Зубчатые колеса являются важной частью многих механизмов и машин. Они используются для передачи вращательного движения и крутящего момента от одного вала к другому. Процесс изготовления зубчатых колес требует высокой точности и качества, чтобы обеспечить плавную и надежную работу механизма.
Существует несколько основных методов изготовления зубчатых колес. Выбор метода зависит от требований к точности, производительности, стоимости и других факторов. Рассмотрим подробнее технологические процессы, используемые при производстве зубчатых колес.
Процесс литья
Один из распространенных способов получения заготовки для последующей механической обработки. Применяется для изготовления зубчатых колес из металлов и сплавов. Перед литьем готовится литейная форма, имеющая полость, повторяющую геометрию будущего колеса. Зубчатое колесо получается путем заливки расплавленного металла в форму и последующего охлаждения.
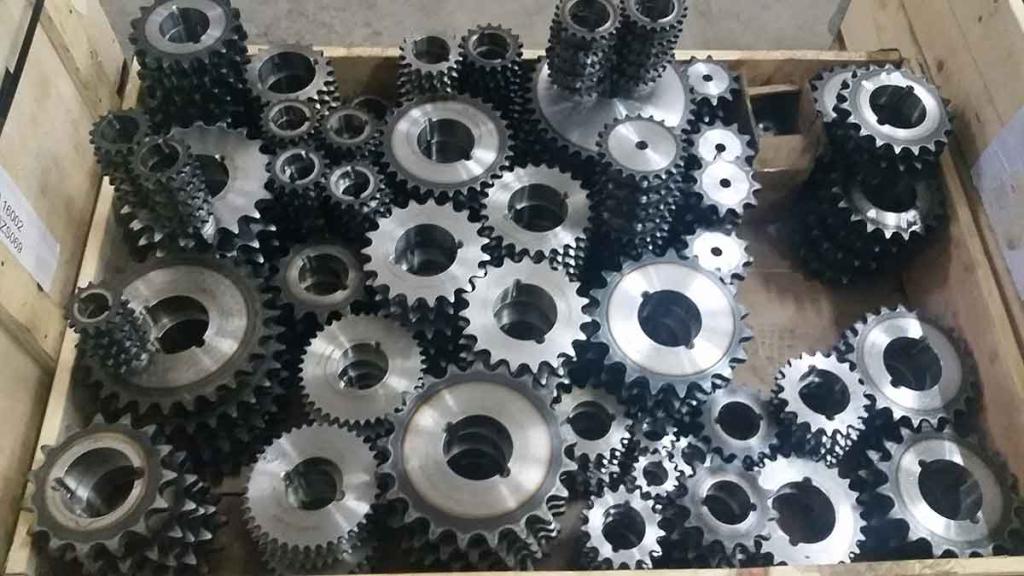
Преимущества литья - высокая производительность и низкая стоимость. Однако точность литых заготовок обычно невысока из-за усадки металла и других факторов. Поэтому литые колеса всегда требуют последующей механической обработки зубьев.
Штамповка и ковка
Это способы получения заготовок для зубчатых колес путем пластической деформации металла. Заготовку вырубают или выдавливают при помощи штампов и прессов. Штампованные заготовки обеспечивают более высокую точность, чем литые.
При холодной штамповке используются штампы и матрицы, повторяющие профиль будущих зубьев. Такая технология позволяет получать колеса малых и средних размеров с достаточно высокой точностью. При горячей штамповке заготовки нагреваются для улучшения пластичности.
Механическая обработка
Этот метод подразумевает постепенное формирование зубьев колеса путем снятия припуска с заготовки режущим инструментом - фрезами, долбяками, шеверами и др. Механическая обработка обеспечивает высочайшую точность зубчатого зацепления, но является более трудоемким и медленным процессом.
Существует несколько разновидностей механической обработки - обкатка, протягивание, долбление, фрезерование. Каждый из этих методов имеет свои особенности и области применения. Например, для точной финишной обработки зубьев часто используется метод протягивания.
Порошковая металлургия
Этот технологический процесс включает прессование заготовки из металлического порошка с последующим спеканием. Получаемые таким образом детали обладают высокой точностью и не требуют большого объема последующей обработки.
Порошковая металлургия эффективна для производства небольших партий сложных зубчатых колес из труднообрабатываемых материалов. Этот метод отличается экономичностью и малым количеством отходов.
