Наплавочные электроды являются незаменимым инструментом для восстановления и упрочнения деталей машин, работающих в условиях абразивного изнашивания, ударных нагрузок и коррозионного воздействия. Благодаря наплавке можно многократно продлить срок службы оборудования по сравнению с заменой изношенных деталей. В этой статье мы подробно рассмотрим особенности наплавочных электродов, чтобы читатель мог грамотно подобрать и использовать эти материалы.
1. Общие сведения о наплавочных электродах
Наплавочные электроды предназначены для нанесения на поверхность металлической детали слоя металла с особыми физико-механическими свойствами. Цель наплавки - восстановить изношенные поверхности деталей или придать им специальные рабочие качества, такие как:
- Повышенная износостойкость
- Коррозионная стойкость
- Жаростойкость
- Жаропрочность
- Ударная вязкость
Преимущества наплавки электродами:
- Возможность локального нанесения слоя на нужный участок детали
- Высокая производительность процесса
- Низкая стоимость оборудования и материалов
- Простота технологии
- Возможность автоматизации
Сегодня наплавка - это неотъемлемая часть ремонтных работ и восстановления деталей во всех отраслях промышленности.
2. Классификация наплавочных электродов
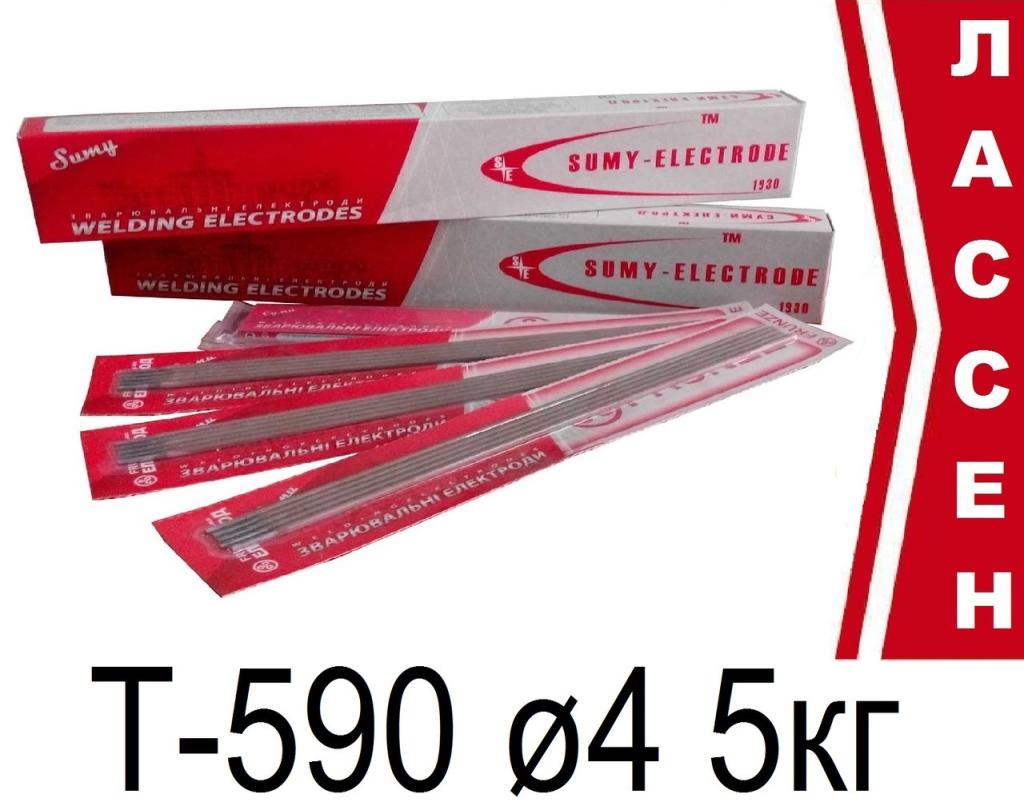
Наплавочные электроды классифицируются по назначению и по маркам. По назначению различают следующие основные группы:
- Износостойкие
- Коррозионностойкие
- Жаростойкие
- Жаропрочные
- Универсальные
Наиболее распространенная классификация по маркам в соответствии с ГОСТ:
- Т-590 - износостойкая наплавка углеродистых и низколегированных сталей
- Т-620 - износостойкая наплавка чугунных деталей
- Т-652 - жаростойкая наплавка стали
- Т-622 - наплавка высокохромистыми сплавами
- Нп-30ХГСА - наплавка инструментальных и штамповых сталей
Наплавочные электроды Т-590 являются наиболее популярной универсальной маркой, применяемой для восстановления стальных деталей, работающих в условиях абразивного изнашивания. Другие марки используются для специальных целей.
