Манометры - незаменимые помощники во многих областях промышленности, энергетики, транспорта. Они позволяют контролировать давление в гидравлических, пневматических и паровых системах. От правильного выбора и установки манометров зависит безопасная работа дорогостоящего оборудования и комфортные условия для людей.
Назначение и принцип действия манометров
Манометры предназначены для измерения избыточного или вакуумметрического давления газообразных и жидких сред. Принцип действия основан на деформации упругого элемента под воздействием давления. В качестве такого элемента чаще всего используется трубка Бурдона или манометрическая пружина.
Различают абсолютные манометры, измеряющие давление относительно абсолютного вакуума и избыточные (относительные) манометры, измеряющие разность между абсолютным давлением среды и атмосферным.
Основное назначение манометров - обеспечение безопасности технологических процессов, предупреждение аварий и выхода оборудования из строя. Корректные показания манометров необходимы для расчетов баланса давления в системах.
Основные типы манометров
Существует множество типов и модификаций манометров для самых разных отраслей промышленности и науки. Рассмотрим наиболее распространенные из них.
По конструкции
По используемому чувствительному элементу различают манометры с трубкой Бурдона, сильфонные, мембранные и пружинные. Каждая конструкция имеет свои достоинства и недостатки.
Манометры с трубкой Бурдона отличаются высокой чувствительностью и минимальной погрешностью. Их часто используют в системах высокого давления и ответственных измерениях.
Сильфонные манометры выдерживают высокие перегрузки по давлению и устойчивы к агрессивным или загрязненным средам. Поэтому их широко применяют в тяжелых условиях эксплуатации.
Мембранные конструкции просты и обладают хорошей ремонтопригодностью. Их часто используют в качестве показывающих манометров в сочетании с преобразователями давления.
Пружинные манометры отличаются малыми габаритами и удобны для монтажа в ограниченном пространстве. Обычно их применяют для грубых измерений давления вспомогательных систем.
По классу точности
В зависимости от допустимой погрешности манометры делятся на классы точности от 0,1 до 4,0. Чем выше класс точности, тем он дороже, но и тем более точные измерения обеспечивает.
- Класс 0,1...0,6 - лабораторные приборы для эталонных измерений.
- 1,0 - образцовые манометры для поверки других приборов.
- 1,5 и 2,5 - технические и промышленные манометры.
- 4,0 - для неответственных вспомогательных измерений.
При выборе класса точности необходимо ориентироваться на реальные требования конкретного техпроцесса с запасом.
По типу измеряемой среды
По измеряемым средам различают манометры для газообразных и жидких неагрессивных сред, паров, кислот и щелочей, масел и топлива, кислорода. Для каждого типа сред существуют свои конструктивные особенности и материалы, совместимые с этой средой.
