Наплавка металла является эффективным способом повышения износостойкости и восстановления деталей машин и оборудования. Применение специальных электродов позволяет получить качественный наплавленный слой с требуемыми свойствами.
История развития наплавки
Первые работы по наплавке относятся к 1920-м годам, когда было установлено, что наплавка повышает стойкость буровых долот более чем в 10 раз. С тех пор наплавка стала эффективным средством борьбы с износом деталей.
Уже к концу 1920-х годов наплавку стали применять повсеместно в металлообработке.
Способы наплавки металла
Различают газовую и электрическую наплавку. При газовой используют горение природного газа или ацетиленокислородной смеси. Электрическая бывает дуговой, импульсной, искровой и в виде их комбинаций.
Наиболее распространен способ дуговой наплавки покрытым электродом. Это обусловлено относительной дешевизной оборудования и материалов, а также возможностью ручного управления процессом.
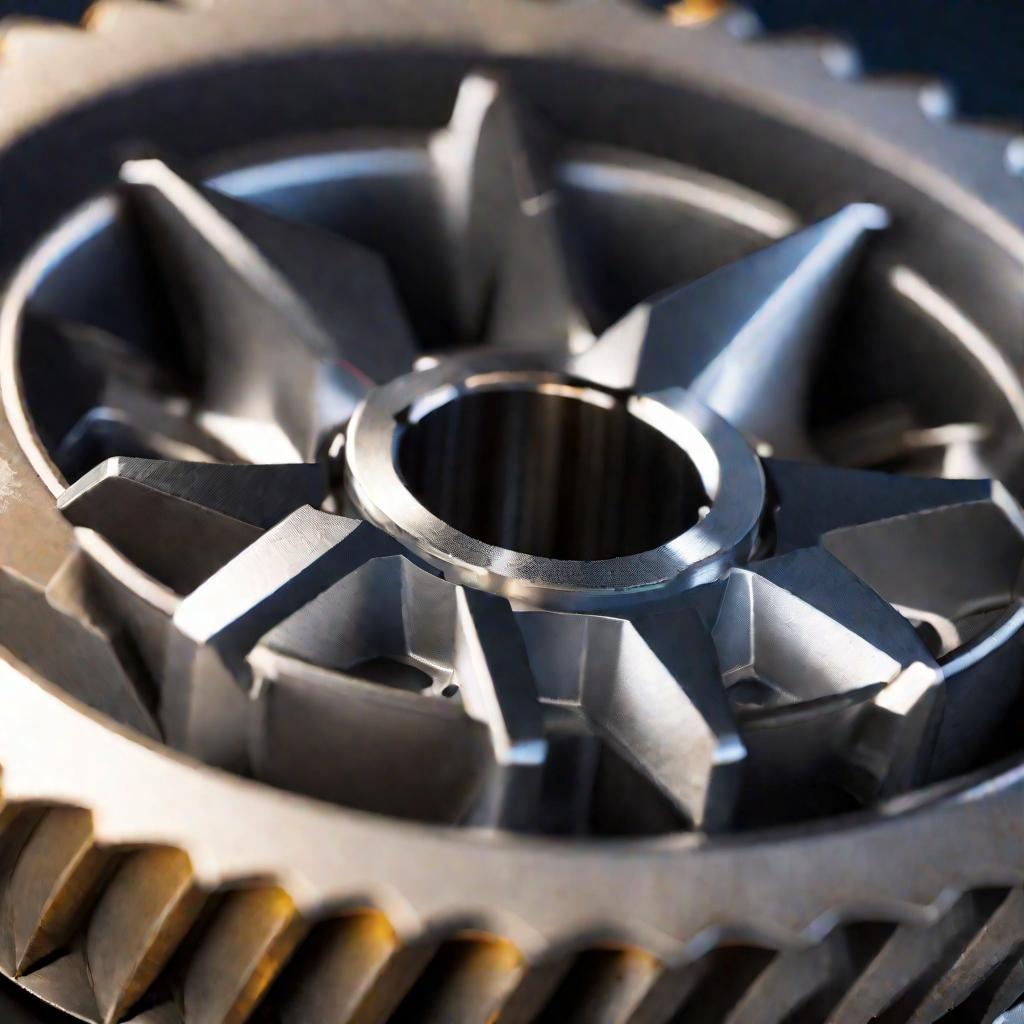
Электроды для наплавки стали
Как и при сварке, для наплавки применяют специальные расходные материалы – электроды. Однако если при сварке важнее прочность соединения, то от наплавки требуется улучшение эксплуатационных свойств поверхности:
- повышенная твердость
- стойкость к истиранию
- термоустойчивость
Это позволяет увеличить межремонтный срок службы деталей.
