Ионно-плазменное напыление - передовая технология упрочнения и нанесения защитных покрытий на поверхность различных материалов. Эта технология позволяет значительно повысить износостойкость, коррозионную стойкость и другие эксплуатационные характеристики изделий практически любой сложности. Давайте разберемся, в чем заключается суть этого метода и какое оборудование для него используется.
1. Сущность ионно-плазменного напыления
Ионно-плазменное напыление основано на распылении материала в вакуумной камере с помощью высокотемпературной плазменной струи. При этом происходит ионизация и ускорение частиц напыляемого вещества, которые затем конденсируются на подложке, образуя покрытие.
Основные процессы при ионно-плазменном напылении:
- Испарение материала катода под действием дугового разряда.
- Ионизация паров материала в плазме разряда.
- Ускорение ионов в электрическом поле.
- Конденсация ионов на подложке с образованием покрытия.
По сравнению с другими методами нанесения покрытий, ионно-плазменное напыление имеет следующие преимущества:
- Возможность нанесения покрытий практически из любых материалов.
- Высокая адгезия покрытия за счет ионной бомбардировки.
- Хорошее качество покрытий благодаря отсутствию окисления.
- Низкая пористость и равномерная толщина покрытия.
Ионно-плазменное напыление широко применяется для упрочнения и нанесения износостойких, коррозионностойких, электроизоляционных и других функциональных покрытий в машиностроении, электронике, энергетике, авиакосмической и других отраслях промышленности.
2. Материалы для ионно-плазменного напыления
В качестве материалов для ионно-плазменного напыления могут использоваться:
- Металлы и сплавы (титан, алюминий, молибден, вольфрам, нержавеющая сталь)
- Тугоплавкие соединения (оксиды, карбиды, нитриды, бориды)
- Полимерные материалы (фторопласт, полиамид)
- Алмаз и алмазоподобные покрытия
- Керамика (оксид алюминия, диоксид циркония)
Наиболее распространенные материалы для ИПН:
- Нитрид титана - износостойкое покрытие золотистого цвета.
- Карбид хрома - высокая твердость и стойкость к абразивному износу.
- Оксид алюминия - высокая электроизоляция и теплопроводность.
