Методы цементации стали: придание твердости металлу
Цементация стали - процесс насыщения поверхности заготовки углеродом в специальных условиях. Цель - повышение твердости и износостойкости деталей без потери вязкости сердцевины. Статья рассматривает разные методы цементации, параметры процесса, марки стали.
После цементации применяют закалку и низкий отпуск. Это придает нужный комплекс свойств поверхности. Рассмотрим подробнее весь процесс от подготовки стали до конечной термообработки.
Твердый карбюризатор
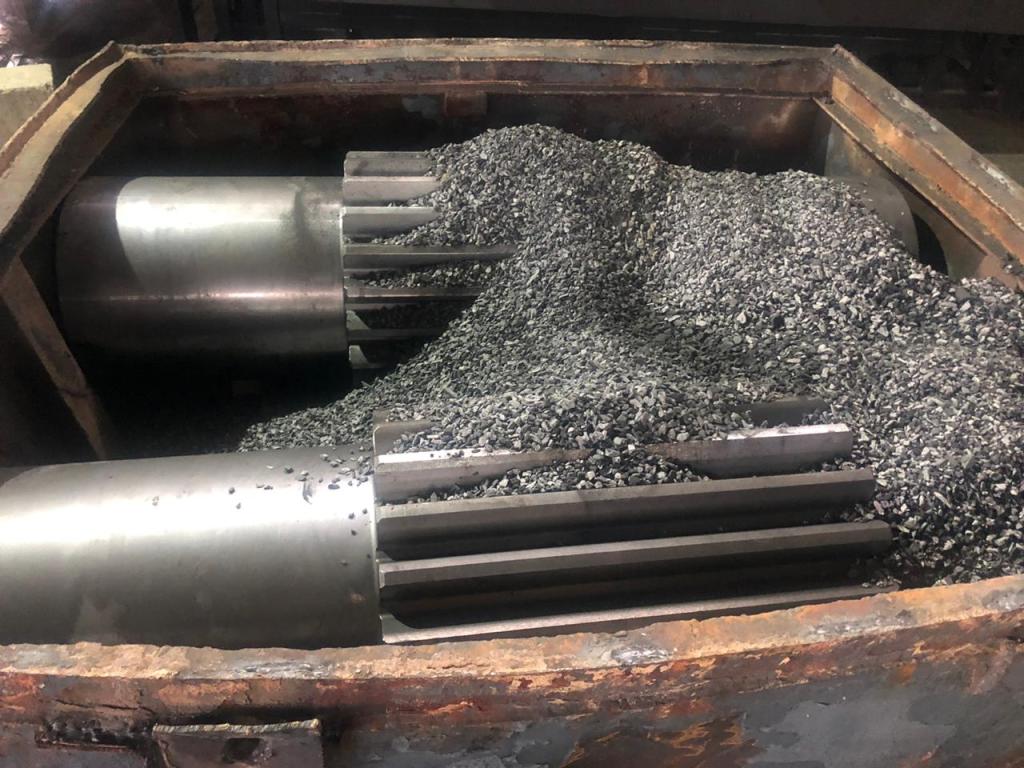
Цементация стали в твердом карбюризаторе - один из наиболее распространенных способов науглероживания стали. В качестве источника углерода используется древесный уголь в зернах диаметром 3,5-10 мм. Процесс проводится при температурах 900-950°C в течение 1 часа на каждые 0,1 мм толщины цементированного слоя цементируемая сталь. Так, для получения слоя толщиной 1 мм требуется выдержка около 10 часов.
Подготовленные детали из цементированной стали помещаются в стальные или чугунные ящики и пересыпаются слоями древесного угля толщиной 2-3 см. Между слоями карбюризатора и деталями оставляется зазор 1-1,5 см. После заполнения ящика его плотно закрывают крышкой и нагревают в печи до требуемой температуры. По окончании процесса ящик медленно охлаждается до 400-500°С, после чего открывается.
Достоинствами цементации в твердом карбюризаторе являются простота оборудования и технологии. Однако этот метод имеет низкую производительность по сравнению с другими видами цементации. Поэтому он применяется в основном в небольших мастерских и для единичного производства.
Газовая цементация
Газовая цементация является одним из наиболее производительных и технологичных способов цементации стали. В качестве источника углерода в этом случае используется газообразный карбюризатор - чаще всего это природный газ, состоящий из метана, пропан-бутановых смесей или жидких углеводородов.
Процесс газовой цементации проводится в печах шахтного типа при температурах 910-930°C. Длительность процесса обычно варьирует от 6 до 12 часов в зависимости от требуемой глубины диффузионного слоя. При использовании газообразного карбюризатора нет необходимости в прогреве инертной насыщающей среды, как в случае с твердым карбюризатором, поэтому время процесса существенно сокращается.
К достоинствам газовой цементации можно также отнести возможность полной автоматизации процесса, хорошую воспроизводимость результатов и управляемость режима насыщения путем изменения состава газовой атмосферы. Кроме того, после газовой цементации можно сразу проводить закалку деталей в печи без их извлечения.
Благодаря всем этим факторам, газовая цементация является оптимальным решением для массового и крупносерийного производства деталей, требующих износостойкости и высокой поверхностной твердости.
