Обработка металлов резанием выполняется для того, чтобы заготовка приобрела нужную форму. С этой целью необходимо снять лишнее. Подобная манипуляция проводится посредством применения разных режущих инструментов на специальных станках. В машиностроении обработка металлов резанием очень важна. Ведь без этого процесса нельзя сделать ни обыкновенные машины, ни прочие приборы.
Применение технологии
Раскрой металла посредством резки практикуется при начальных обдирочных работах и при окончательных операциях, которые называют тонкой обработкой. Ведь подобные действия иногда нужно совершать, соблюдая высокую точность: вплоть до долей микрона. А это очень маленькая величина.
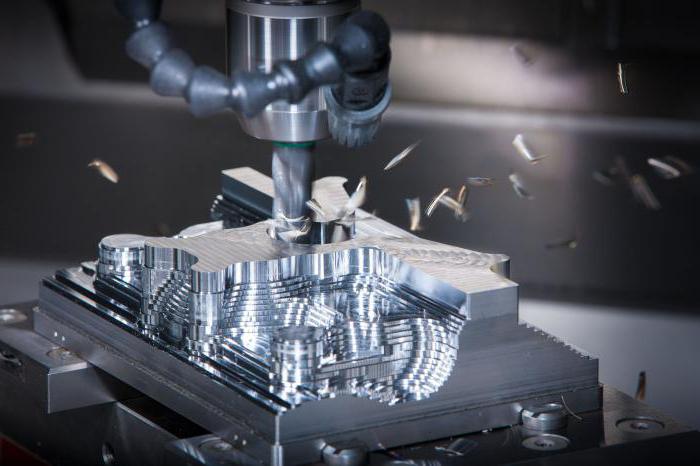
Теория резания
Такая наука изучает раскрой металла подобным способом. Она появилась ещё в конце XIX века. До сих пор ею занимаются как в России, так и за её пределами. Ключевой вопрос – это скорость съёма стружки посредством станка, чтобы стойкость резца была максимальной. Многим может показаться, что добиться высоких скоростей не так уж и трудно. Но это не так. Всё дело в том, что обработка металлов резанием развивает тепло. Оно нагревает и размягчает инструмент для работы, рискуя вывести его из строя. Очень важно выбрать правильное охлаждение для резца. Но оно не всегда решает проблему. К тому же может даже повредить металл. Поэтому скорость работы зависит отчасти от того, насколько правильный был выбран станок. Инструмент для обработки металла резанием должен приобретаться с учётом свойств материала и его свойств.
Особенности применения станков
Металлорежущие станки подразделяются на типы. Они отличаются по используемому инструменту. Также технология обработки металлов резанием с их помощью разная. Чаще всего используется резец. С его помощью можно выполнять операции любой сложности. Все остальные инструменты являются или его модификацией, или сочетанием нескольких типов. Существует две наиболее распространённые схемы работы:
- точение, когда заготовка вращается, а резец медленно идёт по её оси;
- строгание – они идут оба поступательными движениями.
Станки для них необходимы абсолютно разные.
Особенности резки металлов
Как было сказано ранее, рассматриваемый процесс может происходить нетипично. И существуют разные способы обработки металлов резанием, под которые предусмотрено использование того или иного оборудования.

Применение токарных станков
Оборудование для резки бывает разным. Один из ключевых типов станков – это токарный. Его применение практиковалось ещё в древние времена. Тогда его приводили в действие благодаря верёвочным приспособлениям наподобие лука для стрельбы. В такой сфере, как резание металлов, токарная обработка в нынешнее время применяется с целью изготовления машинных деталей. Причём это делается настолько точно и быстро, что механическим путём таких целей достичь не удастся.
Основанием станка этого типа является станина. Заготовку нужно зажать между центрами задней и передней бабки или же в патроне. В суппорте укрепите резец. Установите посредством специальной коробки, напоминающей автомобильную, требуемую скорость вращения для резки. На инструменте присутствует ходовой валик, который приходит в движение от неё и смещает суппорт вместе с резцом. Если кроме него стоит ходовой винт, то тогда посредством такого станка можно выполнять нарезку. Когда же присутствует поворотная головка вместо задней бабки, инструмент называется токарно-револьверным. Такой станок для резки может выполнять разные виды работы. Для обработки изделий с большим диаметром используют такие инструменты, как лоботокарный или карусельно-токарный аппарат. Существуют и прочие его виды.
