Предельные отклонения и допуски - одни из ключевых понятий в машиностроении. Они во многом определяют точность изготовления деталей, качество сборки машин, их надежность и долговечность. Давайте разберемся в этих фундаментальных вещах.
Основные термины и определения
В машиностроении используются следующие основные понятия, связанные с размерами:
- Номинальный размер - указан в чертеже, рассчитан исходя из условий прочности и жесткости
- Действительный размер - получен в результате измерения детали
- Предельный размер - наибольший или наименьший допустимый
Также различают верхнее предельное отклонение (разность между наибóльшим предельным и номинальным размерами) и нижнее предельное отклонение (разность между наимéньшим предельным и номинальным размерами).
Допуск - это разность между наибольшим и наименьшим предельными размерами, то есть интервал значений, в котором находится действительный размер детали.
Виды посадок и их характеристики
Различают следующие основные виды посадок:
- С зазором - обеспечивают подвижность соединений
- С натягом - для неподвижных соединений
- Переходные - могут давать и зазор, и натяг в зависимости от фактических размеров деталей
Конкретные типы посадок:
- Прессовая
- Легкопрессовая
- Глухая
- Тугая
- Плотная
- Скольжения
- Движения
- Ходовая
- Легкоходовая
- Широкоходовая
Посадку выбирают, исходя из условий работы соединения, наличия вибраций, ресурса и других факторов.
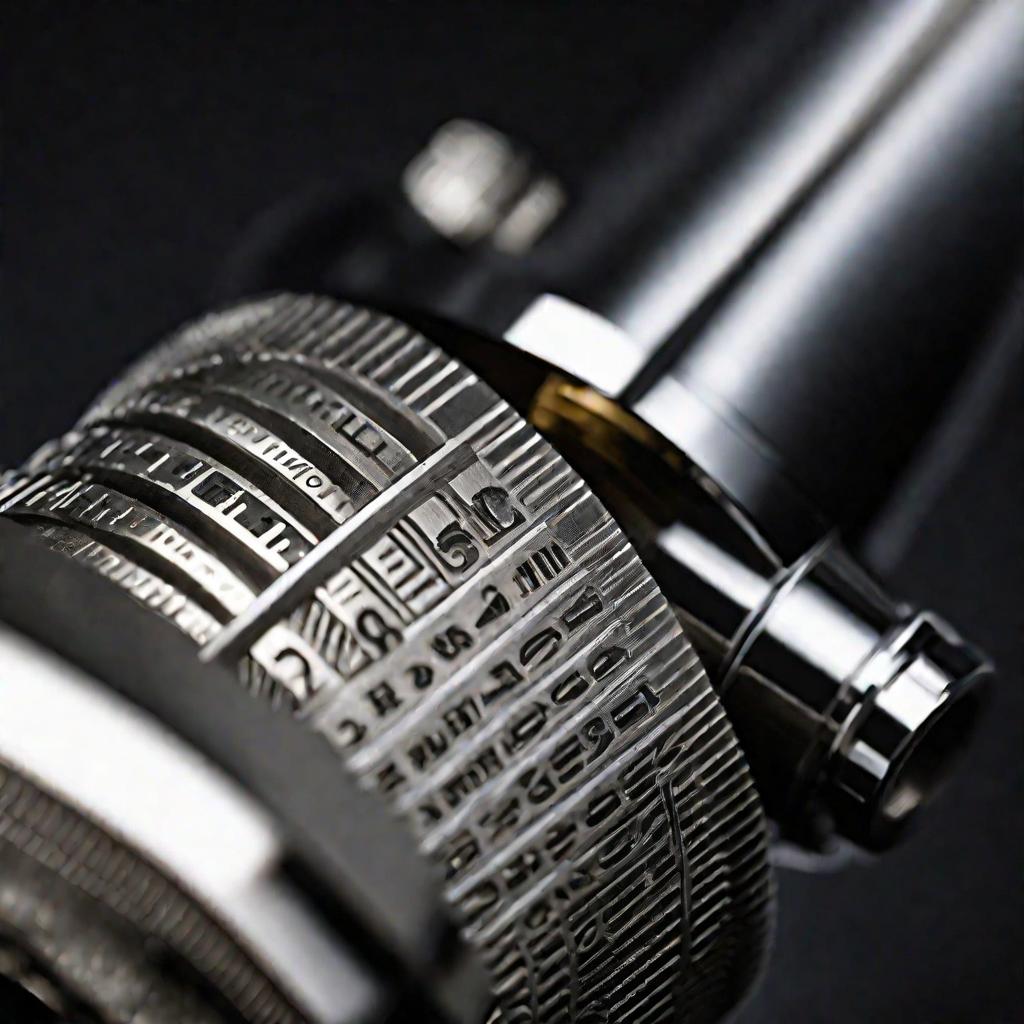
Квалитеты и их практическое применение
Квалитет характеризует точность изготовления детали с учетом ее размера. Чем выше квалитет - тем ниже точность. В системе ИСО определено 19 стандартных квалитетов.