Существует более 40 марок электродов для наплавки, отличающихся химическим составом наплавляемого металла и его свойствами.
Требования к электродам
Химический состав электродов должен максимально соответствовать материалу детали. В противном случае возникают внутренние напряжения в металле.
Для получения стойкого к истиранию слоя необходимо образование карбидных соединений на поверхности за счет легирующих элементов и углерода. Это обеспечивает высокую твердость наплавки при сохранении пластичности.
По убыванию износостойкости основные легирующие элементы располагаются в ряду: W > Mo > Cr > многокомпонентные карбиды.
Маркировка электродов для наплавки
Маркировка наплавочных электродов указывает на основные характеристики материала:
- марку наплавочного металла
- диаметр и длину
- обозначение стандарта
- обозначение предприятия-изготовителя
Например, маркировка Нп-30Х28С2Г2Р означает следующее:
- Нп – электрод для наплавки
- 30Х28С2Г2Р – марка наплавляемого сплава
Применение различных электродов
Для наплавки применяются электроды на основе различных сплавов. Выбор конкретной марки зависит от условий работы детали и требуемых характеристик поверхности.
Быстрорежущие стали
Электроды с быстрорежущими сталями используются при повышенных скоростях трения. Обеспечивают высокую твердость и жаропрочность наплавки.
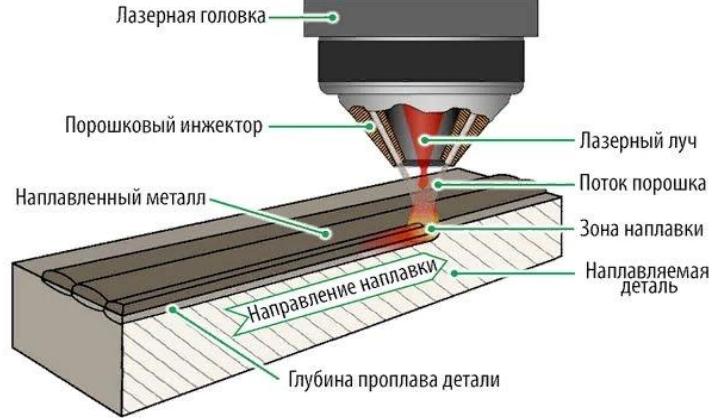
Аустенитные Cr-Ni стали
Аустенитные хромоникелевые электроды применяются в агрессивных средах благодаря коррозионной стойкости. Поверхность получается пластичной и вязкой.
Параметры режима наплавки
Для качественной наплавки важно соблюдать режим по силе тока. Отклонения приводят к дефектам наплавленного слоя.
Определяющим параметром является коэффициент наплавки электродов - масса наплавленного металла, приходящаяся на 1 кг израсходованных электродов. Коэффициент показывает эффективность использования материала.
Контроль качества наплавки
Качество наплавки, в том числе химический состав, структуру и твердость металла контролируют по специальным образцам-свидетелям с нанесенным слоем.
Требования к образцам
Размеры пластин-свидетелей, режим наплавки и количество слоев регламентированы ГОСТом.
Оборудование для наплавки
Для ручной дуговой наплавки применяют источник питания, электрододержатель, провода и расходные материалы – электроды. Может использоваться автоматизация процесса.
Подготовка поверхности
Перед наплавкой поверхность детали тщательно зачищают от ржавчины, окалины, краски и других загрязнений. Это обеспечивает хорошее сцепление наплавленного металла с основой.
