Шпоночные соединения широко используются в машиностроении для передачи крутящего момента. От правильного изготовления шпонки и шпоночного паза зависит работоспособность всего механизма. Давайте разберемся в основных видах шпонок, способах изготовления шпоночных пазов и рекомендациях по их применению.
1. Виды шпонок, применяемых в машиностроении
Существует несколько основных видов шпонок, используемых в машиностроительной промышленности:
- Призматические шпонки имеют прямоугольное сечение, их противоположные грани параллельны. Такие шпонки отличаются простотой изготовления и установки.
- Сегментные шпонки похожи на призматические, но имеют дугообразный профиль. Их можно устанавливать группами для передачи больших нагрузок.
- Клиновые шпонки расклиниваются в пазу, обеспечивая надежное соединение вал-ступица. Применяются в высоконагруженных узлах.
Кроме того, используются цилиндрические, тангенциальные и некоторые другие типы шпонок для специальных целей.
2. Требования к материалам для изготовления шпонок
Для изготовления шпонок чаще всего используется конструкционная сталь со следующими характеристиками:
- Содержание углерода более 0,4% для обеспечения необходимой твердости и износостойкости
- Временное сопротивление разрыву порядка 590-650 МПа
- Твердость HRC 40-45 единиц по Роквеллу
Наиболее подходящие марки стали: Ст45, Ст50, Сталь 6 и им подобные. Применение более дорогих сталей и сплавов нецелесообразно из-за повышенной хрупкости.
3. Способы изготовления шпоночных пазов
Существует несколько технологических методов обработки шпоночных пазов:
- Фрезерование
- Долбление
- Протяжка
- Электроэрозионная обработка
- Лазерная резка