Кипящий слой карбюризатора
Цементация стали в кипящем слое карбюризатора базируется на создании в рабочем пространстве печи псевдоожиженного слоя из мелких твердых частиц. В качестве таких частиц обычно используется корунд фракции 0,05-0,2 мм, который помещается на газораспределительную решетку в нижней части рабочего объема.
При пропускании через слой корунда газа, содержащего углерод, со скоростью выше критической частицы теряют контакт друг с другом и начинают активно перемешиваться. Такое состояние напоминает кипение жидкости, откуда и название метода - цементация стали в кипящем слое.
Обрабатываемые детали помещаются в рабочую камеру печи над слоем кипящего абразивного материала. Благодаря интенсивному движению частиц и высокой турбулизации газового потока происходит очень эффективный тепло- и массообмен между деталью и карбюризующей атмосферой.
Время цементации в кипящем слое составляет 1-2 часа на каждый миллиметр толщины диффузионного слоя. Этот метод отличается высокой производительностью и качеством обработки. Однако оборудование для реализации данного процесса является весьма сложным и дорогостоящим.
Электролитическая цементация
Электролитическая цементация основана на использовании эффекта выделения тепла на поверхности детали при пропускании через электролитическую ванну электрического тока. В данном случае сама деталь выполняет роль анода, а в качестве катода могут использоваться различные конструкции.
Температура нагрева поверхности цементируемой стали в процессе электролитической цементации может достигать 1050°С. Такого уровня температур достаточно для эффективной диффузии углерода в поверхностный слой металла. При этом источником углерода служат специальные углеродсодержащие добавки, вводимые в электролит.
К преимуществам метода электролитической цементации стали можно отнести высокую скорость процесса, возможность локального упрочнения, простоту автоматизации. Однако для реализации требуется сложное электролизное оборудование, работающее на высоких токах. Кроме того, существуют определенные ограничения по размерам и конфигурации обрабатываемых деталей.
Тем не менее, этот метод успешно применяется на ряде предприятий и позволяет сократить время цементации по сравнению с традиционными технологиями. Перспективным является совершенствование составов электролитов и режимов обработки для расширения возможностей метода.
Высокочастотный нагрев
Высокочастотная цементация стали основана на использовании выделяющегося в металле детали джоулева тепла при пропускании через нее тока высокой частоты. В качестве источника нагрева применяют генераторы с рабочей частотой от 440 кГц до 13,56 МГц и выходной мощностью от единиц до сотен киловатт.
Нагрев «цементируемых стальных» заготовок при высокой частоте электрического тока характеризуется рядом преимуществ: возможностью автоматизации процесса, локальностью и строгим дозированием тепловой энергии, высоким КПД нагрева, экологичностью.
Скорость цементации стали при высокочастотном нагреве определяется мощностью генератора и размерами детали. Обычно на каждый миллиметр толщины диффузионного слоя требуется около 15-20 минут. Температура нагрева может достигать 1050°C. При этом источником углерода служит порошковая смесь, наносимая на поверхность детали.
К недостаткам высокочастотной цементации можно отнести высокую стоимость силового оборудования и необходимость использования специальных индукторов, повторяющих форму деталей. Тем не менее, данный метод находит применение благодаря своим уникальным достоинствам.
Цементация пастами
Диффузионное насыщение поверхности стали углеродом можно осуществлять с использованием специальных паст и обмазок, содержащих углерод. Такие составы наносятся на цементируемую сталь слоем заданной толщины, после чего производится сушка и нагрев заготовок для диффузии углерода в металл.
В качестве углеродсодержащих соединений в «цементационных пастах» чаще всего используются различные органические вещества - сахар, крахмал, глицерин, лигнин и другие полимеры. Для создания необходимой консистенции пасты в ее состав также вводят наполнители, связующие и пластификаторы.
Процесс цементации стали с использованием углеродсодержащих паст во многом аналогичен процессу цементации в твердом карбюризаторе. Отличие состоит в том, что источником углерода служит нанесенное покрытие, а не окружающая среда. Соотношение толщин пасты и диффузионного слоя обычно составляет 6-8:1.
К преимуществам этого метода относится простота используемых установок, возможность локального науглероживания, хорошее качество поверхностного слоя. К недостаткам - необходимость нанесения и удаления пасты, ограничения на размеры и массу обрабатываемой партии деталей.
Сравнение методов
Существует несколько основных промышленных методов цементации стали, каждый из которых обладает своими достоинствами и недостатками. Выбор конкретного метода зависит от требований к деталям, типа и объема производства.
Наиболее простым и доступным является процесс цементации в твердом карбюризаторе. Он не требует сложного оборудования, однако характеризуется низкой производительностью и возможен только для небольших партий деталей.
Газовая цементация стали более технологична и производительна. Она применяется в массовом производстве, но требует дорогостоящего оборудования и квалифицированного персонала.
Электролитическая цементация, высокочастотный нагрев, использование паст обеспечивают высокое качество обработки и более высокие скорости процесса. Однако эти методы имеют ограничения по размерам и сложности деталей, а также характеризуются повышенными затратами на реализацию.