Маркировка наплавочных электродов состоит из буквенного кода и цифр, которые указывают диаметр и обозначают основу электрода, тип покрытия, примерное содержание легирующих элементов.
Пример | Значение |
Т-590 | Т - тип покрытия, 590 - марка основного металла |
5 | Диаметр электрода 5 мм |
Таким образом, электрод Т-590-5 - наплавочный электрод диаметром 5 мм для износостойкой наплавки.
3. Химический состав наплавочных электродов
Химический состав наплавочных электродов определяет свойства получаемого наплавленного металла. Он содержит следующие основные легирующие элементы:
- Хром (Cr) - повышает износостойкость, коррозионную стойкость, твердость
- Никель (Ni) - повышает вязкость и ударную прочность
- Марганец (Mn) - улучшает обрабатываемость
- Кремний (Si) - повышает прочность
Для износостойкой наплавки рекомендуется содержание:
- Хрома 20-30%
- Никеля до 5%
- Марганца 1-2%
- Кремния 0,5-1%
Например, химический состав электродов наплавочные электроды Т-590:
Элемент | Содержание, % |
Fe | основа |
C | 2,5-3 |
Cr | 27-32 |
Si | 0,4-0,8 |
Mn | 0,5-1,2 |
Подобранный химический состав обеспечивает требуемый комплекс свойств наплавленного слоя.
4. Физико-механические свойства наплавочных электродов
Основные физико-механические свойства наплавочных электродов и наплавленного ими металла:
- Твердость
- Износостойкость
- Коррозионная стойкость
- Ударная вязкость
- Трещиностойкость
Наплавочные электроды характеристики твердости наплавленного металла зависят от марки электрода и составляют 45-65 HRC.
Износостойкость определяется содержанием твердых карбидов хрома, вольфрама, молибдена. Чем их больше, тем выше износостойкость.
Коррозионная стойкость обеспечивается наличием хрома в наплавленном металле. Для антикоррозионной наплавки применяют электроды с 18-22% Cr.
Ударная вязкость и трещиностойкость зависят от присадок никеля, марганца, кремния. Их оптимальное сочетание обеспечивает комплекс свойств наплавленного слоя.
5. Технология наплавки
Различают следующие виды наплавки:
- Ручная дуговая наплавка
- Механизированная наплавка
- Автоматическая наплавка
Для ручной наплавки используют сварочные трансформаторы или инверторы. Механизированная наплавка выполняется полуавтоматами. Автоматическая наплавка требует специальных установок.
Перед наплавкой поверхность очищается от загрязнений. Рекомендуется наплавлять тонкими валиками или слоями толщиной до 3 мм на слой.
Положение электрода должно обеспечивать формирование равномерного валика. Скорость наплавки зависит от марки электрода и толщины слоя.
При многослойной наплавке каждый последующий слой наплавляют после остывания предыдущего, чтобы избежать перегрева.
6. Наплавочные электроды ОЗН-6
Электроды марки ОЗН-6 предназначены для антикоррозионной наплавки деталей из углеродистых и низколегированных сталей.
Их особенности:
- Высокое содержание хрома (18-22%)
- Повышенная коррозионная стойкость наплавленного металла
- Применяются для защиты от электрохимической и химической коррозии
- Используются в химической и пищевой промышленности
Электродами ОЗН-6 выполняют наплавку емкостного оборудования, трубопроводов, насосов, арматуры для защиты от воздействия кислот, щелочей, солевых растворов.
7. Выбор режимов наплавки
Характеристики электродов влияют на выбор оптимальных режимов наплавки:
- Сила тока
- Напряжение дуги
- Скорость наплавки
- Расход электродов
Для каждого диаметра электродов производитель указывает рекомендуемые режимы. Например, для Э-42 диаметром 4 мм:
- Сила тока 150-190 А
- Напряжение 22-24 В
- Скорость наплавки до 25 м/ч
Соблюдение режимов позволяет получить качественную наплавку и избежать дефектов.
