Допуск позиционный - важная часть конструкторской документации, которая задает точность расположения элементов на чертеже. Давайте разберемся, что это такое, зачем нужно, как определяется и вычисляется. Узнаем практические советы по применению позиционных допусков.
Определение позиционного допуска
Что такое "допуск позиционный"?
Позиционный допуск - это допустимое отклонение расположения оси, центра или плоскости симметрии элемента относительно базовых точек или осей координат.
Иными словами, это область на плоскости или в пространстве, внутри которой должны находиться характерные точки рассматриваемого элемента (ось, центр, плоскость симметрии).
Назначение позиционных допусков
Зачем нужны позиционные допуски? Они необходимы для:
- Обеспечения собираемости изделия
- Обеспечения взаимозаменяемости деталей
- Установления требований к точности взаимного расположения элементов детали
Без соблюдения позиционных допусков сборка механизмов была бы затруднена или невозможна.
Виды позиционных допусков
Существуют следующие основные виды позиционных допусков:
- Допуски формы
- Отклонение от прямолинейности Отклонение от плоскостности Отклонение от круглости
- Допуски расположения
- Отклонение от параллельности Отклонение от перпендикулярности Отклонение от соосности
Такие допуски могут применяться как к отдельным поверхностям детали, так и к детали в целом.
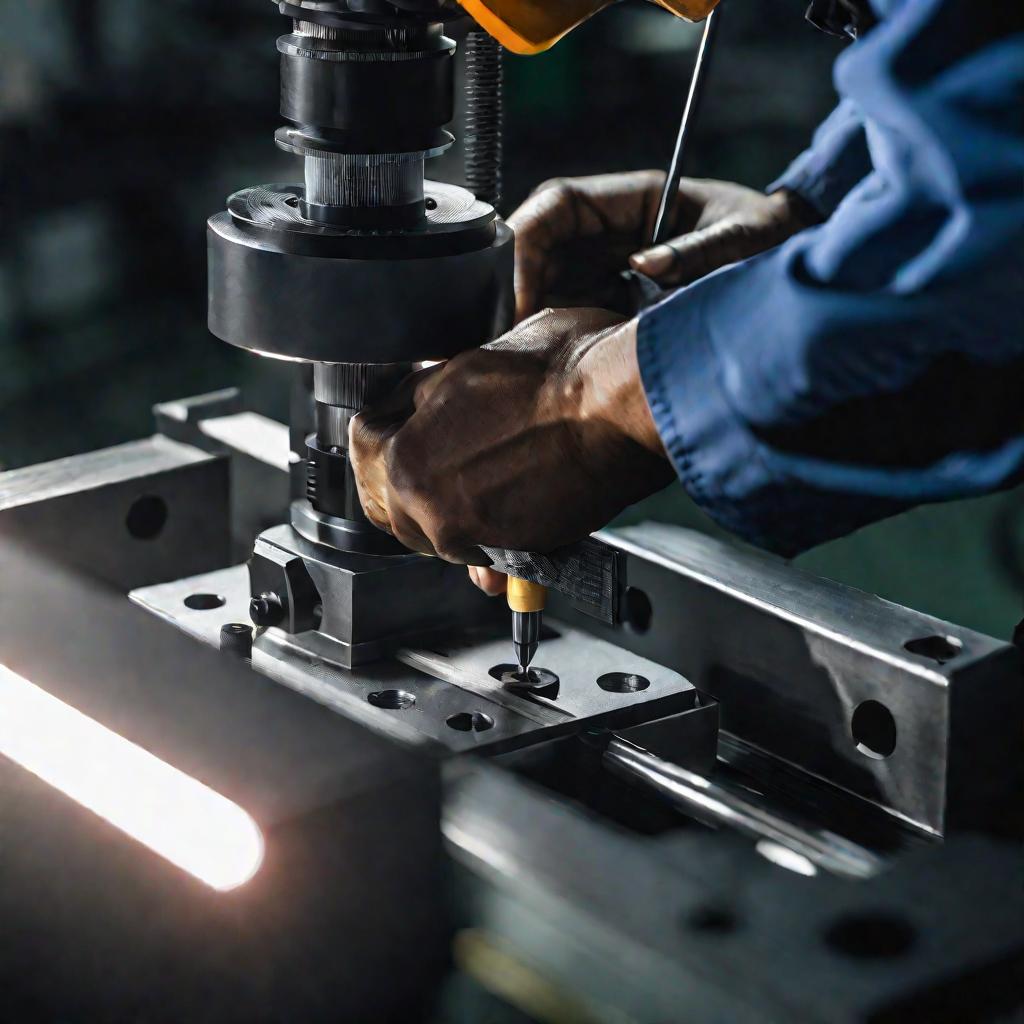
Обозначение позиционных допусков на чертеже
Позиционные допуски изображают на чертеже в виде рамки, которая поделена на несколько частей:
1 часть | Графическое обозначение допуска |
2 часть | Числовое значение допуска |
3 часть и далее | Буквенное обозначение баз |
Например:
Здесь в первой части рамки указан допуск формы (отклонение от прямолинейности), во второй части числовое значение 0,1 мм, в третьей базы А. От этой рамки линия со стрелкой указывает на поверхность, к которой относится данный позиционный допуск.
