Подвижное шлицевое соединение является важным элементом во многих механизмах. Оно позволяет передавать крутящий момент между валами, обеспечивая при этом их подвижность относительно друг друга. Давайте разберемся, как устроено это соединение и что нужно для его надежной работы.
Шлицевое соединение состоит из двух частей - вала с продольными пазами (шлицами) и втулки с соответствующими шлицами. Шлицы вала и втулки имеют одинаковую форму и размеры, благодаря чему плотно соприкасаются друг с другом. Это позволяет эффективно передавать крутящий момент при вращении вала.
Типы шлицевых соединений
Существует несколько разновидностей шлицевых соединений, отличающихся формой шлицев:
- Прямоугольные
- Треугольные
- Эвольвентные
- Круглые
Наиболее распространенными являются прямоугольные и эвольвентные шлицевые соединения. Они отличаются высокой несущей способностью и надежностью.
Материалы для изготовления
Для изготовления шлицевых соединений применяются различные материалы:
- Сталь
- Чугун
- Латунь
- Бронза
- Пластмасса
Наиболее часто используют сталь, чугун и цветные металлы. Выбор материала зависит от требуемых характеристик - прочности, износостойкости, коррозионной стойкости.
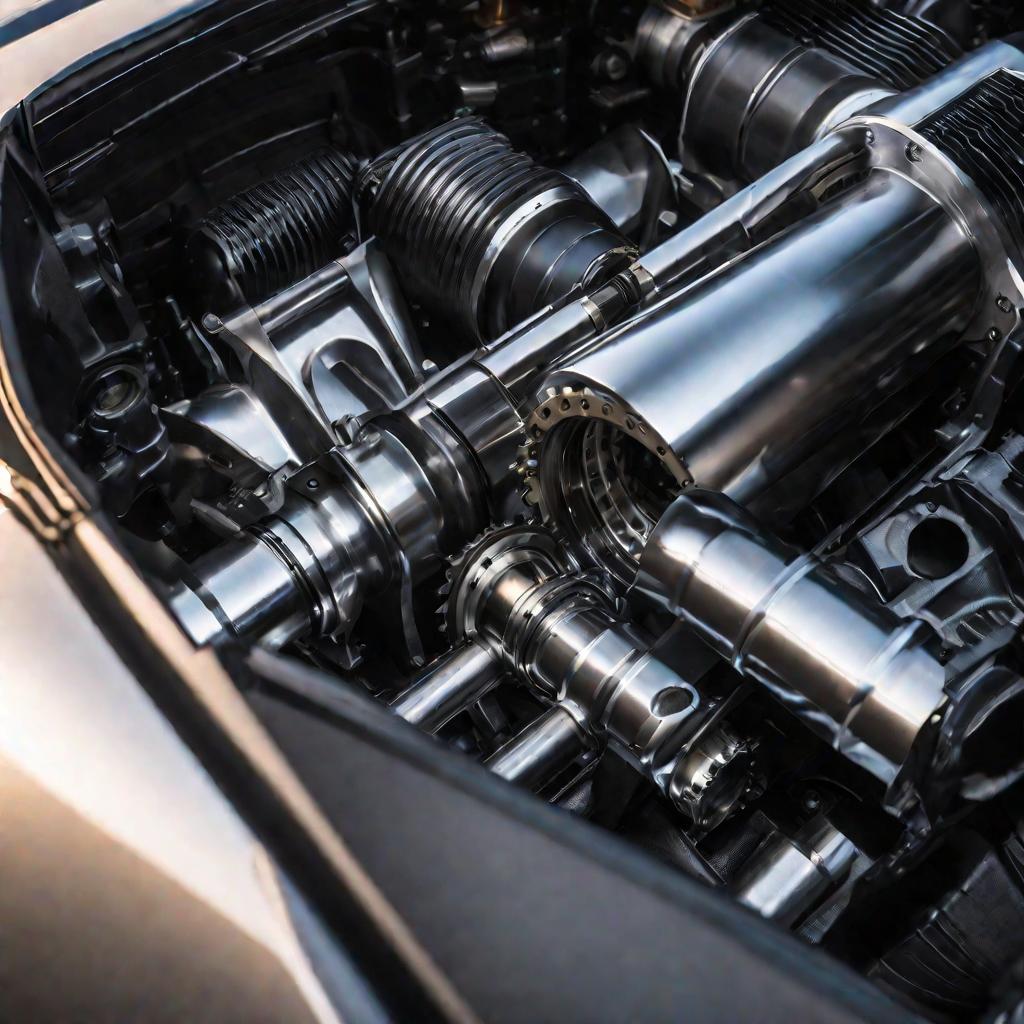
Точность изготовления
Очень важным моментом является соблюдение высокой точности при изготовлении шлицевого соединения. Это необходимо для плотного контакта шлицев вала и втулки.