Повышение стойкости токарного станка
Специалисты постоянно работают над тем, чтобы отыскать подходящие материалы, способные повысить стойкость рабочего инструмента для резки металла. Раньше станки изготавливали на основе простых углеродистых сталей, обладающих несложным составом с точки зрения химии. После этого стали применяться материалы с повышенным содержанием вольфрама. С их помощью можно было резать металлы намного быстрее. Поэтому их стали называть быстрорежущими. Однако и они со временем перестали удовлетворять специалистов в области машиностроения.
Тогда на смену им при создании станков пришли твёрдые сплавы особого класса, которые способны сохранять прочность даже при температуре до 100 градусов. За последние годы процесс, в основе которого лежит обработка металлов резанием, стал ещё проще. Этого удалось достичь за счёт использования материалов с максимальной устойчивостью к высоким температурам. В зависимости от изначальной твёрдости заготовки, например резца, а также вида работы, оно может быть обработано с нужной скоростью, которая регулируется посредством специальной коробки.
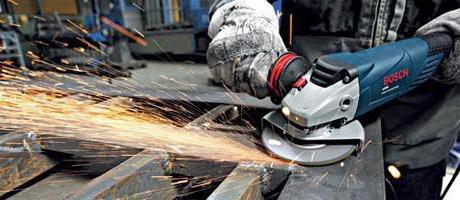
Фрезерование как вид обработки металла
Такой метод работы достаточно широко распространён и является достаточно высокопроизводительным. Он осуществляется с помощью специального фрезерного аппарата. Станки с ЧПУ (числовым программным управлением) используются всё чаще. В зависимости от места размещения суппорта они подразделяются на несколько видов:
- вертикальные;
- горизонтальные;
- портальные;
- продольные;
- зубофрезерные;
- многошпиндельные;
- одношпиндельные и другие.
Специалисты по изготовлению оборудования этого вида постоянно совершенствуют его, чтобы производительность обработки металла была более высокой. Материал станков постоянно меняется, видоизменяется и его конструкция. Как и резец при строгании, фреза выполняет аналогичные действия. Но при этом она сочетает несколько его типов. И будет работать более продуктивно. За счёт этого фрезерование значительно превосходит строгание и постепенно вытесняет его на производствах.
Особенности шлифования
Станки для этого типа обработки используются для шлифовки внутри и снаружи поверхностей круглой формы, разных плоскостей, бесцентровой обработки, резьбы, зубчатых колёс и многого другого. Такой инструмент для металлов относится к категории наиболее производительных. Помимо специального станка, существует ещё одно приспособление. Это шлифовальный круг, который включает в себя большое количество маленьких режущих элементов. Они, в свою очередь, скреплены специальным связующим приспособлением. И каждая частица сама по себе является резцом. Как видите, мы рассмотрели оборудование для металлической обработки. Ниже ознакомимся с более современными методиками, позволяющими осуществлять его раскрой.
Особенности технологии плазменной резки
Есть несколько методик, используемых для низкоуглеродистых металлов. Но плазменная резка считается одной из продуктивных. Поэтому на её особенностях и преимуществах стоит остановиться более подробно. Технология процесса стремительно и постоянно развивается. Плазменная резка металлов широко применяется в разных производственных сферах: начиная от строительства домов и заканчивая машиностроением. Наряду с кислородно-газовым методом, она считается достаточно перспективной.
Ключевые преимущества
Способ плазменной резки металлов имеет большое количество преимуществ. Одно из них – это скорость работы. Чаще всего заготовки для раскроя имеют толщину до 25 мм. В этом случае скорость их обработки примерно в два раза и даже больше превышает аналогичную при использовании резки кислородно-газового типа. И стоит добавить, что при заметном уменьшении толщины листа металла, она может превышать её и в 12 раз. Такое преимущества способно существенно повысить производительность работы и сэкономить время.
