Основные типы резцов, классификация и назначение
Самой распространенной операцией при производстве различных деталей является, пожалуй, токарная. Инструментальная промышленность выпускает большое количество разновидностей и типов резцов для обработки тел вращения на токарных станках, а также для растачивания отверстий на координатно-расточных агрегатах и обрабатывающих центрах. Токарная обработка позволяет снимать припуск и получать изделия с цилиндрической и фасонной поверхностью (в том числе резьбовой). Можно также нарезать пруток на заготовки нужной длины.
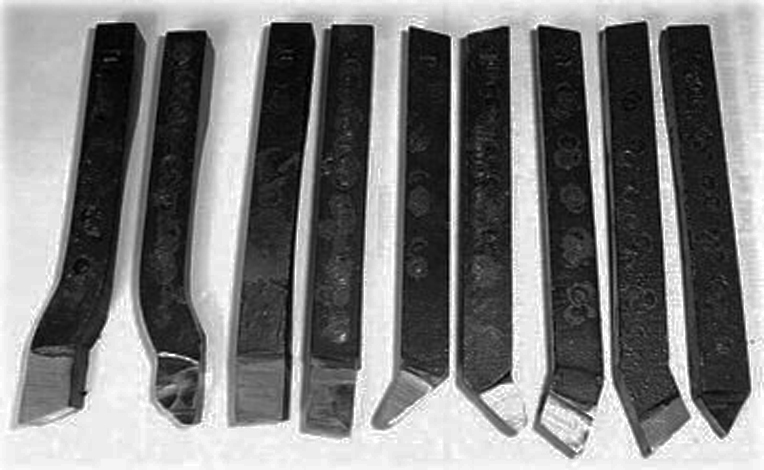
Конструкция резцов для токарной обработки
Несмотря на большое количество типов резцов, все они имеют одинаковые конструктивные элементы. И обычный токарный резец с напайной пластинкой из инструментальной стали, и резец со сменной режущей пластинкой из современных порошковых материалов, схожи между собой по конструкции. У каждого резца имеется державка. Она крепится в револьверную головку токарного станка с ЧПУ или в четырехпозиционное приспособление для крепления инструмента универсального станка.
Для любого типа резца обязательным элементом является также головка, на которую напаивается пластинка из инструментальной стали (типа ТК15). В настоящее время инструмент с напайными пластинами используется очень редко. Предприятия закупают в основном державки резцов с быстросъемными пластинками. Для изготовления таких пластин применяются самые современные материалы, полученные средствами и методами порошковой металлургии.
Общая классификация токарных резцов
В зависимости от формы державки, в сечении различают прямоугольные и круглые резцы. Прямоугольную в сечении державку имеют резцы для обработки наружных поверхностей (резьба, канавки, цилиндр и так далее). Державка округлой формы характерна для резцов, которыми обрабатываются внутренние поверхности (внутренняя резьба, внутренние канавки под стопорные кольца подшипников, отверстия и так далее). Такие типы резцов (с круглой державкой) устанавливаются в револьверную головку через специальный переходник, который позволяет регулировать угол поворота резца вокруг оси с целью совмещения вершины резца с осью вращения заготовки. Если вершина резца не будет совпадать с осью вращения заготовки, то инструмент будет подвержен повышенному износу из-за неправильного схода стружки и увеличенной нагрузки.
Еще один признак, по которому классифицируются токарные резцы, – направление рабочей подачи резания. По данному признаку резцы делят на правые и левые.
В зависимости от вида рабочей части инструмента, резцы бывают прямыми и отогнутыми.
Кроме того, существуют резцы цельного и составного типов. Токарные резцы составного типа являются разборными. Стоимость таких резцов на порядок выше обычного инструмента. Составные головы имеют сложную конструкцию и выполняются из очень дорогих материалов.
Классификация токарного инструмента в зависимости от ориентации относительно заготовки
По данному признаку весь токарный инструмент можно разделить на следующие типы: тангенциальный, параллельный, радиальный.
Тангенциальный инструмент устанавливается к оси вращения заготовки под острым углом. Таким образом получают фаски и другие фасонные поверхности. Теоретически фаски могут точиться путем совмещения продольной и поперечной подач. Однако такой метод требует высокой квалификации токаря и не всегда осуществим.
Параллельная установка используется для рассверливания и растачивания отверстий по оси вращения заготовки со стороны торца.
Радиальная установка используется для точения наружных поверхностей.
