Резьбонакатные станки - это высокотехнологичные устройства, позволяющие эффективно формировать резьбовые поверхности на деталях. Давайте подробно разберемся во всех аспектах этих полезных механизмов.
Назначение и принцип работы резьбонакатных станков
Резьбонакатные станки предназначены для нарезания всевозможных видов наружных резьб и профилей на цилиндрических заготовках. Это достигается за счет вращающихся стальных роликов, которые под давлением деформируют поверхность металлической заготовки, формируя на ней нужный профиль резьбы. Такой метод называется холодной накаткой.
Основные преимущества резьбонакатки:
- Высокая производительность обработки
- Хорошее качество поверхности
- Повышение прочности деталей
- Отсутствие стружки
С помощью резьбонакатных станков можно формировать:
- Цилиндрические резьбы
- Конические резьбы
- Трубные резьбы
- Шлицевые и зубчатые профили
- Червячные поверхности
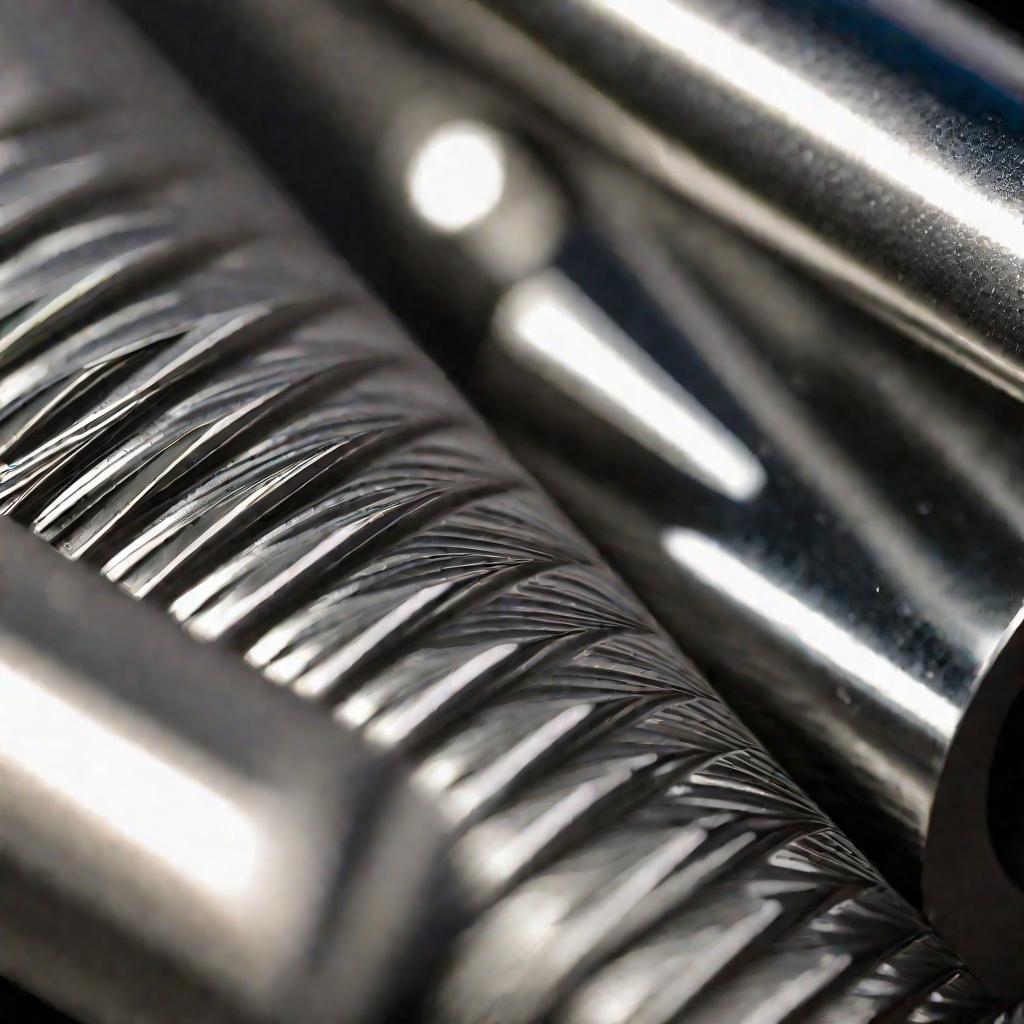
Применение резьбонакатных станков
Резьбонакатные станки широко используются в различных отраслях промышленности:
- Машиностроение - для изготовления резьбовых соединений, ходовых винтов, шпинделей и других деталей.
