Безопасность и надежность трубопроводного транспорта зависят от множества факторов. Один из ключевых - правильный расчет толщины стенки труб с учетом всех нюансов. Давайте разберем основные моменты этого важного вопроса. Узнаем, какие факторы влияют на толщину и как выполнить расчет. Рассмотрим оптимальный выбор толщины и способы прокладки магистральных трубопроводов. Вперед, к надежности и безопасности!
Основные факторы, влияющие на толщину стенки
На толщину стенки трубопровода влияет целый ряд факторов:
- Внутреннее давление. Чем выше давление в трубопроводе, тем толще должна быть стенка для обеспечения прочности.
- Свойства материала труб. Например, сталь с более высоким пределом текучести позволяет использовать меньшую толщину.
- Коррозия внешняя и внутренняя. Для компенсации коррозионного износа требуется дополнительная толщина стенки.
- Термические нагрузки при нагреве, охлаждении, перепадах температуры. Это также влияет на выбор толщины.
- Агрессивность среды и перекачиваемого продукта. Чем сильнее коррозионное воздействие, тем больше толщина.
- Расчетный срок эксплуатации трубопровода. Для длительного срока службы может требоваться увеличение толщины.
Все эти факторы учитываются при выборе толщины стенки трубопровода на стадии проектирования.
Нормативные требования к толщине стенки труб
Требования к толщине стенки трубопроводов регламентируются нормативными документами. В России основным документом является ГОСТ Р 54539-2011 «Нефтепродукто- и газопроводы. Нормы проектирования».
Аналогичные стандарты разработаны в США, Европе и других странах. Хотя подходы в целом схожи, есть и некоторые отличия.
Для магистральных трубопроводов обычно устанавливают более жесткие требования к толщине стенки по сравнению с промысловыми и технологическими трубопроводами.
Перед началом эксплуатации должны проводиться испытания опытных образцов труб при различных давлениях для подтверждения соответствия нормативным требованиям.
Этапы расчета толщины стенки
Расчет толщины стенки трубопровода включает следующие основные этапы:
- Определение исходных данных:
- диаметр и длина трубопровода; внутреннее рабочее давление; расчетный срок эксплуатации; свойства материала труб; параметры окружающей среды; характеристики перекачиваемой среды.
- Выбор методики расчета в соответствии со стандартом.
- Расчет по выбранной формуле с использованием коэффициентов.
- Выбор стандартной толщины стенки с учетом необходимых припусков.
Для неметаллических труб, например стеклопластиковых, методика расчета имеет некоторые особенности.