Основные типы токарных резцов по металлу
Токарной обработке подвергаются не только металлы и стали, но и другие материалы: древесина, пластик и даже стекло. И, разумеется, не существует таких резцов, которые бы подходили для обработки всех этих материалов. И если раньше быстрорежущая сталь ТК15 (и ее аналоги) использовалась практически повсеместно, то сегодня этот материал не может удовлетворить растущую потребность в качественном и долговечном инструменте. Такие резцы очень быстро тупятся, и их необходимо перетачивать. А это время и деньги на зарплату высококлассного специалиста.
Гораздо более выгодно и удобно использовать резцы со сменными пластинами. Стойкость таких пластин из порошковых композиционных материалов на порядок выше традиционной инструментальной режущей стали. К тому же одна такая пластина может иметь до шести рабочих граней. Пластина позволяет осуществлять обработку с очень большими скоростями резания. Когда рабочая грань приходит в негодность, то достаточно лишь повернуть ее другой стороной. Точность позиционирования такой пластины очень большая, а значит, нет необходимости останавливать оборудование на переналадку.
Инструментальная промышленность освоила производство режущих пластин для широкой гаммы материалов: сталь, медь, алюминий, пластик и так далее. Применение пластин по назначению гарантирует получение задекларированных производителем инструмента долговечности, шероховатости и чистоты обрабатываемой поверхности.
Классификация резцов по виду обработки
В соответствии с установленным и действующим ГОСТом, типы резцов по виду обработки бывают следующими: для черного точения, для чистовой (получистовой) обработки.
Режущая пластина для черновой обдирки поковок и проката имеет большой радиус в вершине, что позволяет за один проход снимать значительный припуск (до 4 миллиметров и более на станке с ЧПУ).
Чистовые пластины, а также пластины для обработки цветных металлов (алюминий и медь) имеют незначительный радиус в вершине резца. Обработка такими пластинами ведется на очень больших оборотах (от тысячи и более единиц в минуту), что позволяет получать очень качественную и чистую поверхность.
По данному признаку можно классифицировать как проходные токарные резцы, так и различные типы расточных резцов.
Описание резьбовых резцов для наружной резьбы
Как понятно из названия, данный резец служит для обработки резьбовых поверхностей.
Резьба может нарезаться как снаружи, так и изнутри. Резьбовой резец для наружной резьбы внешне напоминает проходной прямой тип резца. Отличие лишь в угле заточки – он составляет 60 градусов (если необходимо нарезать метрическую резьбу) или 55 градусов (для получения дюймовой резьбы).
Описание резьбовых резцов для нарезания внутренней резьбы
Резец для нарезания внутренней резьбы внешне очень напоминает инструмент для растачивания внутреннего диаметра отверстий. Отличия все те же: фасонная заточка под определенным углом.
Заточка, а также установка инструмента на станок и его наладка – дело очень сложное. С этой задачей способен справиться лишь специалист с большим опытом подобных работ. Применение резьбовых резцов со сменными пластинками решает эту проблему и существенно упрощает процесс наладки станка.
Характеристика проходных резцов
Проходной резец наиболее часто используется при токарной обработке. Без него просто невозможно придать поковке или заготовке из прутка форму и необходимые для проведения последующих технологических операций размеры. Поэтому проходной относится к основному типу резцов.
Данный вид используется для снятия припуска по наружной поверхности тела вращения, а также для подрезания торцевых поверхностей. Угол в вершине может быть разным: 45, 60, 75 и даже 90 градусов. Значение угла продиктовано назначением резца. Назначение и типы проходных резцов: обдирка, подрезка, чистовая обработка.
Особенности токарных резцов по дереву
Весь токарный режущий инструмент имеет одно предназначение – обработка заготовок (тел вращения) на станках и придание им заданной формы. Но несмотря на это, сам принцип работы инструмента по дереву и сама физика процесса резания разительно отличаются от процессов, протекающих в процессе резания металла.
Главное отличие – незначительное усилие резания. Большинство мастеров столярного дела предпочитают использовать в работе ручной инструмент. Так создается эксклюзивная продукция. А вот для токарной обработки древесины в условиях серийного и массового производства используются так называемые копиры. Суть подобной технологии заключается в следующем: щуп перемещается по шаблону и передает движение рабочему органу станка, в результате чего формируется контур детали.
Следует отметить, что качественное изделие можно получить лишь при ручной обработке. Заготовки, полученные с использованием автоматических и полуавтоматических методов, нуждаются в последующей доводке и шлифовании с полированием.