Допуски на размеры шлицев обычно устанавливаются в пределах нескольких сотых долей миллиметра. Шероховатость поверхности также должна быть минимальной - 1,6-0,4 мкм.
Такая высокая точность обеспечивается применением современного металлообрабатывающего оборудования - токарных, фрезерных, шлифовальных станков с ЧПУ.
Сборка и смазка
Перед сборкой шлицевого соединения необходимо тщательно очистить и промыть шлицы от стружки и продуктов обработки. Затем поверхности шлицев смазывают минеральным или синтетическим маслом.
Подвижное шлицевое соединение рекомендуется собирать с небольшим натягом, который обеспечивает плотное прилегание шлицев вала и втулки. Натяг подбирается в зависимости от материалов и типоразмера соединения.
В процессе эксплуатации необходимо проводить периодическую смазку шлицевого соединения, используя рекомендованные производителем смазочные материалы.
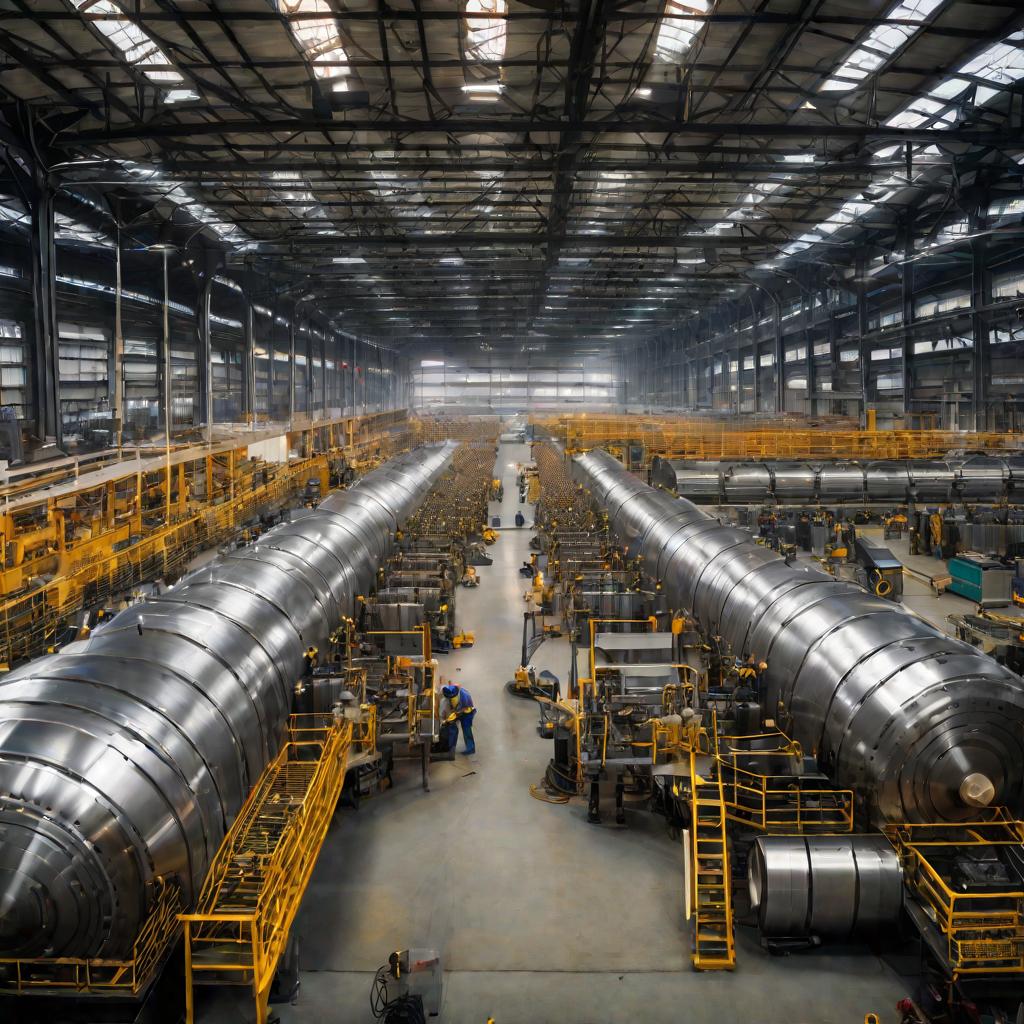
Конструктивные особенности
Для обеспечения надежности и долговечности шлицевого соединения применяются следующие конструктивные решения:
- Фаски на входных кромках шлицев вала и втулки, уменьшающие износ при взаимодействии
- Упрочняющая закалка рабочих поверхностей шлицев
- Грибовидная форма торцов вала, предотвращающая осевое смещение
- Стопорные кольца, фиксирующие положение втулки на валу
Благодаря таким конструктивным особенностям достигается высокая стойкость шлицевого соединения к износу и сохранение заданных эксплуатационных характеристик.