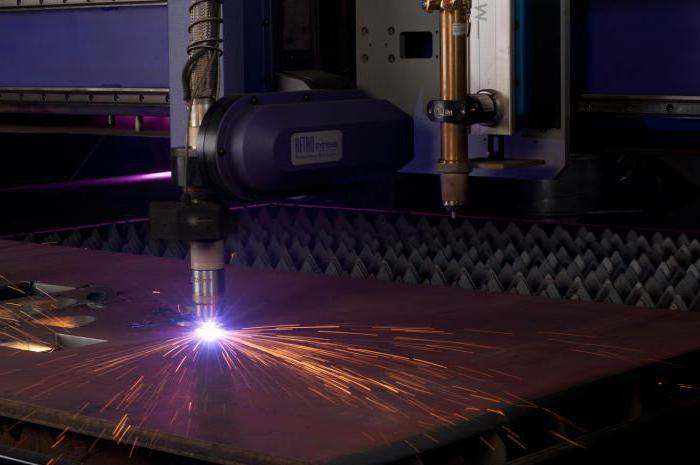
Другим несомненным преимуществом плазменного метода можно назвать минимальное количество окалины при работе. Её можно с лёгкостью удалить. Системы для резки также легко управляются и помогают обеспечить нужную высоту инструмента и хорошую скорость.
Экономия времени и средств
Плазменная резка также подразумевает одновременную работу с несколькими листами, что значительно экономит время. При этом методе можно обрабатывать разные виды материалов:
- алюминий;
- нержавейку;
- медь и многое другое.
Нельзя не отметить и безопасность применения плазменных систем. Они не используют для работы горючие газы, открытый огонь, не выделяется много тепла. Всё это значительно сокращает возможные риски для пользователей при работе с горячими металлами. Зона воздействия тепла составляет всего лишь 2 миллиметра.
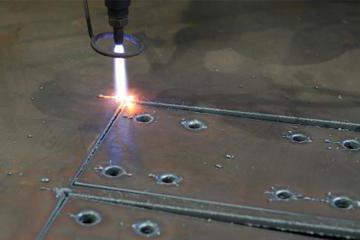
Особенности лазерного метода
На сегодняшний день в области обработки металлических изделий внедрено немало технологий. Они позволяют значительно облегчить работу дизайнеров, строителей и прочих специалистов, чья работа так или иначе связана с этим процессом. Резка лазером в настоящее время считается наиболее продвинутой. Она позволяет получить огромные возможности при изготовлении металлических изделий в плане дизайна и всевозможных конфигураций.
Такая перспективная методика является достаточно молодой, но уже широко распространяется. Резка лазером металла осуществляется посредством сфокусированных технически мощных специальных установок. Они отличаются высокой лучевой концентрацией. И способны раскроить не только алюминий или медь, но также дерево и прочие материалы.
Описание метода
При таком способе резки на поверхности металла появляются окислы. Они увеличивают процесс поглощения энергии и способны поддержать температуру до точки плавления. В контактном месте лазерный луч создаёт максимальные температурные показатели, вследствие чего материал начинает плавиться. А вот за пределами указанной зоны он лишь нагревается. Вместе с этим идёт подача активного газа, чаще всего это кислород. Он выдувает продукты горения и позволяет значительно увеличить скорость резки. Кислород нагревает несколько слоёв посредством удаления жидкого металла и окислов.
Всё это происходит в то время, пока материал не прорезается на всю свою глубину. Ведь струя газа рядом с линиями разделения способна активно охлаждать его. Небольшая зона термического воздействия может обеспечить создание на небольших расстояниях друг от друга (порядка 0, 2 миллиметра) кромок, расположенных параллельно. Очень часто с целью достижения той или иной точности при операции раскроя появляется необходимость внедрения автоматизированного управления посредством компьютера. В таких случаях можно запрограммировать создание того или иного изделия в готовом виде.
Для лазерной резки листовых металлов чаще всего применяется аппаратура на основе твердотельных и газовых инструментов. Срез материала при этом получается идеально ровным. Никакая механическая обработка металлов резанием не может обеспечить подобную точность с учётом оперативного выполнения и с минимальным количеством отходов. В основном для обработки листового металла используют аппараты на основе газовых и твердотельных лазеров. Лазерный срез металла будет идеально ровным. Он получится без деформаций, которые присутствуют при механическом разрезе. К тому же технология лазерной резки позволяет добиться существенной точности работы, минимальных отходов и быстрого выполнения.