Перед числовым значением допуска могут стоять знаки:
- - неравномерный допуск;
- > или < - односторонний допуск.
Если допуск относится не ко всей поверхности, а только к участку, то этот участок выделяется штрихпунктирной линией.
Для одного элемента может быть указано несколько допусков - тогда рамки располагаются друг под другом.
Стандартные значения позиционных допусков по ГОСТ
ГОСТ устанавливает стандартные значения позиционных допусков в зависимости от:
- Класса точности детали или сборочной единицы
- Номинального размера поверхности или расстояния
Например, стандартные значения допуска прямолинейности в зависимости от длины проверяемого участка:
Длина участка, мм | Допуск прямолинейности для классов точности, мм |
до 10 | 0,02 (для высшей точности); 0,1 (для средней) |
от 10 до 50 | 0,1 (для высшей точности); 0,2 (для средней) |
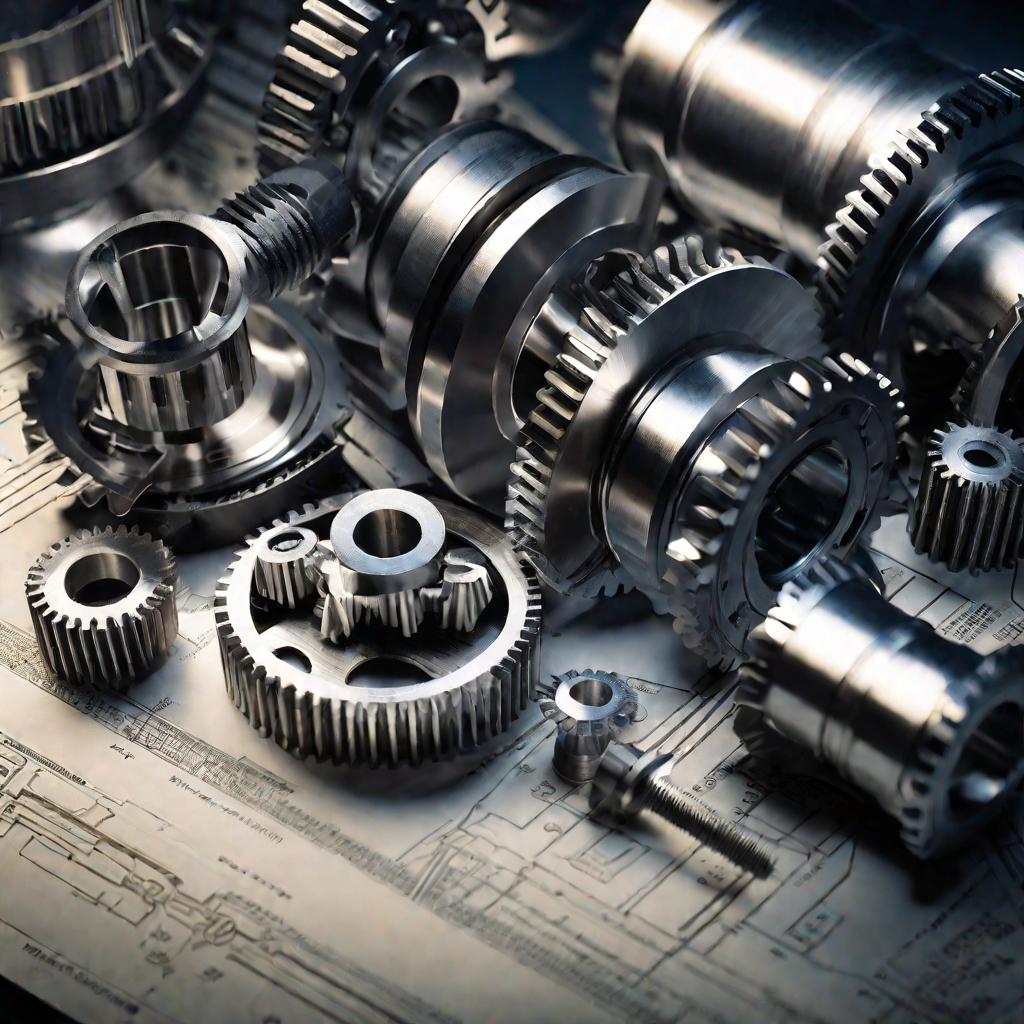
Пример вычисления позиционного допуска
Рассмотрим конкретный пример расчета значения позиционного допуска.