8. Практическое применение наплавочных электродов
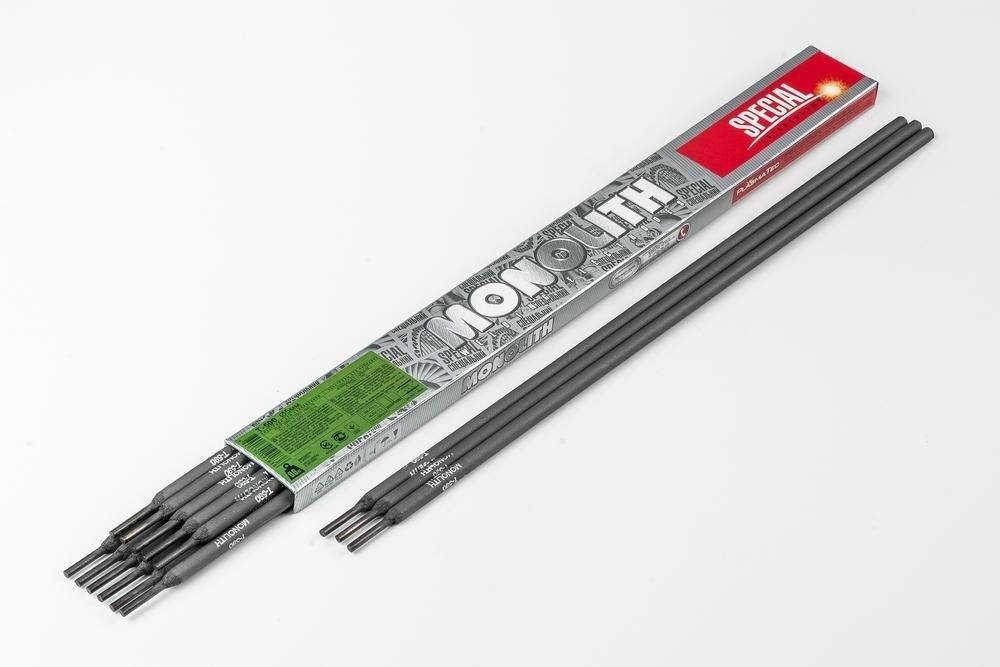
Наплавочные электроды широко применяются в различных отраслях промышленности и транспорта для восстановления и упрочнения деталей.
В горной промышленности наплавляют рабочие поверхности дробильно-размольного оборудования, детали экскаваторов, бурового инструмента. Применяют износостойкие электроды типа Т-590, Т-620.
В машиностроении наплавке подвергают детали прокатных станов, штампового инструмента, пресс-формы. Используют инструментальные электроды - Нп-30ХГСА, ЦНИИ-17.
В сельхозмашиностроении наплавляют лемехи плугов, ножи косилок, зубья борон. Применяют универсальные электроды - Т-590, УОНИ-13/55.
На железнодорожном транспорте наплавке подвергают бандажи колесных пар, сердечники стрелочных переводов, рельсы. Используют электроды типа Т-590, Т-650.
9. Требования к подготовке поверхности
Перед наплавкой поверхность детали должна быть очищена от грязи, ржавчины, окалины, масел. Это обеспечивает хорошую адгезию наплавленного металла.
Рекомендуемые способы подготовки поверхности:
- Обезжиривание органическими растворителями
- Травление в щелочных или кислотных растворах
- Пескоструйная или дробеструйная очистка
- Механическая обработка (шлифовка, фрезерование)
В некоторых случаях применяют предварительный подогрев детали для снятия внутренних напряжений.
10. Контроль качества наплавки
Контроль качества наплавки включает:
- Визуальный контроль
- Измерение твердости
- Металлографический анализ
- Испытания на износостойкость
При визуальном контроле проверяют отсутствие трещин, наплывов, подрезов. Измеряют твердость по заданным участкам наплавки. Металлографический анализ позволяет оценить структуру наплавленного слоя. Испытания на стендах определяют фактическую износостойкость.
11. Дефекты наплавки
Возможные дефекты наплавки:
- Пористость
- Непровары и несплавления
- Трещины
- Подрезы
- Наплывы и неравномерность валиков
Причины дефектов - нарушение режимов наплавки, неправильная техника выполнения, низкое качество подготовки поверхности.
Дефекты могут снизить эксплуатационные характеристики наплавленных деталей или привести к преждевременному разрушению. Поэтому важен тщательный контроль качества.