- Фторопласт - антифрикционные свойства, химстойкость.
Выбор материала определяется нужными свойствами и условиями эксплуатации покрытия.
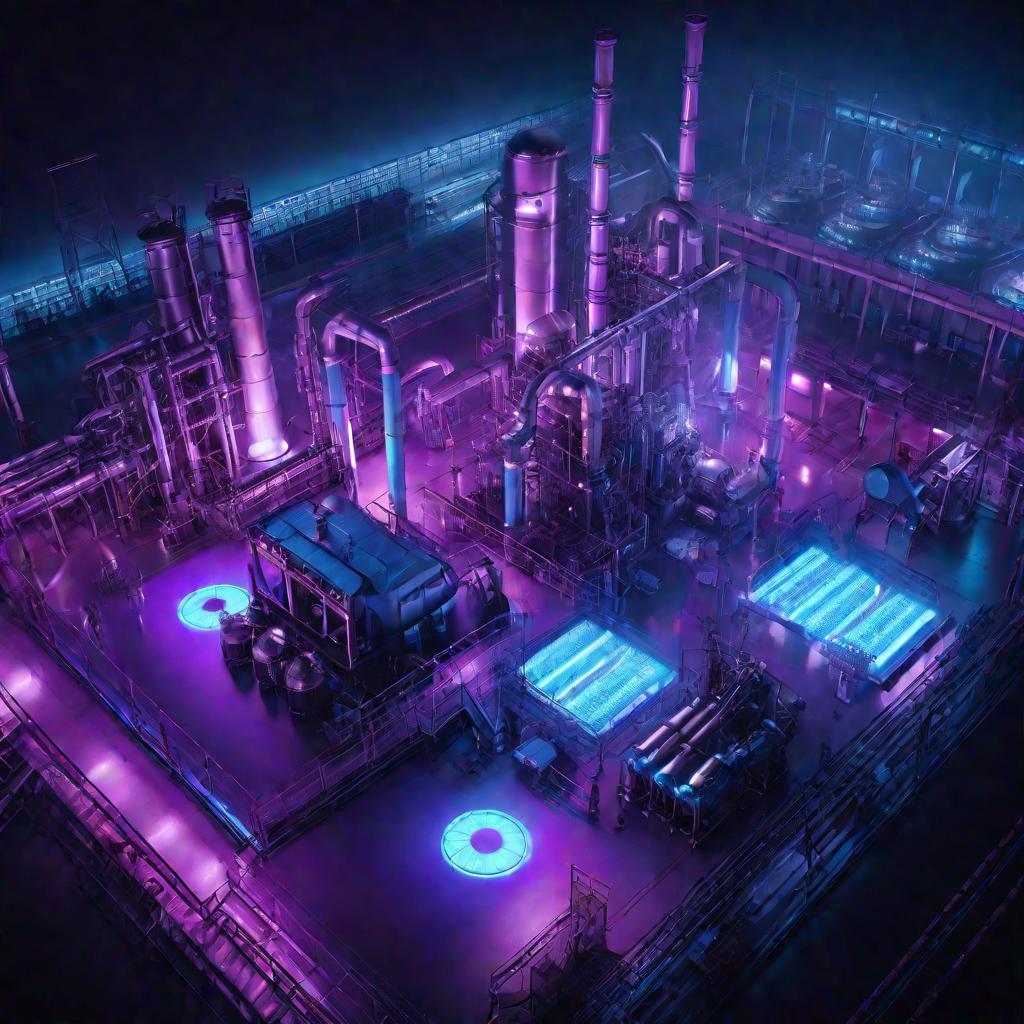
3. Подготовка поверхности перед напылением
Для обеспечения хорошего сцепления покрытия необходима тщательная подготовка поверхности:
- Обезжиривание органическими растворителями, щелочными или кислотными моющими средствами.
- Механическая очистка (пескоструйная обработка, шлифование).
- Травление в растворах кислот или щелочей.
- Активирование ионным или плазменным воздействием.
Подготовленная поверхность должна быть химически чистой, с развитой шероховатостью (Rz 20-40 мкм) и активной для смачивания распыленным материалом.
4. Оборудование для ионно-плазменного напыления
Установка ионно-плазменного напыления включает следующие основные узлы:
- Вакуумная камера с системой откачки.
- Источник питания (дуговой, ВЧ-генератор).
- Система подачи рабочих и плазмообразующих газов.
- Узел перемещения подложки.
- Системы охлаждения и нагрева.
Конструкция камеры ионно-плазменного напыления определяется габаритами и конфигурацией обрабатываемых изделий. Для напыления на небольшие детали используют неподвижные вакуумные камеры. Для крупных или длинномерных изделий применяют конвейерные установки непрерывного действия.
Вакуум в рабочей камере обеспечивает высокое качество покрытий за счет исключения окисления и загрязнения. Типичное давление при ИПН составляет 0,1-10 Па.
5. Режимы ионно-плазменного напыления
Основные технологические параметры процесса ИПН:
- Давление рабочего газа в камере.
- Сила тока дуги.
- Напряжение смещения на подложке.
- Расход плазмообразующего газа.
- Дистанция напыления.
- Скорость осаждения покрытия.
Регулируя эти параметры, можно влиять на структуру и свойства формируемого покрытия, оптимизируя процесс для конкретных задач.
Например, увеличение отрицательного потенциала смещения на подложке повышает плотность и адгезию покрытия за счет более интенсивной бомбардировки ионами.
Также важным параметром является температура подложки. Повышенная температура (300-500°C) обеспечивает лучшую подвижность атомов и формирование более плотного покрытия с мелкозернистой структурой.