Применение шлицевых соединений
Шлицевые соединения широко используются в различных отраслях промышленности:
- Машиностроение - соединения в коробках передач, редукторах
- Автомобилестроение - соединение карданных валов, коленчатых валов
- Судостроение и авиастроение - в трансмиссиях
- Робототехника - в приводах манипуляторов
Правильно спроектированное и изготовленное подвижное шлицевое соединение обеспечивает надежную работу различных механизмов на протяжении длительного времени. Соблюдение рекомендаций по конструкции, материалам, изготовлению и эксплуатации позволяет максимально использовать потенциал этого распространенного типа соединения вала с втулкой.
Требования к точности обработки шлицев
Для обеспечения надежной работы подвижного шлицевого соединения крайне важно соблюдение требований к точности изготовления шлицев вала и втулки.
Отклонения от номинальных размеров по высоте и ширине шлицев не должны превышать нескольких сотых долей миллиметра. Наиболее жесткие допуски устанавливаются для соединений, работающих на высоких скоростях и под большими нагрузками.
Погрешности формы профиля шлицев также влияют на качество соединения. Недопустимы отклонения от прямолинейности образующих, несоосность шлицевых поверхностей.
Высокая чистота поверхности шлицев достигается тщательной финишной обработкой - шлифованием или притиркой. Шероховатость поверхности должна составлять Ra 0,4...0,8 мкм.
Технологии повышения износостойкости
Для увеличения срока службы шлицевых соединений, особенно работающих в тяжелых условиях, применяются специальные технологии повышения износостойкости шлицевых поверхностей.
Наиболее распространены следующие методы упрочнения шлицев:
- Закалка ТВЧ - высокочастотная закалка рабочих поверхностей шлицев
- Азотирование - насыщение поверхностного слоя шлицев азотом
- Наплавка износостойкими сплавами
- Ионная имплантация - внедрение ионов в поверхность
Такие методы позволяют значительно повысить твердость и износостойкость шлицев. Например, закалка ТВЧ увеличивает ресурс шлицевого соединения кардана в 3-5 раз.
Выбор конкретного метода упрочнения зависит от условий работы шлицевого соединения, требований к ресурсу и стоимости.
Использование передовых технологий износостойких покрытий обеспечивает высокую надежность и долговечность прямобочных шлицевых соединений в различных отраслях промышленности.
Особенности смазки шлицевых соединений
Правильный подбор смазочных материалов имеет большое значение для обеспечения надежной работы шлицевых соединений.
Для смазки шлицевых соединений, работающих в условиях высоких скоростей и нагрузок, применяют специальные высокотемпературные смазки. Они обеспечивают стабильную смазывающую пленку при температурах 150-200°C.
Подшипниковые и литиевые смазки используются для смазки шлицевых соединений, работающих при умеренных нагрузках и температурах. Они отличаются хорошей адгезией к металлам.
Для соединений, подверженных фреттинг-коррозии, применяют смазки с противозадирными присадками, снижающими износ.
Проектирование шлицевых соединений
При проектировании шлицевых соединений учитываются следующие основные факторы:
- Нагрузки, действующие на соединение
- Частота вращения вала
- Требуемый ресурс работы
- Условия эксплуатации
На основании этих исходных данных выбираются тип шлицевого соединения, материалы, термообработка, а также рассчитываются основные геометрические параметры.
Диагностика шлицевых соединений
Для контроля технического состояния шлицевых соединений применяются следующие методы диагностики:
- Визуальный и измерительный контроль шлицев
- Анализ вибрации вала
- Контроль биения вала
- Акустическая диагностика
Периодическая диагностика позволяет выявлять дефекты и начальную стадию износа шлицевых соединений для своевременного проведения ремонта и предотвращения аварий.
Примеры применения шлицевых соединений в промышленности
Рассмотрим несколько примеров использования шлицевых соединений в различных отраслях:
- В металлорежущих станках - соединение шпинделя и шестерен коробки скоростей
- В редукторах - соединение валов и шестерен
- В судовых дизелях - соединение коленчатого вала и маховика
- В ветроэнергетических установках - соединение ротора с редуктором
Таким образом, можно увидеть широкое применение шлицевых соединений во многих областях благодаря их надежности и технологичности.