Термическая обработка позволяет существенно улучшить физико-механические характеристики стальных изделий. Правильный подбор режимов нагрева, выдержки и охлаждения способствует повышению твердости, прочности, вязкости, усталостной долговечности деталей. Освоение эффективных методов термообработки - залог выпуска качественной металлопродукции.
Сущность термической обработки стали
Термическая обработка стали - это контролируемый нагрев до определенной температуры с последующим охлаждением по заданному режиму. Цель - изменение структуры металла для придания ему необходимого комплекса служебных свойств.
Основные виды термообработки:
- Отжиг
- Нормализация
- Закалка
- Отпуск
Кроме того, существует специальная термическая обработка сварных соединений для снятия напряжений и улучшения структуры металла в зоне шва.
Основные цели термической обработки
Главные цели, которые преследуют при термообработке:
- Повышение твердости, прочности и износостойкости
- Устранение внутренних напряжений
- Улучшение обрабатываемости резанием или давлением
- Придание специальных свойств (жаропрочность, коррозионная стойкость и др.)
Например, после сварки или литья в металле возникают остаточные напряжения, которые могут привести к короблению или растрескиванию изделий. Поэтому часто требуется провести отжиг или нормализацию.
Термическая обработка стали
Термическая обработка стали является важнейшим этапом в технологии изготовления ответственных деталей машин, механизмов, инструмента. Без термообработки практически невозможно обеспечить требуемый комплекс служебных характеристик таких изделий.
Например, закалка с высоким отпуском повышает твердость инструментальной стали ХВГ в 3-4 раза по сравнению с отожженным состоянием.
Поэтому корректный выбор вида термообработки имеет принципиальное значение.
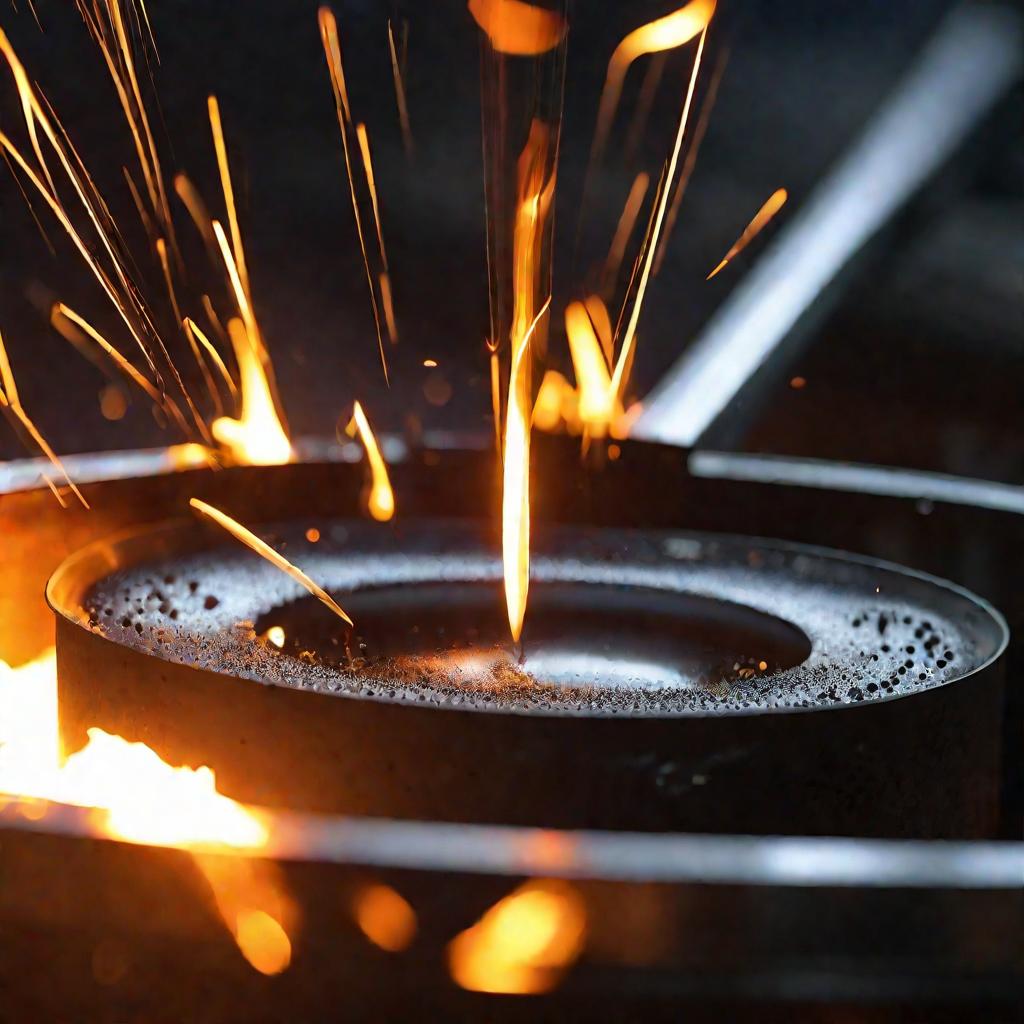
Виды термической обработки стали
"термическая обработка стали" включает несколько основных видов, каждый из которых позволяет решать определенные задачи:
- Отжиг - снижение внутренних напряжений, повышение пластичности
- Нормализация - выравнивание структуры после литья или сварки
- Закалка - резкое повышение твердости и прочности
- Отпуск - снятие части напряжений после закалки, регулирование твердости и вязкости
Механизмы структурных превращений при закалке стали
Основные механизмы изменения структуры стали при закалке:
- Мартенситное превращение - переход аустенита в мартенсит
- Бейнитное превращение - образование промежуточных фаз (нижний и верхний бейнит)
