Шариковые подшипники широко используются в различных отраслях промышленности. Правильный подбор размеров шариков в таких подшипниках имеет принципиальное значение для обеспечения надежной и долговечной работы механизмов. Давайте разберемся в требованиях к размерам шариков в шарикоподшипниках.
Способы изготовления шариков
Существует несколько основных способов производства шариков для подшипников:
- Литье - изготовление чугунных заготовок будущих шариков;
- Прессование - придание формы шарикам из прутковой стали;
- Шлифовка - доведение шариков до заданных размеров и шероховатости;
- Нанесение покрытий - например, хромирование или никелирование.
Наиболее распространен способ прессования. Стальную заготовку продавливают через матрицу с полусферическим углублением. Затем шарик подвергается дополнительной обработке на обдирочных станках для придания идеально сферической формы.
Очень важный этап - термическая обработка шариков, обеспечивающая необходимую твердость и износостойкость. После закалки и отпуска шарики проходят контроль качества - проверяются диаметр, форма, шероховатость поверхности.
Материалы для шариков
Согласно ГОСТ 3722-81 шарики для подшипников чаще всего изготавливают из стали марки ШХ15. Возможно применение и других марок стали в зависимости от требуемых характеристик:
- ШХ4, ШХ6С - повышенная твердость;
- 95Х18, 12Х18Н10Т - высокая коррозионная стойкость.
Для получения заготовок используется высококачественная хромистая или кремний-марганцевая стальная проволока. Иногда применяют бронзу, латунь, алюминий, пластмассы и другие современные материалы.
В последнее время активно ведутся разработки по применению наноструктурированных керамических материалов, таких как нитрид кремния, обладающих уникальным комплексом физико-механических свойств.