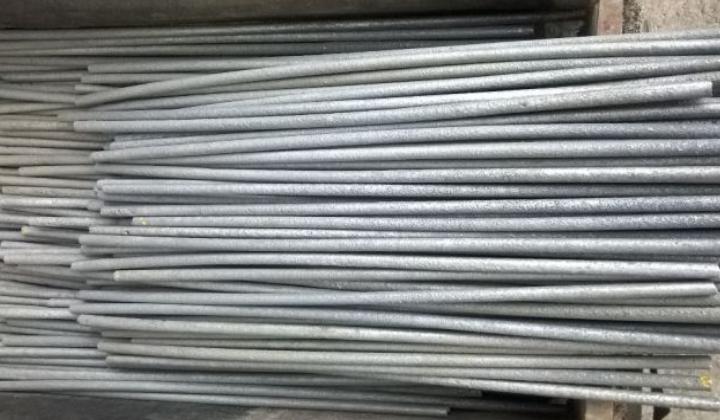
Механическая обработка
Применяют абразивные круги, наждачную бумагу, скребки или пескоструйную обработку. Удаляются дефектные участки, придается шероховатость поверхности.
Обезжиривание и сушка
После механической очистки поверхность обезжиривают с помощью растворителей и сушат. Это предотвращает пористость наплавки.
Техника наплавки
Существует несколько приемов наплавки в зависимости от положения и перемещения электрода:
- нижнее, горизонтальное, вертикальное, потолочное положение;
- поперечные, продольные, круговые движения.
Выбор зависит от формы детали, типа соединения, толщины наплавляемого слоя.
Допустимое количество слоев
Число наплавляемых слоев ограничивается 2-3 из-за опасности появления трещин. После зачистки допускается наплавка следующих слоев.
Закалка наплавленного слоя
Для повышения твердости и износостойкости наплавку подвергают термической обработке - закалке в масле или на воздухе с последующим отпуском.
Автоматизация процесса наплавки
В современном производстве широко применяется автоматизация наплавки с использованием специальных установок.
Преимущества автоматизации
- Повышение производительности и качества;
- Снижение трудозатрат;
- Возможность одновременной обработки нескольких деталей.
Типы автоматических установок
Применяют кольцевые, планетарные, карусельные установки и установки на базе промышленных роботов.
Устройства могут совершать круговые, возвратно-поступательные и вращательные движения относительно оси детали, повторяя движения сварщика.
Механизация подачи электродной проволоки и защитного газа
Для повышения производительности и улучшения условий труда сварщика применяют автоматическую подачу электродной проволоки и защитного газа в зону горения дуги.
Роботизированная наплавка
Наиболее перспективным направлением является полностью автоматизированная роботизированная наплавка с использованием многокоординатных промышленных роботов.
Выбор режима наплавки
Правильный выбор режима наплавки (силы тока, напряжения, скорости перемещения электрода) определяет качество наплавленного слоя.
Влияние параметров режима
- Сила тока влияет на глубину проплавления;
- Напряжение определяет форму и размеры наплавленных валиков;
- Скорость перемещения - ширину валиков.
Неправильно выбранный режим приводит к дефектам: подрезы, непровары, пористость, трещины.
Рекомендации по выбору
Режим наплавки выбирают в зависимости от марки электрода, толщины изделия, требуемых свойств. Рекомендуется придерживаться данных производителя электродов.
Виды дефектов наплавки
Основные дефекты наплавленного слоя:
- Трещины;
- Пористость;
- Шлаковые и металлические включения;
- Непровары и подрезы.
Причины возникновения дефектов
Дефекты, как правило, связаны с нарушениями технологии наплавки или неверным выбором режима и материалов.
Контроль качества наплавки
Качество наплавки проверяют визуальным осмотром, а также методами неразрушающего контроля: радиографией, ультразвуком, магнитопорошковой дефектоскопией.
Технология наплавки особых поверхностей
Существуют особенности наплавки отдельных типов деталей и рабочих поверхностей.
Наплавка внутренних поверхностей
Для наплавки отверстий и полостей применяют специальные электроды небольших диаметров. Используют приспособления, обеспечивающие подачу защитного газа в зону дуги.
Наплавка резьбовых соединений
Перед наплавкой резьбы зачищают накаткой с помощью метчиков. Применяют тонкие электроды, наплавляют точечно или короткими строчками вдоль профиля резьбы.
Ремонтная наплавка
Наплавка является эффективным способом восстановления и ремонта изношенных деталей машин и механизмов.
Преимущества ремонтной наплавки
- Экономическая эффективность по сравнению с заменой детали;
- Возможность многократного применения;
- Восстановление геометрических размеров деталей.
Выбор оптимального варианта наплавки
При выборе технологии наплавки анализируют требования к детали, ее условия работы и экономическую эффективность различных вариантов.