Скорость охлаждения при закалке должна быть выше критической, чтобы подавить диффузионные превращения в твердом растворе и зафиксировать неравновесную структуру.
Режимы термической обработки различных сталей
Режим термообработки (скорости нагрева, температура и выдержка, скорости охлаждения) зависит от:
- Химического состава стали
- Размеров и формы детали
- Требований к свойствам
- Вида предшествующей и последующей обработки
Среды для закалки
Для интенсификации охлаждения при закалке применяют различные среды:
- Вода
- Масло
- Полимерные растворы
- Расплавленные соли
- Воздух или инертный газ
Выбор закалочной среды влияет на скорость охлаждения, величину закалочных напряжений и качество поверхности.
Контроль результатов термической обработки
Для оценки результатов термообработки используют следующие методы:
- Замер твердости
- Испытание на растяжение и ударный изгиб
- Металлографический анализ
- Ультразвуковой контроль
При обнаружении дефектов проводят корректировку режима термообработки.

Оборудование для термической обработки
Для нагрева металла при термообработке применяют различные типы печей и установок:
- Камерные печи
- Проходные роликовые печи
- Индукционные установки
- Электронно-лучевые установки
- Плазменные установки
Выбор оборудования зависит от типоразмера и массы деталей, требуемых температур нагрева, производительности и стоимости.
Автоматизация процессов термообработки
Для автоматизации процессов термообработки применяют:
- Системы программного управления печами
- Устройства для механизированной загрузки и выгрузки
- Системы контроля температурных режимов
- Роботизированные комплексы
Автоматизация повышает стабильность режимов термообработки, снижает брак и повышает производительность труда.
Термическая обработка сварных соединений
После сварки для снятия напряжений применяют:
- Отжиг при 600-650°C
- Местный нагрев сварного шва
- Термическое упрочнение сварного соединения
Режим термообработки швов выбирают в зависимости от марки стали, толщины металла, формы конструкции.
Направления совершенствования термообработки
Основные направления развития технологий термической обработки:
- Создание новых видов термообработки
- Разработка оптимальных режимов для различных сталей
- Совершенствование систем контроля и автоматизации
Это позволит расширить области применения термообработки и повысить качество металлоизделий.
Выбор вида термообработки в зависимости от назначения детали
Для режущего инструмента, как правило, применяют закалку с высоким отпуском для получения оптимального сочетания твердости, вязкости и стойкости.