Квалитет влияет на допустимый разброс параметров деталей. Он выбирается по аналогии с другими известными узлами или в соответствии с рекомендациями и ОСТами.
С повышением квалитета посадки также возрастают требования к чистоте поверхности сопрягаемых деталей.
Поля допусков - наглядное представление
Для наглядности допуски и посадки изображают в виде полей допусков на схемах. Поле допуска строится следующим образом:
- От номинального размера откладываются верхнее и нижнее отклонения
- Полученные точки соединяются линиями, ограничивающими поле
- Размер поля по горизонтали равен величине допуска
Различают основные и неосновные поля допусков. Для основных полей ближайшее к нулевой линии отклонение называется основным.
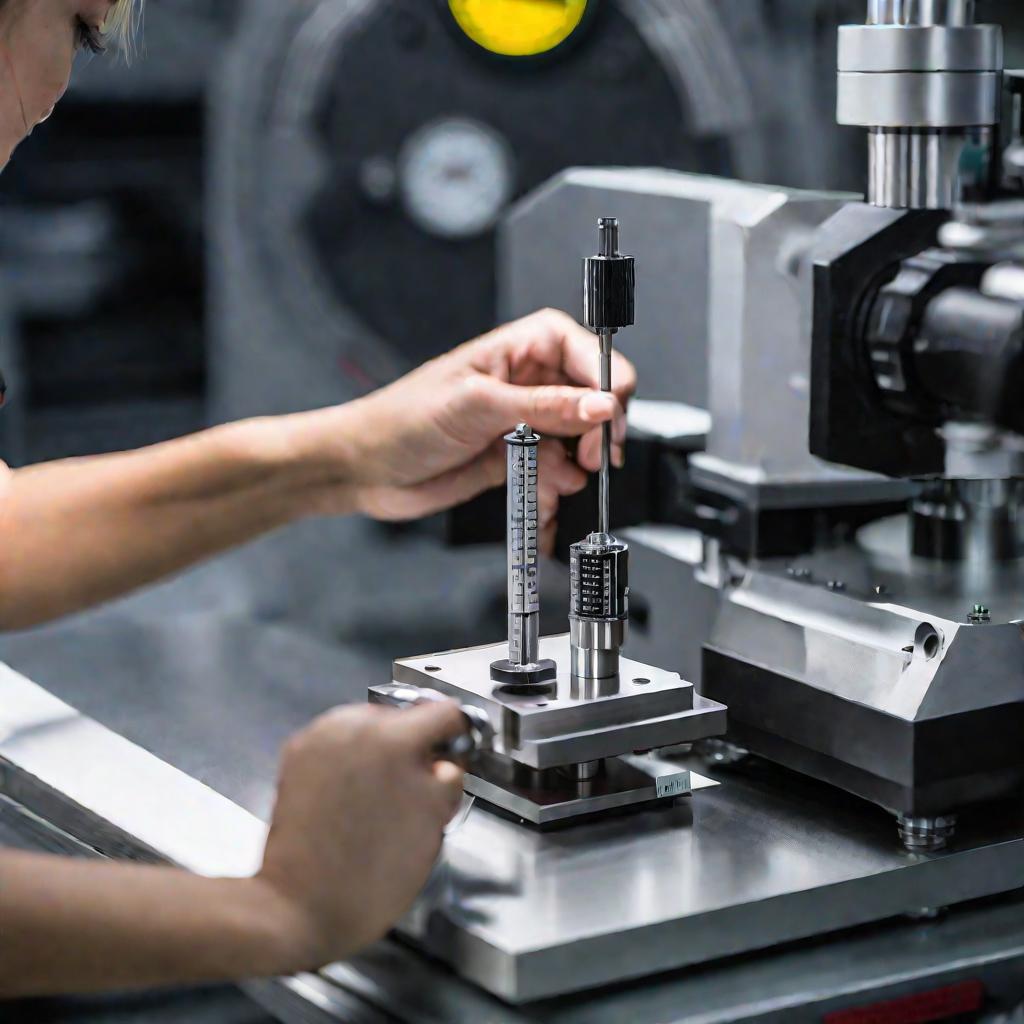
Стандартные обозначения
В системе ГОСТ для полей допусков используется специальная система обозначений с указанием основного отклонения и номера квалитета, например:
- Для вала - 65f6, 65e11
- Для отверстия - 65P6, 65H7
Предельное отклонение полей на практике
Наиболее распространенные типы полей допусков, используемые в машиностроении:
- Поле вала h14 (допуск +0,74 мм / - 0,14 мм)
- Поле отверстия H14 (допуск +0,62 мм / - 0 мм)
При их сочетании получается переходная посадка.