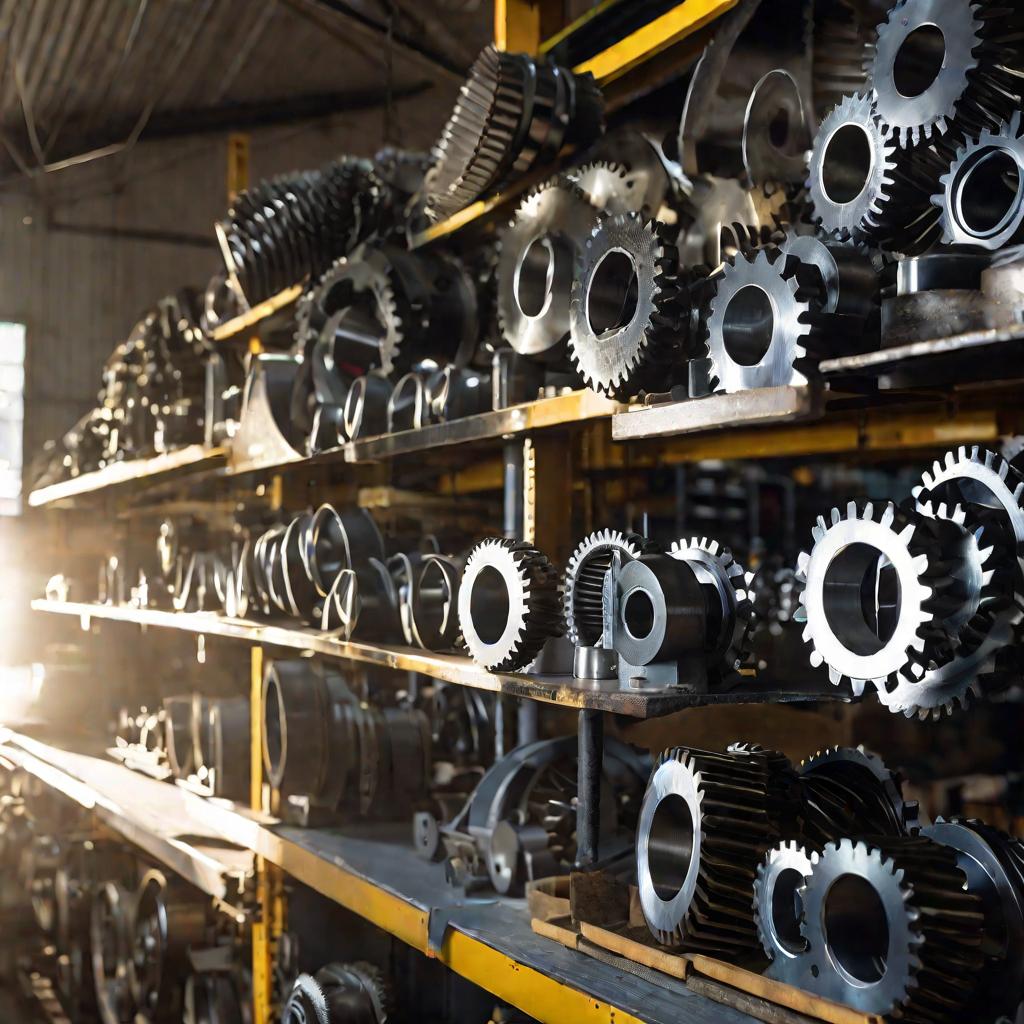
Шлифование
Абразивная обработка применяется как финишная операция при изготовлении зубчатых колес. Шлифование позволяет добиться максимально гладкой поверхности зубьев, устранить микронеровности и дефекты, оставшиеся после предыдущих этапов обработки.
Для шлифования зубчатых колес используют специальные абразивные круги, бруски, ленты. Процесс ведется при высокой точности для получения требуемых допусков и параметров шероховатости поверхности.
Таким образом, при изготовлении зубчатых колес используется целый комплекс технологических методов. Их оптимальное сочетание позволяет получить колеса с требуемыми характеристиками качества, надежности и стоимости.
Выбор материалов
Помимо технологии изготовления, важную роль играет выбор материалов для производства зубчатых колес. Наиболее распространены стали, чугуны и цветные металлы. Конкретный материал подбирается исходя из требований к прочности, износостойкости, весу, стоимости.
Для высоконагруженных зубчатых передач часто используют легированные стали, обладающие повышенной прочностью и твердостью. Детали из чугуна отличаются хорошей вибропоглощающей способностью, но имеют меньшую прочность.
Термообработка зубчатых колес
Для придания необходимых механических свойств деталям зубчатых передач широко применяют различные виды термической и химико-термической обработки: закалку, отпуск, цементацию, азотирование и др.
Термообработка позволяет существенно повысить износостойкость, контактную выносливость, усталостную прочность зубьев. Правильно подобранный режим обработки обеспечивает оптимальное сочетание твердости поверхности и вязкости сердцевины.
Контроль готовых изделий
Модуль зубчатых колес является одним из ключевых параметров, определяющих качество зацепления и передаточное отношение. Поэтому при изготовлении ведется тщательный контроль заданного "модуля".