Например, мембрана манометра для кислорода делается из специальных фторопластов, которые не взаимодействуют с чистым кислородом.
Важно правильно подобрать тип прибора и материалы, совместимые с контролируемой средой, чтобы обеспечить метрологические характеристики и ресурс работы манометра.
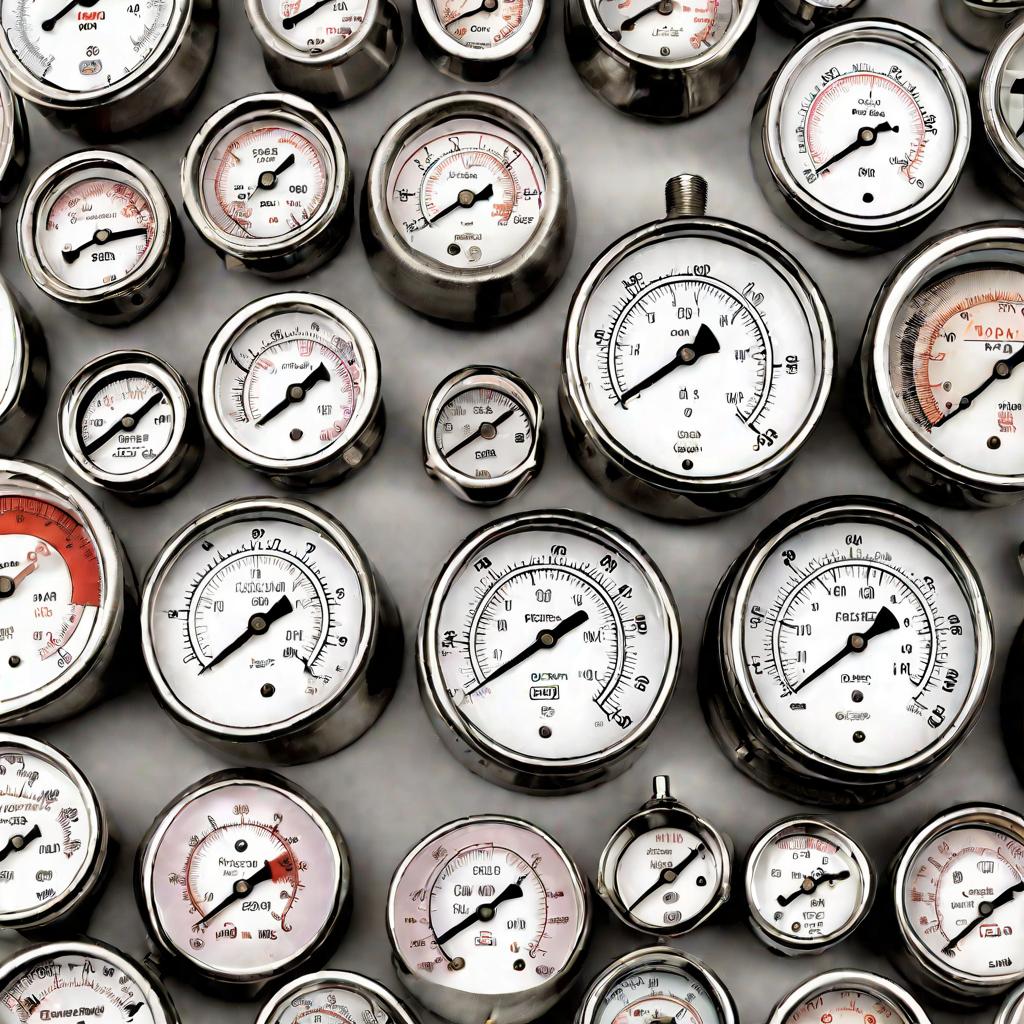
Специального назначения
Помимо стандартных конструкций, существуют манометры для эксплуатации в нештатных и опасных условиях:
- Взрывозащищенные для работы во взрывоопасных средах;
- Виброустойчивые для эксплуатации в условиях вибрации;
- Высокотемпературные для работы при температурах свыше 100°С.
Такие приборы изготавливаются по специальным техническим условиям и проходят дополнительные испытания на соответствие назначению.
Критерии выбора манометра
Правильный выбор манометра является важной и ответственной задачей. От этого зависят корректность измерений параметров техпроцесса, безопасность оборудования и персонала.
Диапазон измерений
Одним из главных параметров при выборе манометра является требуемый диапазон контролируемого давления. Он указывается на шкале в виде начального и конечного значения.
Например, шкала 0...600 кПа соответствует диапазону измерений от 0 до 600 кПа (килопаскалей).
Верхний предел шкалы манометра должен выбираться с запасом от 20 до 100% от максимального рабочего давления в системе. Это позволит избежать выхода прибора из строя при возможных перегрузках.
При долговременной эксплуатации на одном уровне давления рекомендуется выбирать манометры с соответствующей средней шкалой для обеспечения лучшей точности показаний.
Размер корпуса и диаметр шкалы
Стандартный размер корпуса большинства промышленных манометров - 100 или 160 мм. Манометры меньшего размера сложнее считывать, но зато они более компактны.
Для точных лабораторных измерений обычно применяют манометры диаметром 250 мм и больше.
При выборе размера также стоит учитывать удобство считывания показаний и наличие свободного места для монтажа.
Оптимальный диаметр корпуса манометра для промышленности и энергетики - 100, 160 или 250 мм. Приборы меньшего размера хуже читаются, а большего - не всегда возможно разместить в щите.
Климатическое исполнение
Манометры выпускаются в различном климатическом исполнении - от обычного (У) до экстремальных условий Крайнего Севера (ХЛ). Это важно учитывать при выборе для уличного монтажа или неотапливаемых помещений.
Обозначение | Диапазон температур эксплуатации |
У | от -30 до +50 °C |
УХЛ | от -60 до +90 °C |
При выборе исполнения следует ориентироваться на минимальную возможную температуру в помещении, а не среднюю.
Взрывозащищенность
Для применения манометров во взрывоопасных зонах требуется специальное взрывозащищенное исполнение с маркировкой Ex на корпусе.
Оно подразумевает аварийное сбрасывание давления через разрывную мембрану, искробезопасный корпус и ограничение максимальной температуры поверхности.