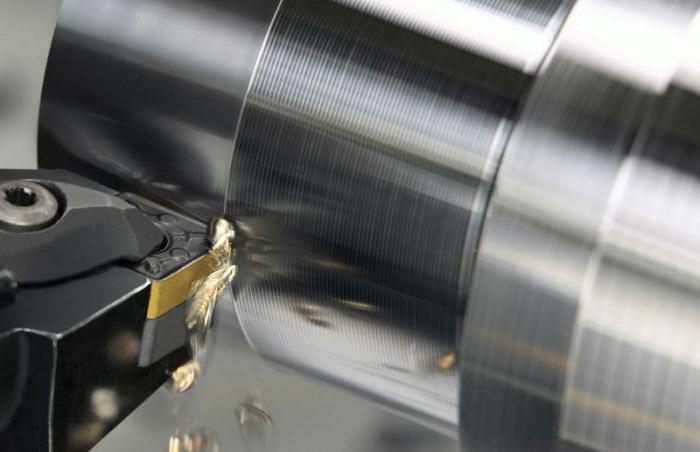
Преимущества метода
На рынке раскроя металлических изделий лазерная резка является одной из наиболее востребованных. Она в значительной мере сделала работу с твердосплавными материалами более простой. Ведь они достаточно сложные в плане обработки и часто могли ухудшиться после таких манипуляций. Для лазерной резки лучше всего подойдут:
- сталь;
- цветные металлы;
- алюминиевые сплавы.
Толстые листы тоже гораздо лучше обрабатываются. Будет проще работать со сложными формами металлических деталей и делать отверстия в очень твёрдых материалах с малым диаметром. Здесь в плане геометрии можно дать волю своей фантазии. Система может быть автоматизирована. Достаточно для этого создать специальный файл с заданной программой на компьютере. Механических воздействий на металл не будет – это тоже немаловажно. Также при лазерной обработке замечены следующие преимущества:
- Возможность создания сложного контура реза.
- Можно обрабатывать практически любой листовой металл независимо от его теплофизических характеристик.
- Высокая точность работ.
- Резка возможна даже на легко деформируемых и не слишком жёстких материалах.
- Высокая производительность за счёт применения большой мощности лазера.
- Если поверхность должна быть гладкой, то лучше использовать сфокусированный луч с регулируемой мощностью.
Газовый способ
Рассмотрим достаточно распространённый метод воздействия на металл, который активно применяется уже многие годы. Это газовая резка. Она достаточно популярна и экономически выгодна. По-другому её называют ещё кислородной, поскольку в этом случае процесс воздействия на металл имеет термический характер. Идёт струя кислорода после окончания работы и удаляет остатки жидкого оксида. Для начала верхняя кромка детали подогревается. В зависимости от химического состава материала (например стали) температура его возгорания может колебаться в пределах от 1000 и до 1200 градусов.
Газовая резка может быть применена для обработки среднелегированной, низколегированной или углеродистой стали. Толщина металлического листа или другого изделия должна составлять максимум 300 миллиметров. Газокислородная методика обработки металла имеет свои преимущества:
- Низкие затраты на обработку.
- Отсутствует необходимость работать с кромкой после завершения процедуры.
- Наличие прямой и диагональной резки изделий под разными углами.
- Можно использовать толстые металлические листы.
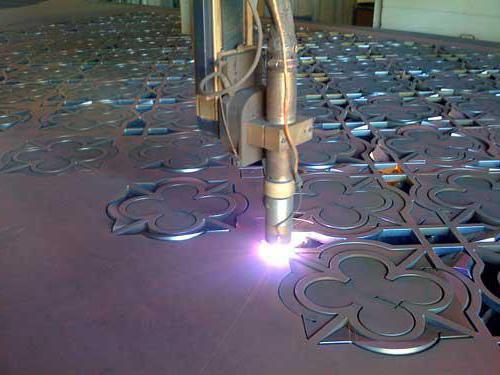
Существует ли стандарт работы?
Многие интересуются, имеет ли обработка металлов резанием ГОСТ или другие стандарты касательно выполнения обработки конструкций. Так, согласно существующим правилам и критериям, подобный процесс имеет свои задачи. Прежде всего деталям должна быть придана та или иная конфигурация и размеры. Этого требует используемая технологическая документация. Например, утверждённый проект строительства объекта. Также обрабатываемая поверхность должна быть всегда чистой согласно принятым стандартам. В ГОСТах перечислены механические способы обработки металлов резанием, включая точение, сверление, фрезерование, а также долбление, протягивание. Также указана и финальная обработка изделий. Каждому виду механической обработки металлов соответствует не только определённое оборудование, но и порядковый номер.
Как мы увидели, существует немало способов механической и автоматизированной обработки изделий с целью их раскроя. Всё это широко используется при строительстве, машиностроении, ремонте и других сферах. Методики постоянно совершенствуются и дополняются новыми, создаётся современное оборудование, которое каждый раз делает процесс всё более простым.