- Автомобилестроение - накатка резьбы на деталях двигателей, трансмиссий, элементах подвески.
- Авиастроение - производство резьбовых частей планеров, двигателей, приборов.
- Судостроение - изготовление крепежа, арматуры, обшивки для морских судов.
- Нефтегазовая отрасль - нарезка резьб на трубах, вентилях, фитингах.
Также резьбонакатные станки применяются на предприятиях, производящих:
- Крепеж (болты, гайки, шпильки)
- Трубы и трубные элементы
- Сантехнические изделия
- Гидравлическую арматуру
- Инструменты и оснастку
Типы резьбонакатных станков
Существует множество разновидностей резьбонакатных станков. Рассмотрим основные из них:
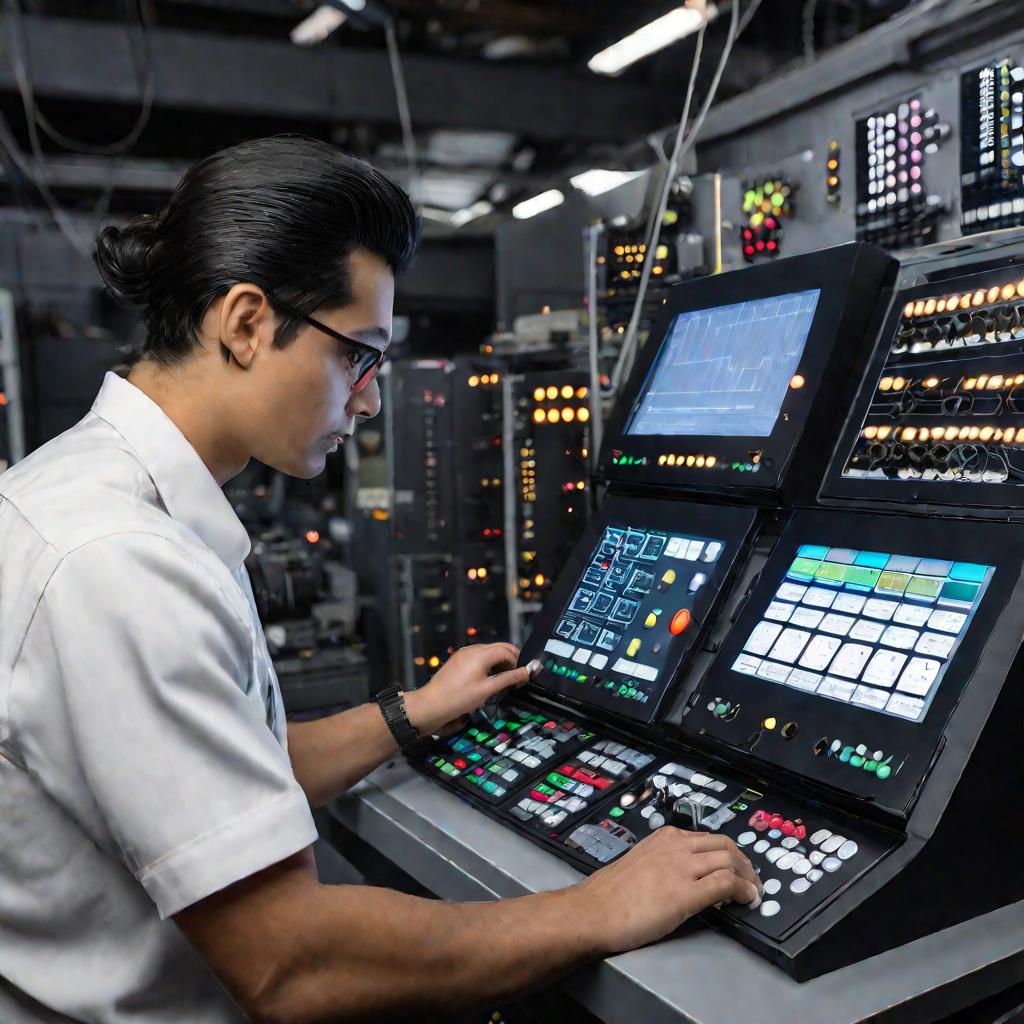
По типу конструкции:
- Односалазочные
- Двухсалазочные
- Трехроликовые
- Планетарные
По степени автоматизации:
- С ручным управлением
- Полуавтоматические
- Автоматические
- С ЧПУ
По производительности:
- Малой мощности
- Средней мощности
- Высокопроизводительные
- Скоростные автоматы
Наиболее распространенными производителями резьбонакатных станков являются: Profiroll (Германия), Rollwasch (Германия), EJOT (Германия), УПВ (Россия), ТВТ (Россия).