Выбор типа взрывозащиты (Exd, Exi или Exia) зависит от категории и класса конкретных взрывоопасных зон на объекте.
Правильный подбор взрывозащищенного исполнения манометров критически важен для обеспечения безопасности на производстве.
Манометры для измерения давления
Манометры для измерения давления являются наиболее распространенным типом из всего многообразия этих полезных измерительных приборов. Они применяются повсеместно - на промышленных предприятиях, транспорте, в энергетике, ЖКХ и даже в быту.
Конструктивно большая часть манометров для измерения давления выполняется с трубкой Бурдона - надежной и относительно простой схемой передачи усилия на стрелку. Но есть и другие разновидности - мембранные, сильфонные, пружинные.
Основное назначение манометров для измерения давления - обеспечение безаварийной работы оборудования и технологических систем. Нормальные показания манометра свидетельствуют об отсутствии опасности. А вот отклонения давления от штатных значений - повод для беспокойства и проверки работы системы.
Правила монтажа манометров
Для обеспечения надежной работы и корректности показаний манометров необходимо соблюдать ряд правил при их монтаже. Рассмотрим основные аспекты.
Схемы включения
В зависимости от измеряемой среды и рабочего давления используют прямое или г-образное включение манометров в систему:
- Прямое - до 630 кПа для газообразных неагрессивных сред.
- Г-образное - свыше 630 кПа, а также для химически активных и загрязненных сред.
Г-образная схема защищает прибор от прямого воздействия потока, загрязнений и повышает срок службы.
Защита от перегрузок
Для исключения выхода из строя манометров из-за возможных гидравлических ударов в системе необходимо устанавливать перед ними защитные устройства:
- Стабилизаторы давления;
- Демпферные устройства;
- Мембранные разделители сред;
Такие устройства сглаживают пульсации давления и предохраняют чувствительный механизм манометров от резких перегрузок, которые способны вывести их из строя.
Установка вентилей и кранов
Для удобства монтажа и обслуживания манометров перед ними рекомендуется ставить вентильные блоки, которые позволяют:
- Отключать прибор без нарушения работы системы;
- Сбрасывать давление перед демонтажем;
- Производить поверку и замену манометра.
Выбор места установки
При выборе места для монтажа манометров необходимо учитывать следующие факторы:
- Удобство считывания показаний;
- Вибрация (она затрудняет замеры);
- Температура и влажность окружающего воздуха.
Рекомендуется устанавливать приборы на высоте 1-1,5 м от уровня пола в легкодоступном месте щита.
Поверка и калибровка манометров
Любые средства измерений, в том числе манометры, в процессе работы дают все большую погрешность. Чтобы это не сказывалось на корректности замеров давления, необходимо периодически поверять и калибровать приборы.
Метрологическая поверка
Государственная поверка манометров подтверждает их соответствие метрологическим характеристикам, заявленной точности и работоспособности.
Она необходима после выпуска из производства, после ремонта и периодически в процессе эксплуатации.
Периодичность поверки
Согласно правил по метрологии, манометры подлежат периодической поверке со следующей периодичностью:
- Класс 0,6...2,5 - 1 раз в год;
- Класс 4,0 - 1 раз в 2 года.
Для ответственных измерений рекомендуется поверка каждые 6 месяцев.