Рассмотрим подробнее первые три наиболее распространенных способа.
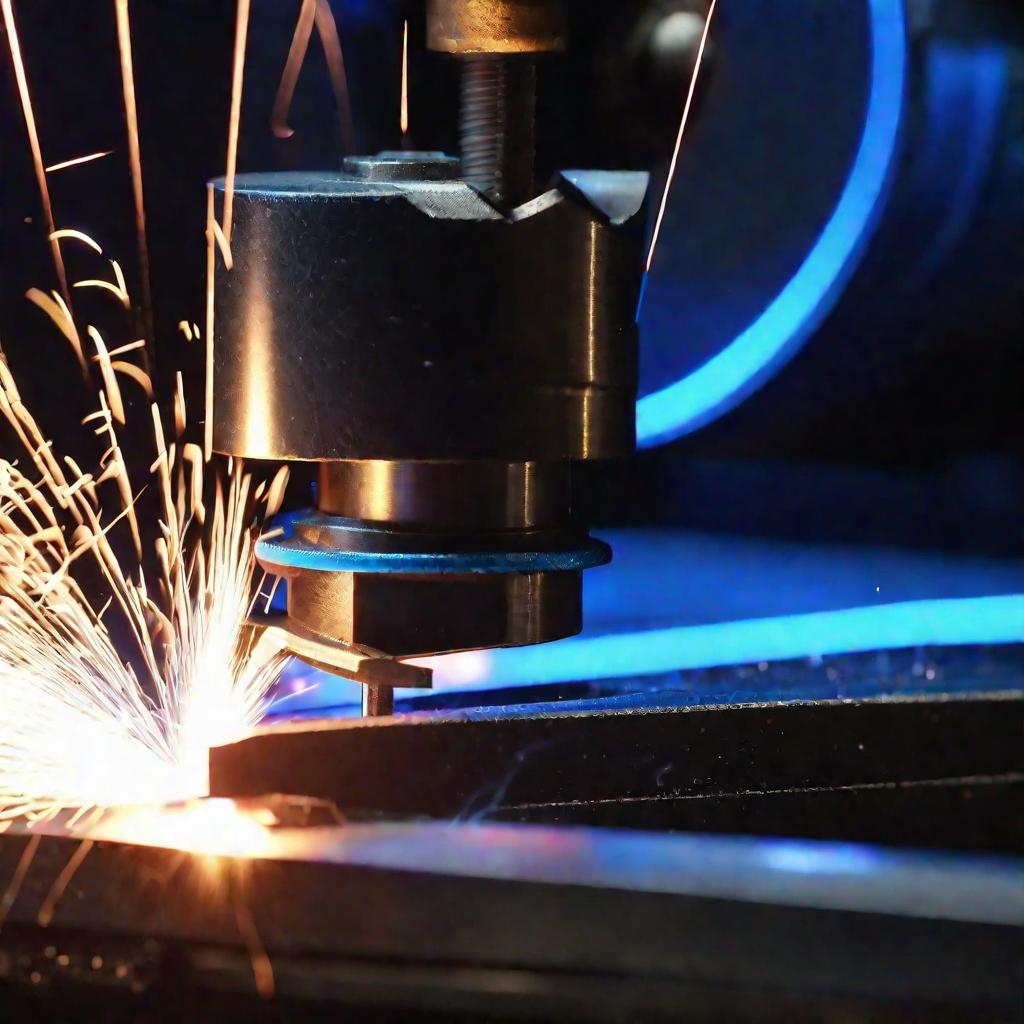
Фрезерование шпоночных пазов
Фрезерование осуществляется специальными дисковыми пазовыми фрезами. Этот метод обеспечивает высокую точность обработки и хорошее качество поверхности паза.
Однако требуются мощные станки и жесткие системы крепления заготовки. Процесс отличается высокой металлоемкостью.
Долбление шпоночных пазов
Долбление пазов осуществляется при помощи специальных долбяков в 2-3 прохода. Этот способ обеспечивает достаточную точность обработки при высокой производительности.
К недостаткам долбления относятся повышенная шероховатость поверхности и заусенцы по краям.
Обработанные пазы обычно подвергаются последующей чистовой обработке.
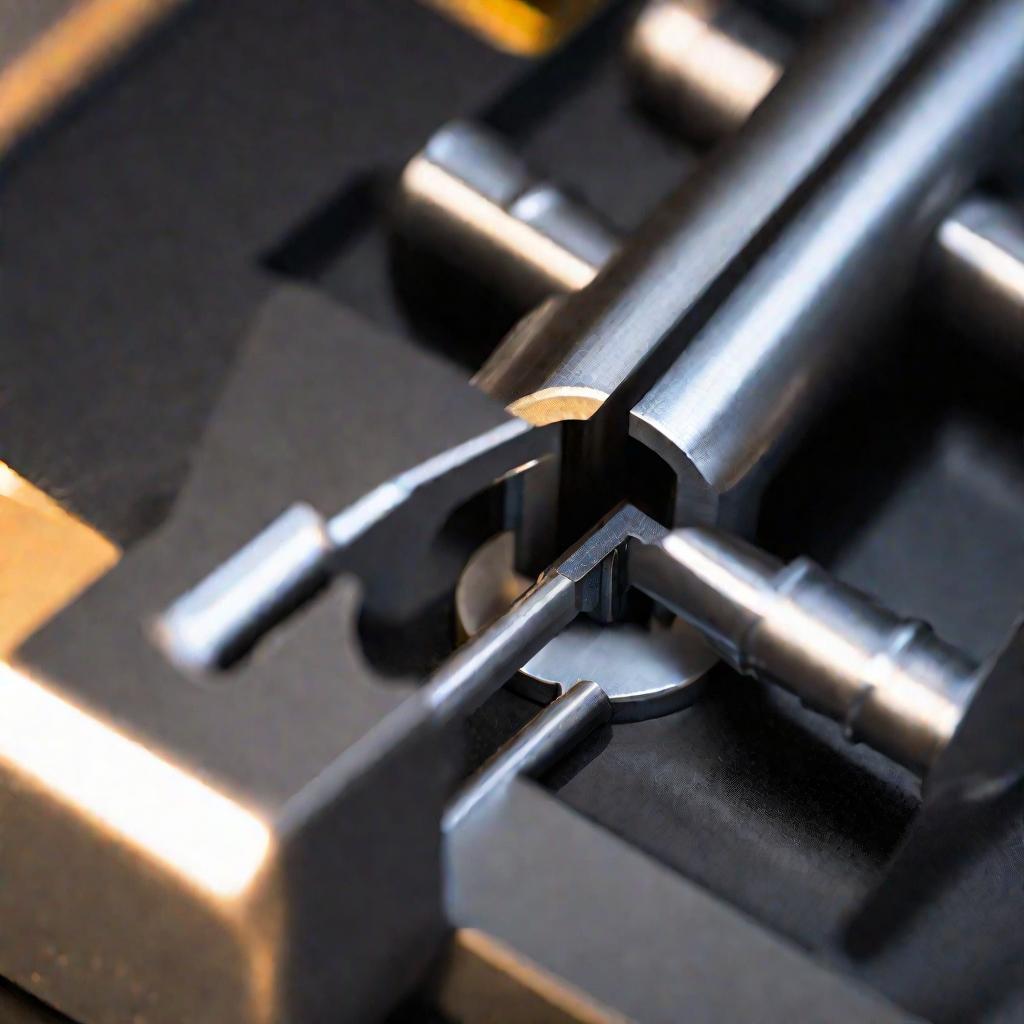
Протяжка шпоночных пазов
Протяжка осуществляется специальным инструментом - протяжкой. Этот способ прост в исполнении и не требует сложного оборудования.
Однако точность и чистота обработки шпоночных пазов протяжками значительно ниже, по сравнению с фрезерованием и долблением. Применяется в основном для неответственных деталей и черновой обработки.
4. Размеры и допуски шпоночных пазов и шпонок
Размеры шпоночных пазов и самих шпонок стандартизированы и регламентируются следующими ГОСТ:
- ГОСТ 23360-78 - призматические шпоночные пазы и шпонки
- ГОСТ 24071-97 - сегментные шпоночные пазы и шпонки
- ГОСТ 24068-80 - клиновые шпоночные пазы и шпонки
В этих стандартах приведены значения основных размеров, а также допустимые отклонения.
Анализ допусков и посадок
Допуски на размеры шпонок и пазов под них задают достаточно жесткие требования к точности изготовления.
