Дефектовка - важнейший этап подготовки к ремонту любого оборудования. От качества ее проведения зависит дальнейший процесс восстановления деталей. Дефектовка позволяет выявить все дефекты, оценить техническое состояние деталей и составить оптимальный план их ремонта.
В данной статье мы подробно рассмотрим основные методы и процесс дефектовки, ее роль в подготовке к ремонту, правила составления ведомости дефектов.
Методы дефектовки деталей
Дефектовка деталей - это важный этап в процессе ремонта техники. От того, насколько качественно проведена дефектовка, зависит дальнейший ремонт детали и всего узла или агрегата. Для выявления дефектов используются различные методы:
- Визуальный осмотр - позволяет увидеть внешние дефекты, такие как трещины, забоины, деформации.
- Остукивание - помогает определить внутренние дефекты по изменению звука.
- Гидравлические испытания - выявляют скрытые полости и трещины в корпусных деталях.
- Измерения - определяют отклонения размеров и форм деталей.
- Проверка твердости - выявляет изменения свойств материалов.
- Проверка сопряжений - определяет качество и работоспособность соединений деталей.
- Дефектоскопия - обнаруживает скрытые дефекты в металле.
Каждый из этих методов применяется в зависимости от особенностей детали и предполагаемого характера дефектов. Их совокупное использование позволяет максимально точно определить все имеющиеся дефекты и повреждения. Это необходимо для выбора оптимального метода дальнейшего ремонта или восстановления детали.
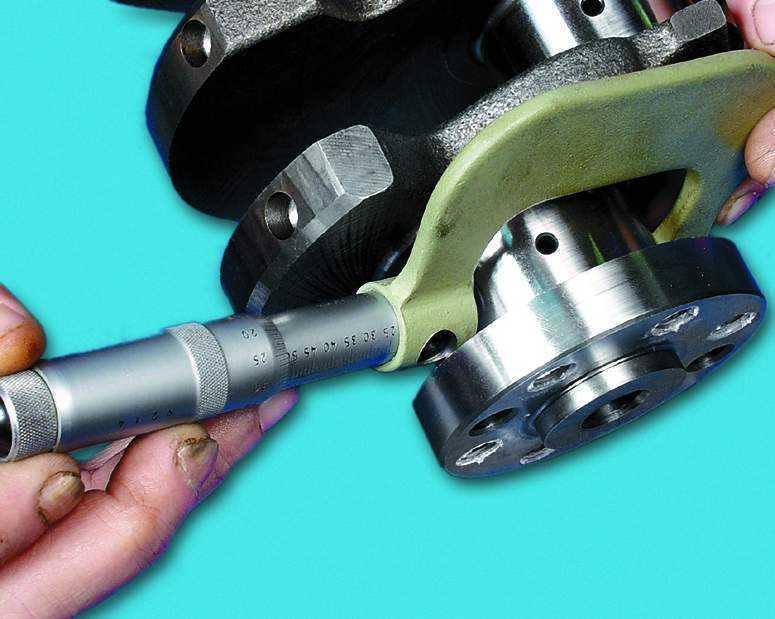
Таким образом, применение различных методов дефектовки является основой качественного анализа состояния детали и обеспечивает технологичность последующего ремонта.
Порядок проведения дефектовки
Процесс дефектовки деталей должен выполняться в определенной последовательности, чтобы обеспечить выявление всех дефектов:
- Подготовка к дефектовке. Детали должны быть чистыми и сухими. Необходимо подобрать измерительный инструмент в соответствии с особенностями детали.
- Визуальный осмотр. Проводится для выявления видимых повреждений поверхности, таких как трещины, вмятины, коррозия.
- Остукивание детали молотком. Помогает определить внутренние дефекты по изменению звука.
- Гидравлические испытания корпусных деталей. Выявляют наличие внутренних полостей и трещин.
- Измерение размеров и формы деталей. Проводится с помощью измерительных инструментов.
- Проверка твердости материала детали. Определяет изменения механических свойств.
- Проверка качества сопряжений с другими деталями узла.
- Дефектоскопия для выявления скрытых дефектов.
- Составление ведомости выявленных дефектов.
Все перечисленные методы используются в комплексе и в определенной последовательности. Например, сначала проводится визуальный осмотр и измерения, затем, в зависимости от конструкции детали, дополнительно применяют остукивание, гидроиспытания или дефектоскопию. Их очередность может варьироваться.
Правильная организация процесса дефектовки позволяет сократить временные затраты за счет исключения ненужных или дублирующих методов контроля. Опытный технолог должен четко представлять конструктивные особенности каждой детали и возможные для нее дефекты. Это поможет оптимизировать выбор методов дефектовки в каждом конкретном случае.