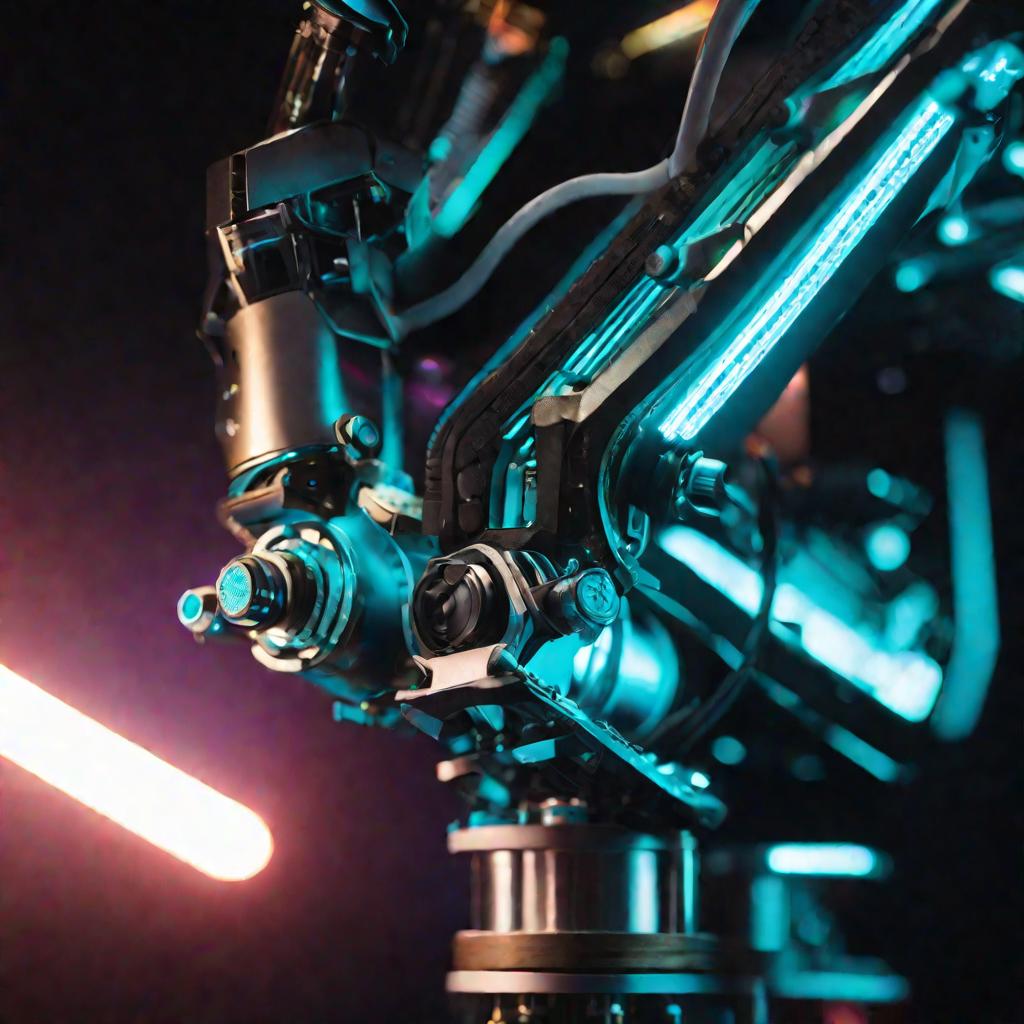
6. Контроль процесса и качества покрытий
Для обеспечения стабильности процесса ИПН и качества покрытий необходим постоянный контроль следующих параметров:
- Температура подложки.
- Толщина осаждаемого покрытия.
- Адгезия покрытия к подложке.
- Пористость покрытия.
- Фазовый состав и структура.
Температуру подложки контролируют с помощью термопар, установленных непосредственно на образце или на держателе. Толщину покрытия измеряют после напыления специальными толщиномерами.
Оценка адгезии проводится методом нормального отрыва, царапания алмазным индентором или методом акустической эмиссии. Для определения пористости используют металлографический анализ поперечных шлифов покрытия.
7. Применение ионно-плазменных покрытий
Ионно-плазменные покрытия широко применяются в различных отраслях промышленности:
- Машиностроение - износостойкие, антифрикционные покрытия деталей.
- Авиакосмическая отрасль - защитные покрытия лопаток турбин.
- Электроника - электроизоляционные пленки в микроэлектронике.
- Медицина - биосовместимые покрытия имплантатов.
Некоторые примеры применения ИПН:
- Нитрид титана на лопатках газотурбинных двигателей.
- Карбид вольфрама на режущем инструменте.
- Оксид алюминия в интегральных микросхемах.
- Гидроксиапатит на ортопедических имплантатах.
8. Достоинства и недостатки метода
Основные достоинства ИПН:
- Высокое качество и надежность покрытий.
- Возможность напыления на изделия сложной формы.
- Широкий выбор материалов для напыления.
К недостаткам ИПН можно отнести:
- Высокая стоимость оборудования.
- Ограничения по размерам обрабатываемых деталей.
9. Перспективы развития технологии ИПН
Актуальные направления совершенствования ионно-плазменного напыления:
- Разработка новых материалов покрытий.
- Комбинирование ИПН с другими методами обработки.
- Автоматизация и роботизация процессов напыления.
- Увеличение производительности и снижение стоимости.
Развитие нанотехнологий открывает новые возможности для создания уникальных наноструктурированных покрытий методом ионно-плазменного напыления.
Комбинирование ИПН с лазерной обработкой позволяет формировать функционально-градиентные покрытия с заданным распределением свойств.
Дальнейшее совершенствование технологии ИПН будет способствовать расширению областей ее применения и повышению качества получаемых покрытий.