Допустим, в чертеже задано отверстие диаметром 25 мм. Расстояние от оси отверстия до базы по оси X составляет 50 мм, по оси Y - 80 мм. Указан позиционный допуск без обозначения радиуса или диаметра перед числовым значением. Числовое значение допуска - 0,1 мм.
В таком случае поле допуска представляет собой квадрат со стороной, равной удвоенному значению допуска. То есть сторона квадрата будет 0,2 мм.
Это значит, что фактическое положение оси отверстия может отклоняться от номинального (определяемого размерами 50 и 80 мм) не более чем на 0,1 мм в каждую сторону.
Зависимые позиционные допуски
Особый вид представляют зависимые позиционные допуски. В этом случае величина допустимого отклонения зависит от размеров самой детали.
Например, допуск может вычисляться по формуле:
где D - диаметр отверстия.
При обозначении такого допуска на чертеж добавляется символ М после числового значения или после базы.
Назначение позиционных допусков
При назначении позиционных допусков следует учитывать:
- функциональное назначение поверхности;
- технологичность обработки поверхности;
- точность базирования заготовки;
- точностные параметры станка.
Правильный выбор допусков позволяет оптимизировать технологический процесс.
Контроль позиционного допуска
Как проверить, удовлетворяет ли реальная деталь заданному позиционному допуску?
Для контроля позиционных допусков используются следующие методы:
- Измерение координат характерных точек (центров отверстий, осей пазов и т.п.) с помощью координатно-измерительных машин;
- Применение специальных калибров для контроля взаимного расположения поверхностей;
- Использование оптических, пневматических и электронных приборов (например, автоколлиматоров).
Полученные данные сравниваются с допустимыми значениями, указанными на чертеже. Делается заключение о соответствии детали заданному позиционному допуску.
Типичные ошибки при работе с позиционными допусками
При назначении и контроле позиционных допусков часто встречаются следующие ошибки:
- Неправильный выбор типа допуска, не соответствующий функциональному назначению;
- Завышение допустимых отклонений, что приводит к увеличению брака;
- Неучет влияния технологических возможностей;
- Некорректное нанесение обозначений допусков на чертеж;
- Ошибки при измерениях и вычислениях.
Все это может стать причиной нарушения работоспособности конструкции.
Рекомендации по применению позиционных допусков
Для правильного назначения позиционных допусков рекомендуется:
- Анализировать функциональное назначение детали и условия ее эксплуатации;
- Учитывать технологические возможности производства при обработке поверхностей;
- Правильно выбирать базовые поверхности;
- Ориентироваться на рекомендуемые значения допусков в зависимости от класса точности;
- Проверять влияние допусков на точность сопряжения с другими деталями в сборке.
Выбор базовых поверхностей
В качестве баз при назначении позиционных допусков обычно используют:
- Поверхности, образованные технологическими базами
- Поверхности, имеющие наибольшую точность обработки
- Плоскости симметрии детали
Анализ условий эксплуатации
Необходимо учитывать:
- Характер сопряжения детали с другими деталями
- Наличие подвижных или неподвижных соединений
- Возможные нагрузки и вибрации при работе
При назначении допусков следует учитывать возможности технологического оборудования и оснастки для обработки данной поверхности. Например:
- Точность станков (погрешность позиционирования, жесткость и т.д.)
- Систему базирования и закрепления заготовки
- Точность измерительного оборудования
- Квалификацию персонала
Это позволит назначить оптимальные допуски, которые реально выполнимы в заданных производственных условиях.
Проверка влияния позиционных допусков на точность сборки
На заключительном этапе нужно проверить, как назначенные позиционные допуски влияют на точность взаимного расположения сопрягаемых поверхностей этой детали и смежных деталей после сборки.
Для этого необходимо:
- Задать допуски формы и расположения сопрягаемых поверхностей
- Построить размерные цепи
- Рассчитать возможные суммарные отклонения
Если расчет показывает нарушение работоспособности конструкции, следует скорректировать назначенные ранее допуски.
Корректировка позиционных допусков
Если расчет точности сборки показал недостаточную точность из-за выбранных позиционных допусков, то необходима корректировка.
Возможные решения:
- Ужесточение допусков формы и расположения поверхностей рассматриваемой детали или сопрягаемых с ней деталей;
- Замена системы базирования;
- Применение дополнительных пригоночных операций для критических поверхностей;
- Изменение конструкции сопряжения или введение компенсирующих элементов.
Конкретные решения определяются конструктором в зависимости от особенностей изделия с учетом технологических возможностей и экономической целесообразности.
Автоматизация назначения позиционных допусков
Для облегчения работы конструктора существуют программные комплексы автоматизированного проектирования (САПР), которые позволяют:
- Автоматически назначать стандартные допуски в соответствии с ГОСТ при создании модели;
- Контролировать непротиворечивость допусков сопрягаемых деталей в сборке;
- Проводить анализ размерных цепей и проверять обеспечение заданной точности сборки по критериям работоспособности.