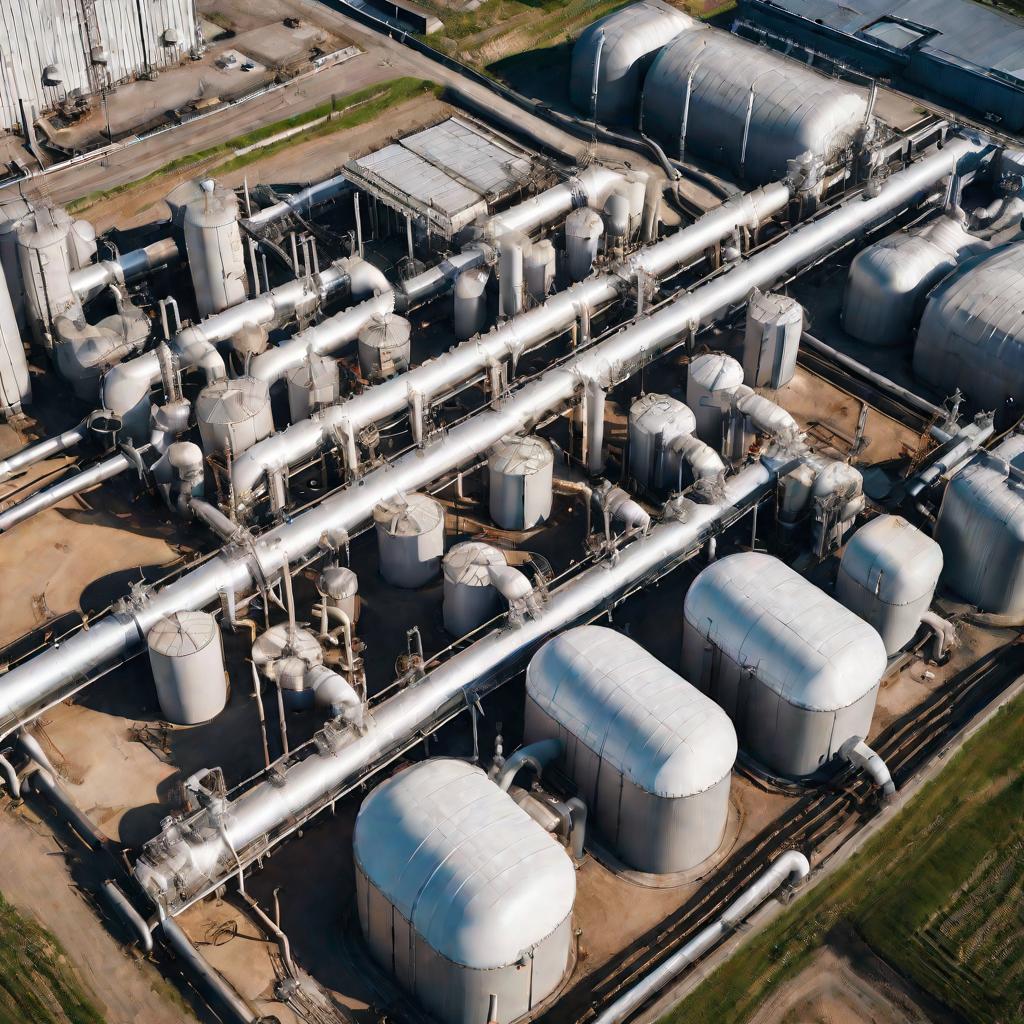
Калибровка рабочих манометров
Помимо обязательной поверки, рекомендуется выполнять калибровку рабочих манометров - сличение показаний с эталонным прибором.
Такая калибровка позволяет выявить отклонения метрологических характеристик в процессе работы и вовремя отрегулировать прибор или заменить его до очередной поверки.
Неисправности манометров и их устранение
К сожалению, даже самые надежные манометры могут выйти из строя. Рассмотрим типичные неисправности и способы их устранения.
Заедание стрелки
Самая распространенная проблема - заедание стрелки. Причин может быть несколько:
- Загрязнение или запыление внутри корпуса;
- Высыхание или загустение смазки;
- Деформация пружин или оси.
В таком случае требуется полная разборка манометра, очистка деталей и смазка оси вращения.
Утечки из системы или корпуса
Еще одна распространенная проблема - течь в местах уплотнений или соединений:
- Негерметичность присоединительного штуцера;
- Трещины или вмятины корпуса;
- Износ или старение прокладок.
В подобных случаях требуется замена прокладок, а иногда и всего прибора в сборе.
Негерметичность прибора
Негерметичность самого механизма манометра приводит к потере точности:
- Течи через стенки напорной трубки или мембраны;
- Нарушение плотности припоя у коромысла или стрелки;
- Износ резьбовых соединений внутри корпуса.
В таких ситуациях приходится полностью заменять вышедший из строя прибор. Ремонт чаще всего нецелесообразен из-за его стоимости по сравнению с ценой нового манометра.
Эксплуатация манометров в опасных условиях
Нередко манометры приходится устанавливать и эксплуатировать в нештатных и опасных условиях: при взрывоопасности, высоких температурах, воздействии агрессивных сред.
Работа в таких экстремальных режимах требует особого подхода.
- Взрывоопасные объекты. Для применения манометров во взрывоопасных зонах обязательны специальное исполнение Ex и выбор соответствующего вида взрывозащиты - искробезопасная электрическая цепь (Exi), защита вида "взрывонепроницаемая оболочка" (Exd) и др.
- Агрессивные среды. При контакте с кислотами, солевыми растворами или другими химически активными веществами материалы манометра должны быть стойкими к их воздействию.
- Высокие температуры. Работа манометров при высокой температуре контролируемой среды требует применения специальных мембран и уплотнений, стойких к нагреву. Кроме того, следует использовать отводы и сильфоны для защиты корпуса от перегрева.