Допуск и требования к поверхности
С ужесточением допусков обычно повышаются требования к поверхности отверстий. Например, шероховатость для разных посадок может составлять:
Вид посадки | Шероховатость Ra, мкм |
С зазором | 6.3 |
Переходная | 3.2 |
С натягом | 1.6 |
Таблица допусков для отверстий
Для отверстий диаметром до 500 мм в зависимости от квалитета посадки действуют следующие предельные значения допусков согласно ГОСТ:
Квалитет | Допуск отверстия TD, мкм |
4 | 76 |
5 | 100 |
6 | 140 |
7 | 250 |
8 | 400 |
9 | 640 |
10 | 1000 |
11 | 1600 |
Из таблицы видно, что с повышением квалитета допуск увеличивается, а точность снижается.
Допуск и зазоры в посадках
Увеличение допуска для отверстий и валов приводит к росту возможных зазоров при их сопряжении. Например, при посадке:
- h9 (вал) / H9 (отверстие) минимальный зазор составит 0,086 мм
- h11 (вал) / H11 (отверстие) минимальный зазор - 0,43 мм
Значит, с ослаблением требований к точности зазоры будут больше, за счет бо́льших допусков размеров. Это важно учитывать при выборе посадки.
Обработка деталей с разными требованиями к точности
При механической обработке заготовок требования к деталям могут быть крайне разными. Например, для прессовых посадок токарная и фрезерная обработка недостаточна. Используются следующие методы:
- шлифование
- хонингование
- притирка
- доводка
Эти операции позволяют получить микронную точность размеров, низкую шероховатость поверхности (Ra = 0,05 мкм и выше) и высокий класс чистоты (8-12 класс по стандарту).
Пример посадки с точным зазором
Рассмотрим посадку с зазором H8/h8 в подшипниках качения. Здесь важно точно выдержать расчетный диаметральный зазор в пределах 0,023-0,087 мм. Это обеспечивает равномерное распределение нагрузки между телами качения и долгую безотказную работу узла.
Расчет допуска для спецтехники
В спецтехнике, работающей при низких температурах или с большими нагрузками, расчет допусков ведется с учетом дополнительных факторов. Например, предусматривается запас на термическое расширение деталей или их силовые деформации в процессе эксплуатации.
Автоматизация расчетов допусков
Современные системы автоматизированного проектирования (CAD) позволяют рассчитывать и оптимизировать допуски для сопряжений во всем механизме исходя из заданных условий работы, нагрузок и прочих параметров.
Влияние допусков на себестоимость
Чем жестче требования к допуску размеров деталей, тем выше себестоимость их изготовления. Это связано с применением более дорогостоящего высокоточного оборудования, инструмента, контрольно-измерительной техники.
Кроме того, на обработку деталей с малыми допусками тратится больше времени и трудозатрат. Например, при шлифовании достижение зеркальной чистоты поверхности может потребовать несколько проходов круга с постепенным снижением шероховатости.
Брак при изготовлении деталей
Если в процессе механической обработки допущены отклонения, выходящие за пределы заданного поля, такая деталь идет в брак. Частые браковки снижают рентабельность производства.
Поэтому важен постоянный контроль техпроцесса, а также квалификация рабочих и наладчиков оборудования. Небольшое ужесточение допусков может резко поднять процент брака.
Экономически оптимальные допуски
Исходя из вышесказанного, возникает задача определения экономически обоснованных допусков при проектировании изделия.
С одной стороны, это минимально необходимые допуски, при которых обеспечивается работоспособность и заданный ресурс конструкции.
С другой - такой уровень точности, при котором стоимость дополнительной высокоточной обработки еще оправдана эксплуатационными характеристиками.
Перспективы развития системы допусков
Совершенствование станочного оборудования, контрольно-измерительных машин и автоматизации производства открывает путь к дальнейшему повышению точности обработки деталей при сохранении экономической целесообразности.
Это позволит создавать более сложные, надежные и долговечные технические устройства и механизмы.
Погрешности измерительных средств
При контроле и приемке деталей возникает вопрос о достоверности полученных результатов измерений. Любые измерительные средства имеют собственные погрешности и неопределенности.
Поэтому значение допуска контрольного средства должно быть существенно меньше допуска на контролируемый параметр детали. Иначе результат будет недостоверным и невоспроизводимым.
Стандартизация и унификация
Единая система допусков и посадок (ЕСДП) позволяет унифицировать сопряжения в различных отраслях промышленности. Это облегчает проектирование, удешевляет и ускоряет производство комплектующих и запчастей.
Стандарты на механическую обработку - важнейшее достижение на пути к взаимозаменяемости деталей и совместимости оборудования.
История развития системы допусков
Первые системы предельных отклонений появились в 19 веке для нужд массового производства оружия и боеприпасов. Это позволило облегчить и удешевить изготовление оружия при сохранении боеспособности.
Современные системы допусков и посадок сформировались к началу 20 века. Основой ЕСДП стала система допусков СЭВ, принятая странами соцлагеря еще в 50-х годах.