Таким образом, расчет толщины - это комплексный процесс с учетом множества факторов, требующий привлечения высококвалифицированных специалистов.
Оптимальный выбор толщины стенки позволяет обеспечить надежность и безопасность трубопровода при минимизации затрат.
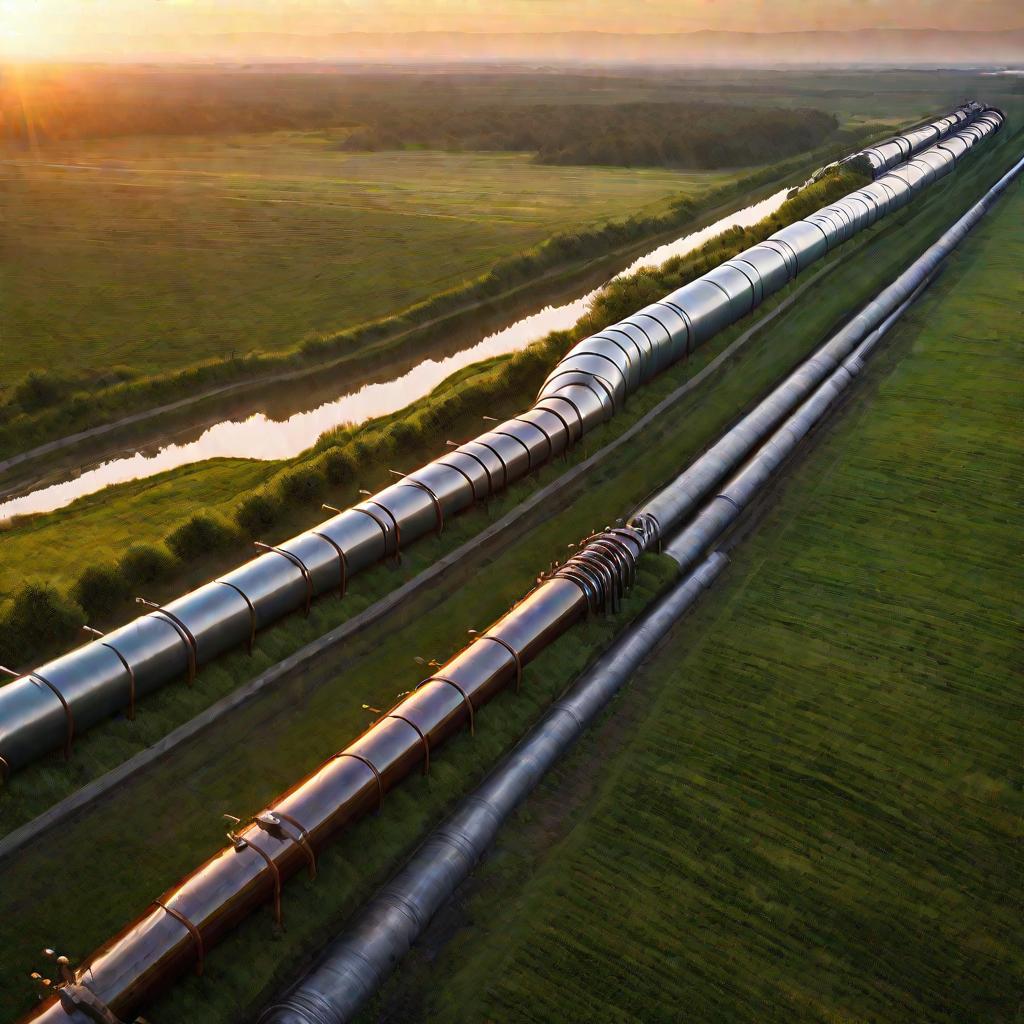
Выбор оптимальной толщины стенки
После расчета толщины стенки согласно нормативным требованиям, необходимо выбрать оптимальное значение из ряда стандартных.
При этом учитываются следующие факторы:
- Прочность и надежность трубопровода.
- Стоимость труб разной толщины.
- Влияние на гидравлические потери.
- Обеспечение необходимой жесткости и сопротивления изгибу трубопровода.
- Минимизация общей массы трубопровода.
Исходя из этих критериев, можно дать следующие рекомендации:
- Для технологических трубопроводов предпочтительны меньшие толщины стенки.
- Для магистральных трубопроводов важнее обеспечить надежность.
- Оптимальный выбор - наименьшая толщина, удовлетворяющая нормативам.
Контроль качества труб и сварных соединений
После изготовления трубопровода, необходимо провести входной контроль качества.
Для этого применяют различные методы неразрушающего контроля:
- визуальный и измерительный контроль геометрии труб;
- радиография для выявления внутренних дефектов;
- ультразвуковая дефектоскопия сварных швов.
Трубопровод может быть принят в эксплуатацию только при полном соответствии нормативным требованиям. В процессе эксплуатации проводится периодическая диагностика, выполняются ремонтные работы по замене отдельных дефектных участков.
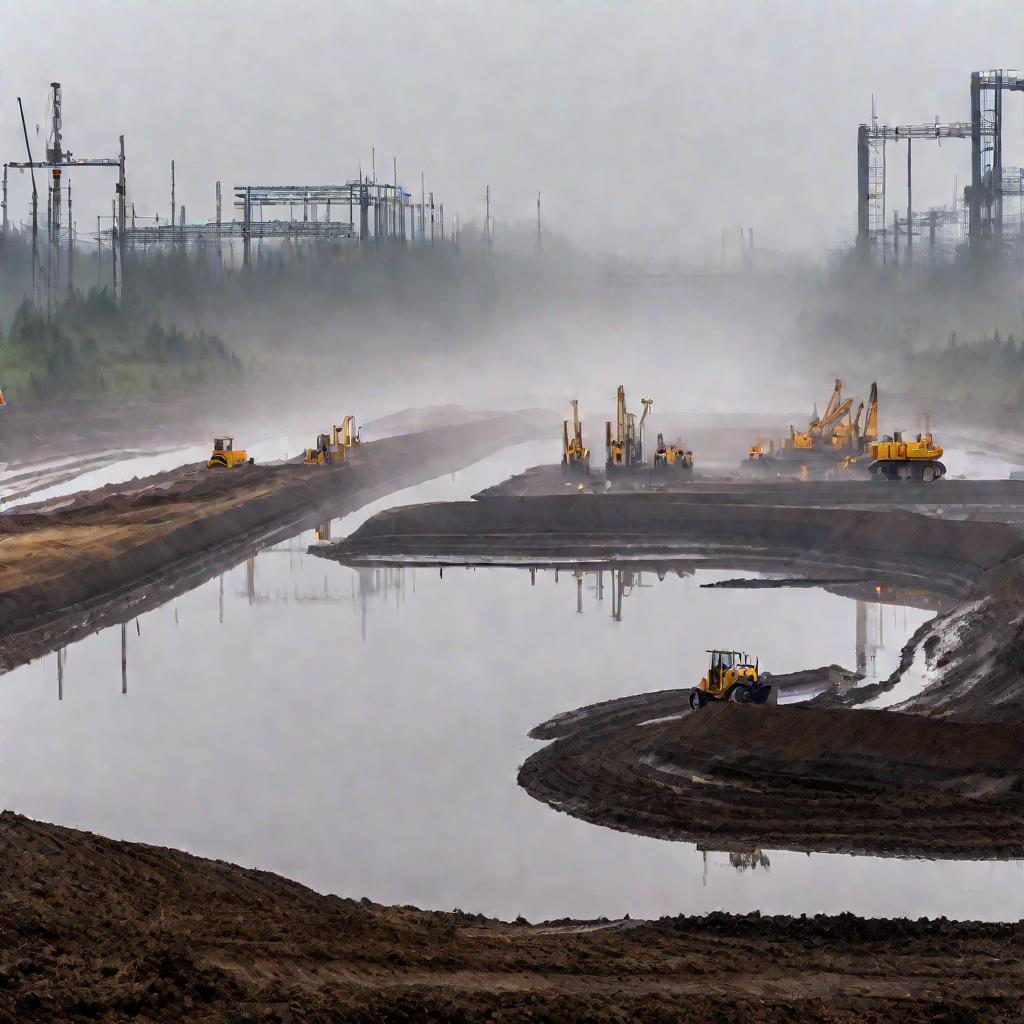
Способы прокладки магистральных трубопроводов
Существуют различные способы прокладки магистральных трубопроводов:
- Подземная прокладка в траншее.
- Наземная прокладка на опорах.
- Подводные переходы в защитных футлярах.
- Прокладка в болотистой местности с использованием насыпей.
- Устройство переходов через реки и овраги.
Выбор конкретного способа зависит от рельефа местности, грунтовых условий, наличия водных преград. Учитывается также стоимость строительства и эксплуатации трубопровода.
Правильный выбор способа прокладки позволяет оптимизировать затраты и обеспечить надежность трубопровода.
Особенности прокладки трубопроводов в болотистой местности
При прокладке трубопроводов в болотистых районах применяют специальные технические решения.
Чаще всего используют прокладку трубопровода по насыпи из песка, гравия или другого грунта. Высота насыпи должна превышать уровень болота не менее чем на 1 метр.