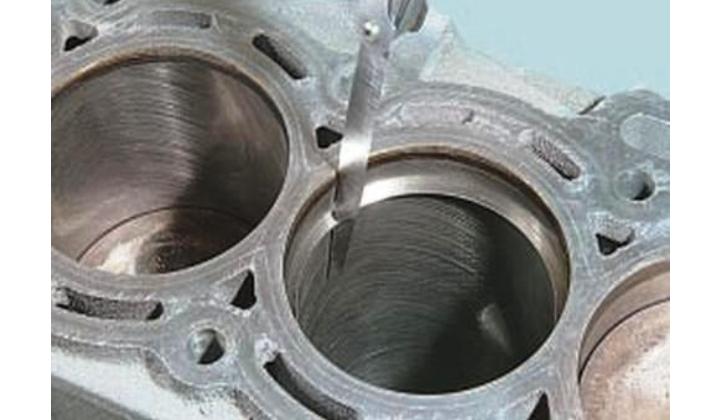
Таким образом, правильная последовательность и комплексное применение различных методов контроля при дефектовке являются залогом полноты и достоверности информации о состоянии детали. А это, в свою очередь, определяет обоснованность принимаемых решений о способе дальнейшего ремонта или восстановления детали.
Дефектовка - основа для ремонта
Дефектовка деталей является важнейшим этапом, предшествующим ремонту. От качества ее проведения зависит обоснованность выбора методов восстановления деталей и, как следствие, надежность и долговечность отремонтированных узлов.
В процессе дефектовки решаются следующие задачи:
- Выявление всех дефектов детали, их локализация и оценка степени.
- Определение причин возникновения дефектов.
- Оценка ремонтопригодности детали.
- Выбор метода устранения каждого дефекта.
- Составление ведомости дефектов.
Для решения этих задач требуется комплексный подход с использованием всех необходимых методов диагностики. Только в этом случае можно получить полную и достоверную информацию о состоянии детали.
На основании данных дефектовки принимается решение о способе ремонта детали:
- Возможно ли восстановление детали или требуется изготовление новой.
- Какой метод ремонта оптимален для устранения каждого дефекта с учетом ресурсов предприятия.
- Целесообразность ремонта детали с экономической точки зрения.
Таким образом, именно на стадии дефектовки закладываются основы качественного ремонта. Ее результаты определяют оптимальную ремонтную технологию. Поэтому от квалификации дефектовщиков, применения ими современных методов диагностики, точности и полноты ведомости дефектов напрямую зависит качество ремонта.
Дефектовка позволяет также оценить типичные причины отказов данной детали. Эта информация используется для совершенствования ее конструкции, технологии изготовления и эксплуатации. То есть дефектовка дает ценные данные для повышения надежности и долговечности деталей.
Составление ведомости дефектов
Ведомость дефектов является одним из основных документов, оформляемых по результатам дефектовки. В ней содержится полная информация о всех выявленных повреждениях и износах детали.
При составлении ведомости дефектов необходимо:
- Зафиксировать точное наименование и обозначение каждой дефектованной детали.
- Подробно описать характер, степень, локализацию и предполагаемые причины каждого дефекта.
- Указать размеры дефектных участков, величину износа, отклонения формы и т.д.
- Предложить возможные методы устранения каждого дефекта с учетом его особенностей.
Для удобства анализа и использования ведомости дефектов все повреждения группируются по их характеру и локализации. Например, отдельно описываются износы трущихся поверхностей, отклонения размеров и формы, механические повреждения, коррозия и т.д.
Качественно составленная ведомость дефектов позволяет определить оптимальные методы ремонта с учетом имеющегося на предприятии оборудования и технологических возможностей. Кроме того, на ее основе рассчитывается трудоемкость ремонтных работ.
Таким образом, ведомость дефектов является важнейшим техническим документом, от качества которого зависит обоснованность принимаемых решений на всех последующих этапах ремонта. Поэтому к ее составлению нужно подходить с особой тщательностью и ответственностью.
Типовые формы ведомостей дефектов
Для оптимизации процесса дефектовки и составления ведомостей дефектов целесообразно использовать типовые формы на наиболее массовые детали.
Типовая форма ведомости дефектов содержит:
- Перечень всех элементов и поверхностей данной детали.
- Возможные дефекты каждого элемента.
- Рекомендуемые методы устранения типовых дефектов.
При дефектовке конкретной детали в такой форме отмечают выявленные дефекты и выбирают методы их устранения из рекомендованного перечня.
Использование типовых форм ведомостей дефектов дает следующие преимущества:
- Сокращает время составления ведомости.
- Снижает вероятность упущения дефектов.
- Облегчает выбор метода ремонта.
- Стандартизирует оформление документации.
Типовые формы целесообразно разрабатывать на основе анализа данных о типичных отказах наиболее массовых деталей. Их использование способствует повышению качества дефектовки и ремонта.
Роль дефектовки в оптимизации ремонта
Качественно проведенная дефектовка позволяет оптимизировать процесс ремонта деталей за счет следующих факторов:
- Обоснованный выбор способа ремонта на основе объективной информации о характере и степени дефектов.
- Возможность оценить целесообразность ремонта vs изготовления новой детали.
- Планирование ремонтных работ и расчет затрат исходя из реального состояния детали.
Кроме того, данные дефектовки используются для:
- Анализа качества и надежности деталей, выявления слабых мест конструкции.
- Выработки рекомендаций по повышению долговечности и ремонтопригодности деталей.
- Совершенствования нормативов технического обслуживания и ремонта.
Таким образом, дефектовка является основой оптимизации всех этапов жизненного цикла детали - от проектирования до эксплуатации и ремонта. Качество ее выполнения напрямую влияет на технико-экономические показатели ремонтного производства.