Особое внимание следует уделить ширине шпонки (размер b). Допуск по этому размеру определяет надежность передачи крутящего момента.
5. Расчет шпоночных соединений на прочность
Расчет шпонок и шпоночных пазов ведется по сложной методике, включающей определение:
- Максимального крутящего момента
- Допускаемых напряжений для материалов шпонки и вала
- Коэффициентов запаса прочности
Рассмотрим упрощенный пример расчета.
Пример расчета призматической шпонки для редуктора
Рассмотрим редуктор, в котором установлен электродвигатель мощностью 5,5 кВт. Передаточное число редуктора i = 10.
Определим максимальный передаваемый крутящий момент:
где Р - мощность электродвигателя, кВт; n - частота вращения вала электродвигателя, об/мин.
Принимаем допускаемое напряжение для шпонки из стали Ст5 Ϭдоп = 60 МПа.
Определяем необходимые размеры шпонки из справочника в зависимости от диаметра вала d.
Выбор длины шпонки
Длина l призматической шпонки определяется по формуле:
где d - диаметр вала в месте установки шпонки, мм
В нашем случае получаем, что длина шпонки должна быть не менее 96 мм.
Расчет ширины шпонки
Ширина шпонки b
где T - крутящий момент на валу, Н·м; h - высота шпонки, мм; l - длина шпонки, мм; [σ] - допускаемое напряжение для материала шпонки, МПа.
Подставив значения, получаем требуемую ширину шпонки равной 14 мм.
По ГОСТ 23360-78 выбираем ближайший стандартный размер призматической шпонки с параметрами:
- Ширина b = 16 мм
- Высота h = 10 мм
- Длина l = 100 мм
Таким образом, расчетно-аналитическим методом определены параметры шпонки, обеспечивающие необходимую прочность шпоночного соединения в редукторе.