Тщательный подбор материалов позволяет оптимизировать характеристики шариков для конкретных условий эксплуатации подшипников.
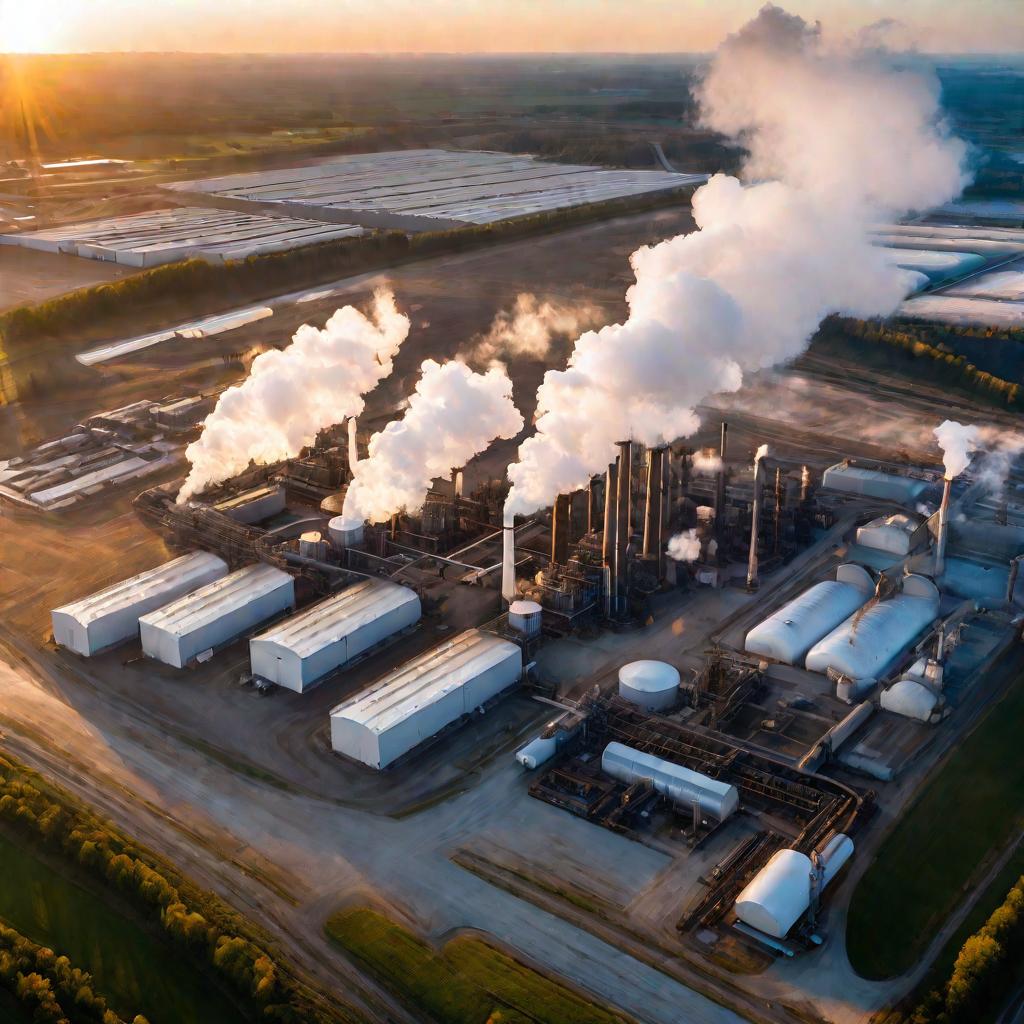
Сферы применения шариков
Шарики в подшипниках используются в самых разных областях:
- Машиностроение;
- Автомобилестроение;
- Сельскохозяйственная техника;
- Робототехника;
- Медицинское оборудование;
- Авиация и космонавтика.
Шарики могут работать в узлах со сложными условиями: высокие скорости, нагрузки, температуры, агрессивные среды. Поэтому к их качеству предъявляются особые требования.
Кроме подшипников, стальные шарики применяются в шариковых ручках, роликах, опорах, дверных петлях, замках, линейных направляющих, пневмоприводах и других механизмах.
Требования к размерам шариков
Размеры шариков в подшипниках регламентируются стандартом ГОСТ 3722-81. В нем определены допуски на диаметр, форму, шероховатость поверхности.
Отклонение среднего диаметра шариков от номинального значения не должно превышать 6-12 мкм в зависимости от класса точности. Разница между наибольшим и наименьшим диаметрами в партии - не более 15 мкм.
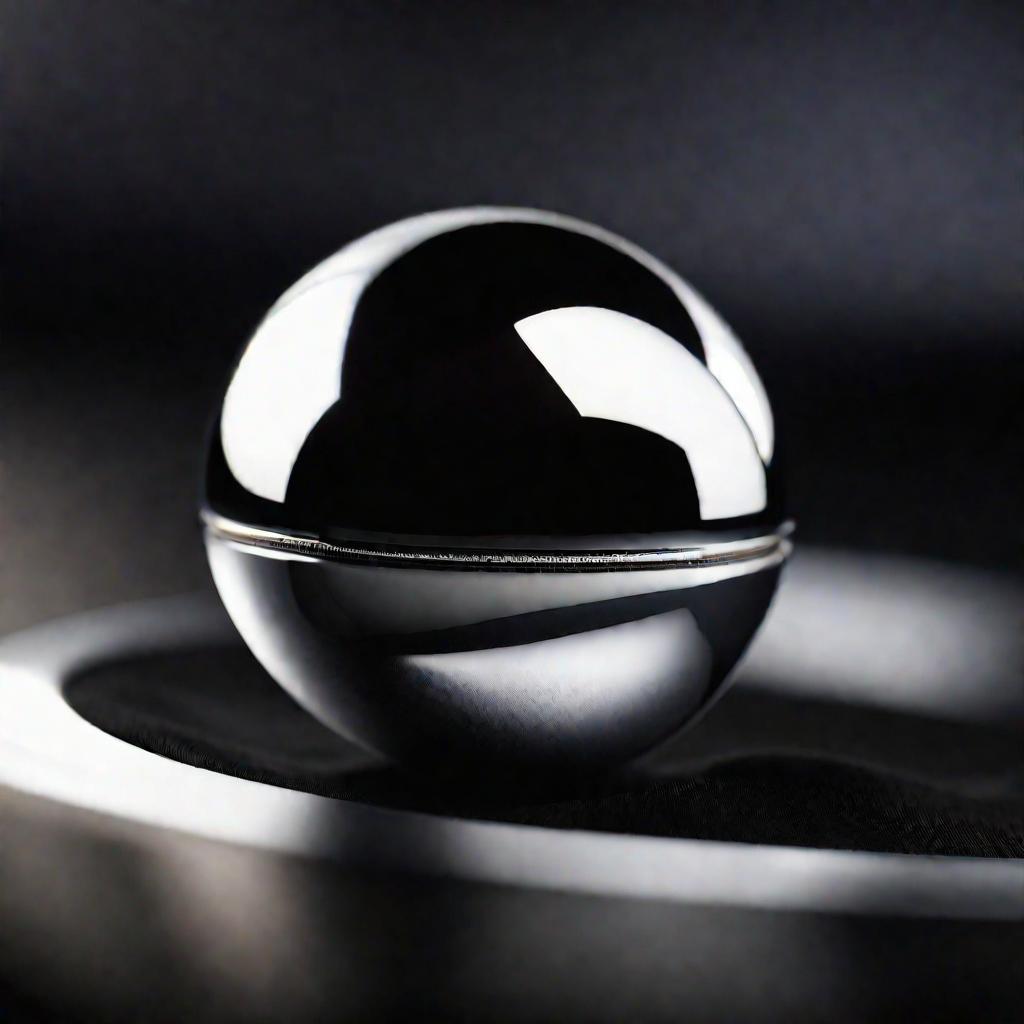
Контроль качества шариков
После изготовления все шарики проходят входной контроль:
- Измерение диаметров;
- Проверка формы на кругломерных станках;
- Контроль шероховатости;
- Металлографический анализ микроструктуры;
- Испытания на твердость.
Только шарики, отвечающие заданным параметрам, используются для комплектации подшипников.
Маркировка шариковых подшипников
Маркировка подшипников обычно содержит обозначение его типа и размера. Например, шариковый радиальный однорядный подшипник с внутренним диаметром 30 мм:
180200 - условное обозначение типа подшипника;
30 - внутренний диаметр, мм.
По маркировке можно определить требуемые размеры шариков в конкретном подшипнике.
Подбор шариков по каталогам
