Методы обработки материалов регулярно совершенствуются, каждый год предлагая улучшение того или иного показателя или же принципиальное изменение техники. В этом смысле лазерные способы резки можно отнести к наиболее перспективным и прогрессивным. Данная группа технологий раскроя отличается множеством достоинств, но также имеет некоторые ограничения. Так, если в работе с твердотельными материалами с такими способами могут конкурировать средства механического воздействия, то лазерная резка пластика, картона, плексиглаза и фанерных листов практически не имеет аналогов по критериям качества получаемых изделий.
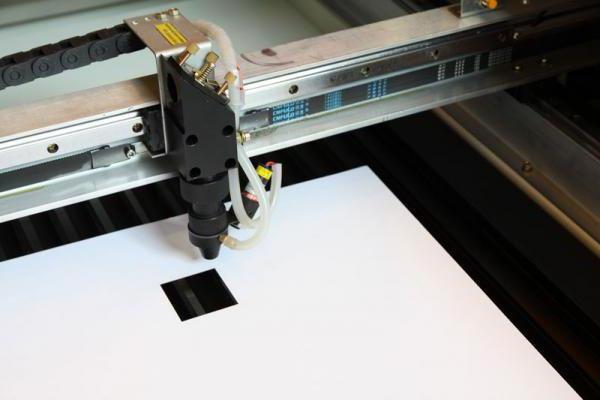
Преимущества лазерной обработки
С помощью лазерной резки сложно справиться с камнем или металлом, сохраняя при этом высокий уровень точности. Однако легкодеформируемые материалы позволяют максимально раскрыть преимущества данного метода. Например, лазерная резка акрила может производиться с минимальным допуском реза и повышенной детальностью в его направлении. Сама же точность может находиться на показателе 25 мкм, чего невозможно достичь при помощи традиционных средств механического раскроя. Другое дело, что многое зависит и от самого материала. Но даже твердые породы дерева с картоном или оргстекло оптимально поддаются быстрой гравировке лазером.
Помимо преимуществ, которые выражаются непосредственно в свойствах получаемого изделия, стоит подчеркнуть и косвенные выгоды. Высокая скорость, на которой реализуется лазерная резка пластика, позволяет эффективно работать с большими партиями заказов. И это не говоря о минимизации отходов от базового материала, которая также обуславливает экономические преимущества метода.
Суть технологии
Вторжение в структуру материала с целью осуществления раскроя происходит с помощью подачи лазерного луча через специальную оптику. Рабочий процесс также сопровождается поддержкой особых смесей – воздушных и газовых. Например, потоки сжатого воздуха выполняют две задачи – очищают те же оптические линзы и в некоторых случаях избавляют рабочую площадку от перегрева. Газы в виде азота и кислорода участвуют в активизации процесса резки и в то же время не допускают воспламенения.
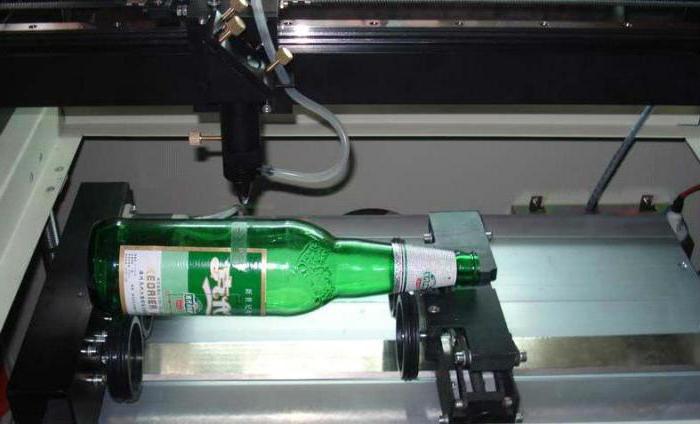
В некотором роде комбинированная лазерная резка пластика и позволяет достичь вышеописанных преимуществ за счет использования минимума ресурсов. По сравнению с абразивной или плазменной обработкой лазеры не просто задействуют меньше расходников, но и в техническом плане не такие требовательные. Правда, это не касается технологического обеспечения, поскольку уровень аппаратно-программной начинки в применяемом оборудовании зачастую на порядок выше.
Техническое обеспечение
Для выполнения лазерной резки применяются специальные станки. В состав типового оборудования данного рода входит рабочая площадка, движущиеся механизмы управления заготовкой, панель оператора, коммуникационные подводки и системы безопасности. По мощности оборудование для лазерной резки может требовать от 3 до 10 кВт в среднем, что является неплохим показателем на фоне других станков, работающих в форматах серийного производства.