Выбор резьбонакатного станка
При выборе резьбонакатного станка необходимо учитывать:
- Тип и размер обрабатываемых заготовок
- Материал заготовок
- Требуемые параметры резьбы
- Производительность
- Требуемый уровень автоматизации
- Стоимость оборудования
Также важно обращать внимание на:
- Надежность и долговечность станка
- Простоту и удобство эксплуатации
- Возможность модернизации
- Качество сервиса и запчастей
Правильный подбор станка позволит оптимизировать процесс резьбонакатки и повысить эффективность производства.
Эксплуатация резьбонакатных станков
Эксплуатация резьбонакатных станков включает следующие этапы:
- Подготовка заготовок к обработке
- Установка резьбонакатных роликов
- Закрепление заготовки в станке
- Настройка параметров резьбы
- Запуск процесса накатки
- Контроль качества обработки
- Техническое обслуживание станка
Важнейшими аспектами при работе на станке являются:
- Соблюдение режимов резания и охлаждения
- Периодическая замена и заточка роликов
- Чистота рабочей зоны
- Регулярная смазка и проверка узлов
- Контроль износа механизмов
Грамотная эксплуатация позволяет обеспечить стабильно высокое качество резьб и длительный срок службы станка.
Перспективы развития резьбонакатных станков
Современные тенденции в конструировании резьбонакатных станков:
- Применение новых материалов для повышения износостойкости
- Увеличение точности и качества обработки
- Рост уровня автоматизации и использование робототехники
- Улучшение эргономики и интерфейса управления
- Интеграция в гибкие производственные системы
- Комбинирование различных методов обработки
Благодаря этим инновациям резьбонакатные станки будут выполнять обработку еще быстрее и качественнее, расширяя возможности современного машиностроения.
Особенности эксплуатации различных типов резьбонакатных станков
Эксплуатация резьбонакатных станков имеет свои нюансы в зависимости от типа оборудования:
Односалазочные станки
Для односалазочных станков характерны:
- Более простая конструкция и обслуживание
- Меньший вес и габариты
- Ограничения по длине обрабатываемых заготовок
- Необходимость точной центровки заготовки
Двухсалазочные станки
При эксплуатации двухсалазочных станков важно:
- Обеспечить синхронное перемещение салазок
- Контролировать биение оси вращения заготовки
- Следить за износом направляющих салазок
Планетарные станки
Особенности планетарных станков:
- Высокая производительность за счет нескольких роликов
- Сложность наладки взаимодействия роликов
- Повышенные требования к жесткости конструкции
Типичные неисправности резьбонакатных станков
К типичным неисправностям резьбонакатных станков относятся:
- Повышенный люфт в подшипниках валов
- Износ или поломка зубчатых передач
- Сбои в работе электропривода
- Нарушение регулировки натяжения ремней
- Загрязнение и износ направляющих салазок
Для предотвращения поломок необходимо регулярно проводить техобслуживание и замену изношенных элементов станка.
Системы ЧПУ на резьбонакатных станках
Системы ЧПУ позволяют:
- Автоматизировать процесс резьбонакатки
- Повысить точность обработки
- Сократить время переналадки
- Исключить брак при обработке
Однако программирование ЧПУ требует квалификации оператора.
Меры безопасности при работе на станках
Основные правила безопасности:
- Контроль целостности защитного кожуха
- Использование СИЗ при обслуживании
- Проверка надежности крепления заготовки
- Отключение станка при изменении режимов
- Содержание рабочей зоны в чистоте
Соблюдение инструкций по охране труда сводит к минимуму риск получения травм.