Существуют справочники и каталоги, где для каждого типоразмера подшипника указаны используемые в нем шарики.
Это позволяет быстро подобрать необходимые размеры шариков, если известен тип подшипника.
Замена шариков при ремонте
При ремонте подшипников часто требуется заменить изношенные или поврежденные шарики.
В таких случаях необходимо точно подобрать новые шарики по размерам, чтобы восстановить работоспособность подшипника.
Для этого следует либо измерить оставшиеся шарики, либо определить их диаметр по маркировке подшипника.
Качество поверхности шариков
Помимо размеров, важнейшей характеристикой шариков является качество их поверхности.
Шероховатость поверхности шариков не должна превышать 0,025-0,32 мкм в зависимости от класса точности подшипника.
Наличие дефектов на поверхности - царапин, вмятин, рисок - недопустимо, так как это приводит к повышенному износу и снижению долговечности.
Точность формы шариков
Форма шариков должна быть максимально близка к идеальной сфере. Отклонение от сферичности по ГОСТ не должно превышать 2-5 мкм.
Это обеспечивается высокой точностью оборудования для шлифовки и доводки шариков.
Термообработка шариков
Для придания необходимой твердости шарики подвергают термообработке - закалке и низкому отпуску.
После закалки твердость шариков достигает 63-66 HRC. Затем следует низкий отпуск при температуре до 250°С для снятия внутренних напряжений.
Упаковка и хранение шариков
Шарики поставляются упакованными в специальную тару, исключающую повреждение поверхности.
При хранении необходимо исключить попадание влаги, которая может привести к коррозии.
Температура хранения от -40 до +50°С.
Применение неметаллических материалов
Помимо стали для шариков активно применяются неметаллические материалы:
- Керамика;
- Пластмассы;
- Стекло.
Они используются в узлах, работающих без смазки, а также в агрессивных средах.