Детали, работающие на износ, подвергают закалке и низкому отпуску для максимальной твердости поверхностного слоя.
Ответственные крепежные изделия после закалки обычно подвергают среднему отпуску с целью снятия части напряжений и придания необходимого комплекса механических свойств.
Контроль твердости деталей после термообработки
Контроль твердости после ТО осуществляют с помощью:
- Переносных твердомеров Роквелла или Бринелля
- Стационарных стендов для автоматизированного контроля
- Метода вдавливания алмазного наконечника (Виккерса)
Твердость замеряют как на поверхности детали, так и на спиле в сердцевине металла после разрезки или сверления отверстия.
Контроль внутренних напряжений и структуры после ТО
Для контроля остаточных внутренних напряжений используют:
- Магнитные методы (коэрцитиметрия)
- Ультразвуковой метод
- Рентгеновская дифрактометрия
Анализ микроструктуры проводят с помощью металлографического микроскопа на шлифах, вырезанных из различных участков детали.
Подбор среды закалки в зависимости от размеров детали
Для массивных деталей используют закалку в масле, расплавах солей или воздухе. Для деталей небольших размеров применяют воду, водные растворы полимеров, иногда жидкий азот.
Скорость нагрева металла при термообработке влияет на качество изделия. Слишком медленный нагрев может привести к избыточному окислению и обезуглероживанию поверхности, а слишком быстрый - к перегреву отдельных участков.
Рекомендуется выбирать скорость нагрева в пределах 100-400 °С/ч в зависимости от марки стали, размеров детали и типа печи.
Рекомендации по скорости охлаждения при разных видах закалки
При непрерывной закалке обычно используют скорость охлаждения 100-300 °С/сек. При ступенчатой закалке скорость выше - до 1000 °С/сек.
Слишком высокая скорость приводит к появлению трещин, а недостаточно быстрое охлаждение не обеспечивает требуемой твердости.
Рекомендации по температуре отпуска стали после закалки
Температура отпуска подбирается в зависимости от требуемой твердости детали и марки стали в диапазоне 150-700 °С.
Отпуск при более низких температурах (до 350°С) используют, когда нужно сохранить высокую твердость. Более высокие температуры применяют для снижения хрупкости и роста пластичности.
Предварительный подогрев перед закалкой
Для снижения скорости охлаждения крупных деталей иногда используют предварительный подогрев до 300-500°С перед собственно нагревом под закалку. Это позволяет уменьшить термические напряжения в детали.
Требования безопасности при проведении термообработки
При проведении работ по термической обработке стали необходимо соблюдать требования пожарной безопасности, использовать СИЗ, осуществлять периодический контроль состояния оборудования и качества воздушной среды.
Влияние легирующих элементов на скорость закалки стали
Легирующие элементы влияют на критическую скорость охлаждения при закалке. Например, высоколегированные инструментальные и нержавеющие стали могут закаливаться на воздухе.
Хром, никель, марганец замедляют превращение аустенита и снижают минимальную скорость охлаждения в 3-4 раза.
Особенности закалки сварных конструкций
Перед закалкой сварных конструкций рекомендуется предварительно проводить отжиг при 650-700°С для снятия остаточных напряжений и устранения коробления.
Температура закалки устанавливается на 50-100°С выше линии рекристаллизации для конкретной марки стали.
Совершенствование операций технологического цикла после ТО
"термическая обработка стали" часто сопровождается короблением и окислением. Для минимизации этого необходимо контролировать режим охлаждения и проводить соответствующую мехобработку (шлифовку, дробеструйную обработку и т.д.)
Использование защитных атмосфер при термообработке
Для улучшения качества термообработанных изделий можно в печах использовать защитный вакуум или атмосферу инертного газа (аргона, гелия). Это позволяет минимизировать окисление поверхности металла.
Управление свойствами стали поверхностного слоя
Избирательное упрочнение формообразующих элементов режущего инструмента возможно при комбинированной термической и химико-термической обработке. Например, после азотирования или цианирования можно провести высокий отпуск.