Для устойчивости насыпи по ее периметру укладываются специальные геотекстильные материалы или выполняется уплотнение грунта.
В отдельных случаях возможно сооружение опор из свай. На них монтируются надземные участки трубопровода.
Требования к глубине заложения подземных трубопроводов
Глубина заложения подземного трубопровода регламентируется нормативными документами.
Обычно глубина заложения составляет:
- не менее 0,8 м до верха трубы - на болотах;
- не менее 1 м - на пахотных угодьях;
- не менее 1,5 м - при пересечении автодорог;
- не менее 2 м - на участках возможных нарушений.
Большая глубина заложения уменьшает риск повреждений трубопровода и обеспечивает его сохранность.
Методы укрепления грунта при строительстве трубопроводов
Для повышения несущей способности грунтового основания трубопровода используют различные методы его укрепления:
- Уплотнение грунта катками или трамбовками.
- Устройство песчано-гравийной или щебеночной подготовки.
- Химическое или термическое закрепление грунта.
- Устройство георешеток или геотекстиля.
- Использование различных грунтоцементов.
Выбор метода зависит от типа грунта, нагрузок и других факторов. Это позволяет существенно повысить надежность трубопровода.
Организация защиты трубопроводов от коррозии
Для предотвращения коррозионного повреждения подземных стальных трубопроводов применяют:
- Изоляцию полимерными лентами или мастиками.
- Электрохимическую защиту катодной поляризацией.
- Протекторную защиту с помощью жертвенных анодов.
- Использование труб из коррозионно-стойких материалов.
Комплекс мер защиты обеспечивает значительное увеличение срока службы подземного трубопровода.
Особенности эксплуатации трубопроводов большого диаметра
При эксплуатации трубопроводов большого диаметра, например 1200-1400 мм, возникает ряд особенностей.
Из-за значительных габаритов и веса увеличивается сложность транспортировки и монтажа труб. Требуется применение мощной спецтехники и грузоподъемных механизмов.
Повышаются требования к прочности и устойчивости опорных конструкций и несущей способности основания трубопровода.
Усиливаются меры по защите от вибрации, вызванной пульсациями потока жидкости или газа.
Увеличивается опасность возникновения гидравлического удара. Необходимо тщательное регулирование режимов работы и параметров перекачки.
Нормативные требования к испытаниям трубопроводов
Испытания трубопроводов на прочность и герметичность являются обязательными.
Согласно СП 36.13330.2012, испытания должны проводиться:
- Гидравлическим давлением, равным 1,25 рабочего давления.
- В течение 6 часов для надземных участков.