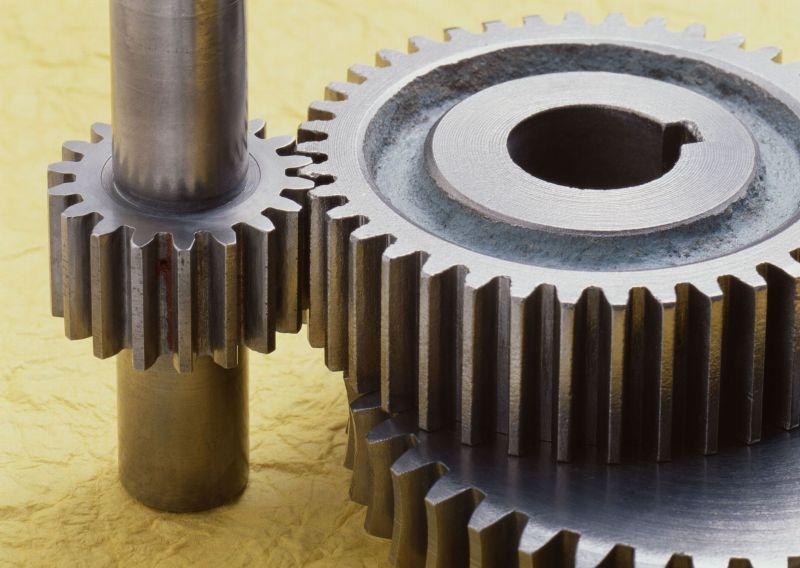
Также проверяются размеры модуля зубчатых колес, форма и взаимное расположение зубьев, шероховатость поверхностей, наличие дефектов. Для контроля используют специальные измерительные инструменты и приборы.
Применение современных технологий
Совершенствование процессов производства зубчатых колес идет по пути внедрения новых технологий. Так, все большее распространение находят методы лазерной и электроэрозионной обработки.
Лазерное изготовление позволяет получать зубья высокой сложности и точности. Электроэрозия дает возможность обрабатывать самые твердые материалы, например, закаленные или керамические.
Применение роботизированных комплексов, автоматизация проектирования и производства также способствуют повышению качества и эффективности изготовления зубчатых колес.
Классификация зубчатых колес
Зубчатые колеса разделяют на различные типы в зависимости от их конструкции и особенностей зацепления.
По форме рабочей поверхности различают "цилиндрические" и конические зубчатые колеса. Цилиндрические имеют зубья, расположенные по параллельным окружностям. Конические зубчатые колеса отличаются тем, что их зубья находятся на поверхности конуса.
По взаимному расположению осей валов выделяют колеса с внешним, внутренним и перекрестным зацеплением.
Материалы для конических колес
Для изготовления конических зубчатых колес обычно применяют те же материалы, что и для цилиндрических. Однако в связи с большими углами наклона зубьев к оси вала к ним предъявляются повышенные требования по изгибной прочности.
Чаще всего конические колеса производят из легированных сталей, имеющих высокие показатели прочности. Также могут использоваться высокопрочные чугуны.
Особенности контроля
При контроле готовых конических зубчатых колес особое внимание уделяется проверке углов конусности, а также радиального и торцевого биения. Эти параметры в значительной степени определяют плавность работы и ресурс конической передачи.
Кроме того, важен контроль взаимного расположения зубьев, их точности и шероховатости. Для измерений используют специализированные приборы и шаблоны.
Применение конических зубчатых колес
Благодаря компактности и возможности передачи движения под углом, конические зубчатые колеса широко используются в машиностроении. Их можно встретить в редукторах, коробках передач, приводах станков, робототехнике.
Правильный подбор и качественное изготовление таких деталей обеспечивает надежность и долговечность всего механизма.
Влияние диаметра на характеристики
"Диаметр" зубчатых колес является одним из основных параметров, влияющих на их работу. С увеличением диаметра повышается передаваемый крутящий момент, но снижаются частота вращения и быстроходность.
При проектировании зубчатых передач подбирают оптимальный диаметр шестерен из условия обеспечения требуемых мощностных и кинематических характеристик механизма.
Особенности смазки
Для уменьшения трения и износа зубьев в процессе эксплуатации зубчатые колеса смазывают специальными маслами или пластичными смазками. Правильный выбор смазочных материалов повышает КПД передачи и продлевает срок службы.
Смазки должны обеспечивать образование прочной масляной пленки, уменьшать трение скольжения и заедание зубьев. Для высоконагруженных или высокоскоростных передач используют синтетические смазочные материалы.
Расчет зубчатых колес
При проектировании зубчатых передач производят расчет основных геометрических параметров колес - модуля, числа зубьев, углов зацепления. Это необходимо для обеспечения требуемых кинематических и силовых характеристик.
Расчет учитывает заданные мощность передачи, передаточное отношение, допустимые напряжения для выбранных материалов. По результатам расчета выполняется рабочее проектирование колес.
Автоматизация проектирования и производства
Современные системы автоматизированного проектирования позволяют быстро и точно проектировать сложные зубчатые колеса, моделируя их работу. Затем 3D-модели используются для настройки станков с ЧПУ или 3D-печати.
Автоматизация сокращает сроки и стоимость разработки, повышает качество. Внедрение robotics в производство также способствует росту производительности и точности при изготовлении зубчатых колес.