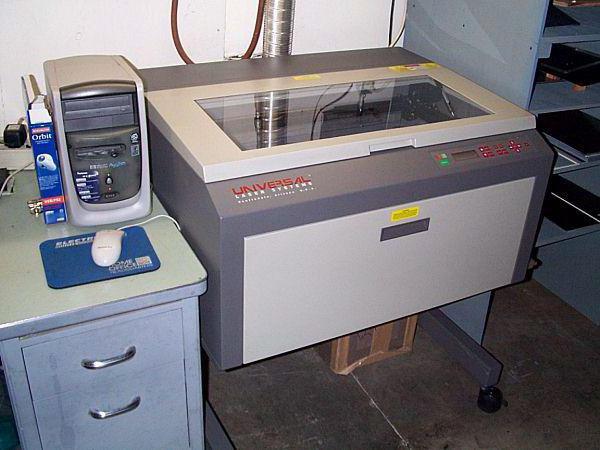
Раскрой осуществляется при помощи активной оптики с линзами, функция которой дополняется соплом, подающим вспомогательные смеси. Важной особенностью лазерного оборудования такого типа является возможность высокоточной коррекции позиционного органа резки, отклонения в которой могут достигать не более 3 мкм в передовых установках.
Дополнительный опционал станков
Модели станков с числовым программируемым управлением (ЧПУ) демонстрируют наибольшие успехи использования лазерной резки. Конструкторам удается органично связывать функцию оптических элементов с программными системами. Современные пакеты опционального оснащения станков позволяют выполнять обработку в автоматическом режиме, вести видеонаблюдение за рабочим участком, компенсировать возможные искажения без ручного вмешательства и эффективно разрабатывать шаблонные форматы раскроя с применением специальных программ.
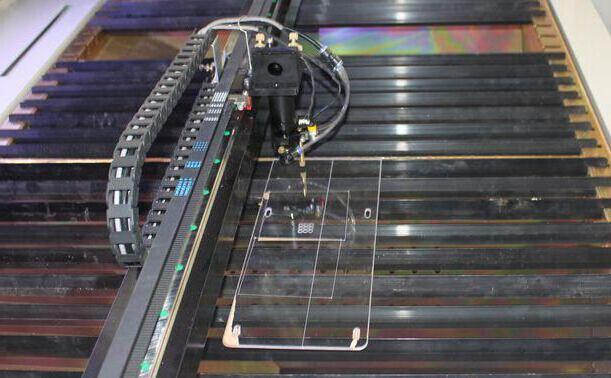
При этом существует лазерная резка, ЧПУ которой позволяет вносить корректировки в рабочий процесс на основе воздействия внешних факторов. То есть станок оснащается набором датчиков, которые отслеживают характеристики воздушной среды, отправляя оптической головке или соплу соответствующие сигналы с командами коррекции. Это наиболее передовые и сложные разработки, которые используются преимущественно крупными компаниями.
Где используется лазерная резка пластика?
Спектр областей применения технологии довольно широк. С одной стороны, высокоточный раскрой пластиков, древесины, оргстекла и других податливых материалов успешно используется в строительстве при создании отделочных покрытий с мелкими узорами и рисунками.
Но основная сфера все же относится к производству рекламной и сувенирной продукции. Мелкая по формату лазерная резка и гравировка, в частности, позволяет получать аккуратные и небольшие по размеру брелоки, шильдики и различные аксессуары почти с ювелирными украшениями на поверхностях.
Используют технологию и в текстильной промышленности. В этой нише фабрики осваивают данный метод с целью выполнения сложных штамповок, кружев и контуров на тканях, коже и других материалах.
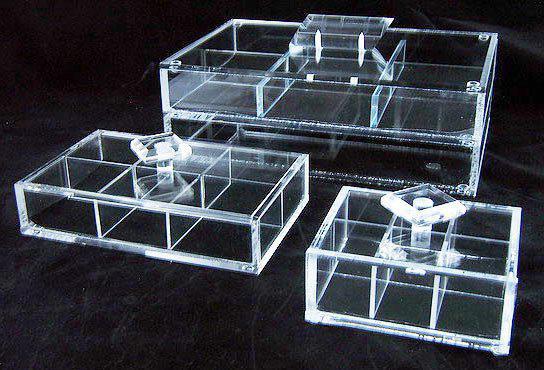
Заключение
Редко бывает, что новые технологии во всех отношениях оказываются лучше по сравнению с традиционными способами решения тех или иных задач. Недостатком данного метода является отсутствие возможности с той же эффективностью справляться с твердым металлом. Но для тех, кому требуется именно лазерная резка акрила, пластиковых и деревянных материалов, минусы практически неощутимы. Конечно, аппараты с программируемым управлением могут доставить определенные хлопоты в процессе эксплуатации, но активное включение автоматических систем упрощает и эргономические нюансы производственного процесса. Вместе с этим совершенствуется и конструкционная основа, позволяющая уже сегодня избавляться от специальных механизмов фиксации заготовок.