- В течение 24 часов для подземных участков.
Кроме того, перед вводом в эксплуатацию выполняют контроль качества сварных стыков радиографическим или ультразвуковым методом.
Методы врезки и присоединения вновь построенного участка трубопровода
Для врезки и присоединения нового участка трубопровода используются следующие основные методы:
- Установка вставки с запорной арматурой и последующей сваркой стыков.
- Врезка под давлением с помощью спецоборудования.
- Устройство камеры запуска-приема очистных устройств с последующим соединением.
Выбор метода зависит от диаметра, давления, конструкции трубопровода и других факторов.
Причины возникновения дефектов при эксплуатации трубопроводов
Основными причинами возникновения дефектов трубопроводов в процессе эксплуатации являются:
- Коррозия под воздействием агрессивной среды.
- Механические повреждения из-за деформаций грунта.
- Температурные деформации при перепадах температур.
- Вибрация трубопровода при пульсациях давления среды.
- Ошибки при монтаже, сварке и других работах.
Своевременное устранение дефектов крайне важно для обеспечения надежности и предупреждения аварийных ситуаций.
Пример расчета толщины стенки трубопровода
Рассмотрим пример расчета толщины стенки для трубопровода из стали марки 09Г2С диаметром 720 мм, длиной 10 км. Рабочее давление 11 МПа, срок эксплуатации 30 лет.
- Определяем исходные данные:
- Наружный диаметр D = 720 мм
- Рабочее давление P = 11 МПа
- Предел текучести стали S = 353 МПа
- Коэффициент надежности по материалу n = 1,1
- Рассчитываем толщину стенки по формуле: t = (P*D) / (2*S*n) = (11*720) / (2*353*1,1) = 10,2 мм
- Выбираем ближайшую стандартную толщину с учетом припусков на коррозию - 12 мм.
Таким образом, принимаем толщину стенки труб равной 12 мм.
Факторы, влияющие на минимальную толщину стенки трубопровода
На величину минимально допустимой толщины стенки трубопровода влияют:
- Внутреннее давление среды.
- Наружный диаметр трубопровода.
- Механические свойства материала труб.
- Коэффициент запаса прочности.
- Величина допускаемых напряжений.
- Требуемый срок эксплуатации.
- Особенности транспортируемой среды.
Увеличение давления, диаметра, срока службы ведет к необходимости утолщения стенки. Использование более прочных материалов позволяет принимать меньшую толщину.
Способы восстановления изношенных участков трубопровода
Для восстановления изношенных или поврежденных участков стальных трубопроводов применяют:
- Замену дефектного участка на новый с последующей сваркой.
- Установку муфт или заплат сварными, фланцевыми или механическими.
- Наплавку дефектных участков специальными материалами.
- Установку композитных ремонтных конструкций.
Выбор способа зависит от размера, типа и расположения дефекта. Комплексный подход позволяет значительно продлить срок службы трубопровода.
Контроль технического состояния трубопроводов
Для поддержания трубопроводов в работоспособном состоянии проводится регулярный контроль их технического состояния.
Основные методы контроля:
- Визуальный осмотр трассы.
- Замер толщины стенок труб.
- Диагностика сварных стыков и фитингов.
- Испытания на прочность и герметичность.
- Оценка опасных деформаций трубопровода.
По результатам контроля принимаются меры по ремонту или замене непригодных элементов трубопровода.
Методы предотвращения разрушения трубопроводов от коррозии
Для защиты трубопроводов от коррозии применяют:
- Изоляцию полимерными покрытиями.
- Электрохимическую защиту.
- Протекторную защиту жертвенными анодами.
- Ингибиторы коррозии в транспортируемой среде.
- Стабилизационную обработку воды.
Комплекс мер защиты позволяет значительно увеличить срок службы трубопроводов, подверженных коррозионному воздействию.
Требования к охранным зонам трубопроводов
Для обеспечения нормальных условий эксплуатации и исключения повреждений трубопроводов устанавливаются охранные зоны:
- Для магистральных газопроводов - 25 м в обе стороны от оси.
- Для магистральных нефтепроводов - 25 м в обе стороны от оси.
- Для технологических трубопроводов - по 5 м в обе стороны.
В охранных зонах запрещено производить строительство, посадку деревьев, разводить огонь и другие опасные действия.
Особенности прокладки трубопроводов в сейсмоопасных районах
При прокладке трубопроводов в районах с сейсмической активностью предусматриваются специальные мероприятия:
- Увеличение глубины заложения трубопровода.
- Использование изогнутых в плане трасс для гашения волн.
- Установка компенсаторов для снятия напряжений.
- Усиление несущих конструкций опор и повышение их степени надежности.
Соблюдение сейсмостойких норм проектирования снижает риск разрушений трубопроводов при землетрясениях.