Допуск прямолинейности - один из важнейших показателей качества деталей в машиностроении. Давайте разберемся, что этот параметр означает, как он контролируется и почему настолько важен для обеспечения работоспособности изделий.
Определение допуска прямолинейности
Допуск прямолинейности - это предельно допустимое отклонение реальной линии или оси поверхности детали от идеальной прямой линии в заданном направлении. Этот показатель регламентируется ГОСТ 24643-81 и определяет степень соответствия формы детали ее чертежу после обработки.
Допуск прямолинейности важен для деталей с плоскими поверхностями, а также цилиндрической и конической формы. Отклонение реальной поверхности детали от идеальной прямой приводит к нарушению ее геометрии и может вызвать отказ при эксплуатации.
Например, допуск прямолинейности оси отверстия диаметром 10 мм может составлять 0,02 мм. Это означает, что реальная ось отверстия не должна отклоняться от идеальной прямой более чем на 0,02 мм на всем протяжении. Такой допуск обеспечивает высокую точность обработки отверстия.
Виды отклонений от прямолинейности
Существуют различные виды отклонений реальной геометрии детали от идеальной прямой линии:
- Отклонение оси цилиндрической поверхности от прямой в пространстве
- Отклонение образующей конической поверхности от прямой
- Отклонение кромки детали от прямолинейности
- Отклонение оси паза или выступа от прямой
Каждый вид отклонения характеризуется своим числовым значением допуска прямолинейности в зависимости от геометрии детали и требований к точности. Например, допуск прямолинейности оси паза глубиной 5 мм на валу может составлять 0,01 мм.
Причины возникновения отклонений
Отклонения реальной геометрии детали от заданной в чертеже могут возникать по разным причинам:
- Неточная настройка и износ станка
- Деформация заготовки при обработке
- Неидеальная геометрия режущего инструмента
- Вибрации в системе станок-инструмент-деталь
- Неравномерность припуска на обработку
Например, при точении цилиндрической поверхности неточность направляющих станка может вызвать отклонение оси обработанной поверхности от прямой. Износ резца приводит к появлению неровностей на поверхности.
Чтобы свести к минимуму отклонения формы, необходим тщательный контроль геометрии станка, инструмента, припусков и режимов резания.
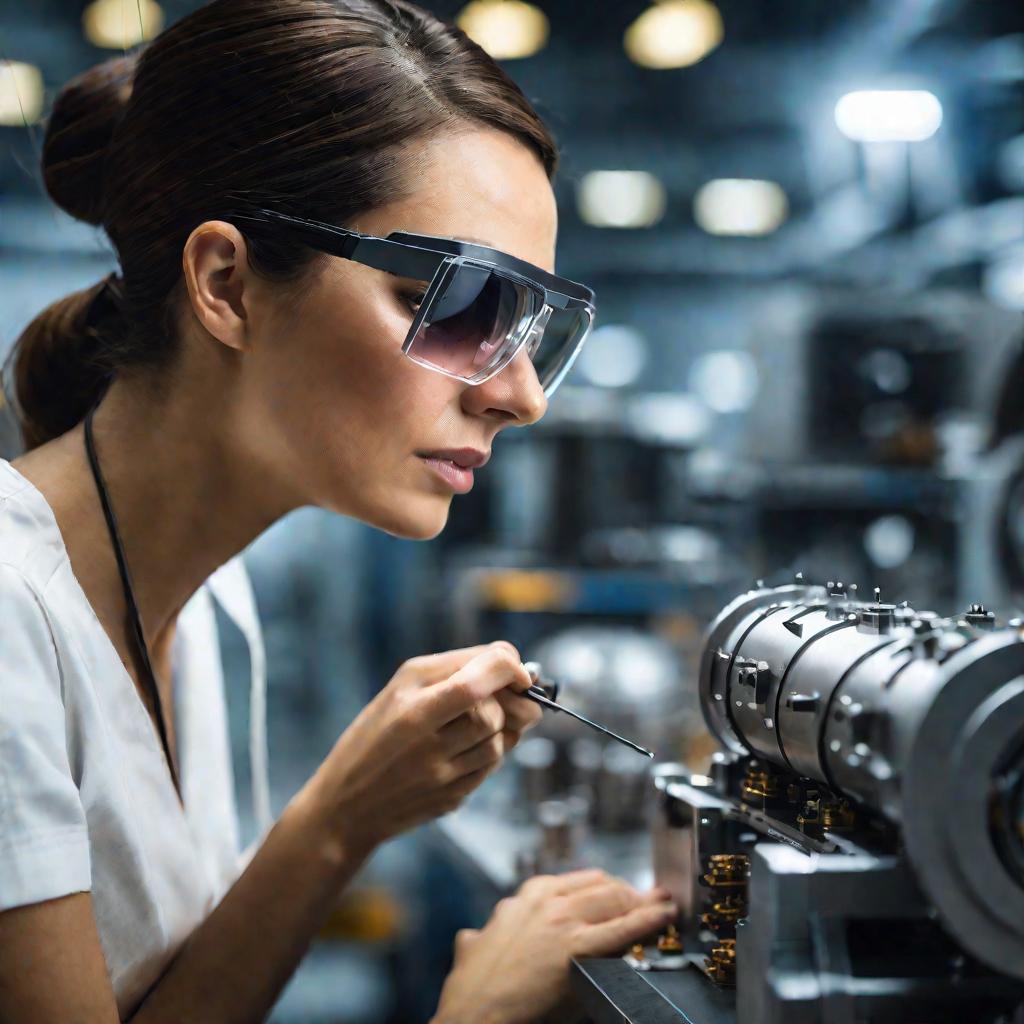
Способы контроля прямолинейности
Существуют различные способы контроля отклонений от прямолинейности:
- Визуальный контроль
- Измерение профилометрами
- Контроль на оптико-механических приборах
- Использование пневматических и гидростатических приборов
- Метод лазерной триангуляции
Наиболее простой способ - визуальная проверка прямолинейности с помощью измерения линейкой или угольником. Однако такой контроль обеспечивает недостаточную точность.
Для высокоточных измерений применяют специальные приборы - профилометры, оптико-механические установки, работающие на основе отражения светового пучка от поверхности, а также лазерные системы триангуляции.
Выбор метода контроля зависит от требуемой точности, особенностей детали и производственных условий.
Средства измерения прямолинейности
Для измерения отклонений от прямолинейности применяют следующие основные средства:
- Поверочные линейки и угольники
- Механические профилометры
- Оптические профилометры
- Лазерные измерительные системы
- Координатно-измерительные машины (КИМ)
Поверочные линейки и угольники используют для визуального контроля и обеспечивают точность порядка 0,1 мм. Механические профилометры снимают профиль поверхности с помощью щупа и имеют точность до нескольких микрон. Оптические профилометры используют отраженный от поверхности световой пучок и позволяют измерять отклонения с точностью до 0,5 мкм. Наибольшую точность обеспечивают лазерные системы и КИМы – до 0,1 мкм.
Нормы и допуски прямолинейности
Согласно ГОСТ 24643-81 устанавливается 16 степеней точности допусков прямолинейности. Чем меньше номер степени, тем выше точность:
Степень точности | Допуск прямолинейности, мкм |
1 | 0,1 |
2 | 0,2 |
... | ... |
16 | 100 |
Допуск назначают в зависимости от способа обработки: шлифование и доводка обеспечивают наибольшую точность, грубая механическая обработка - наименьшую.
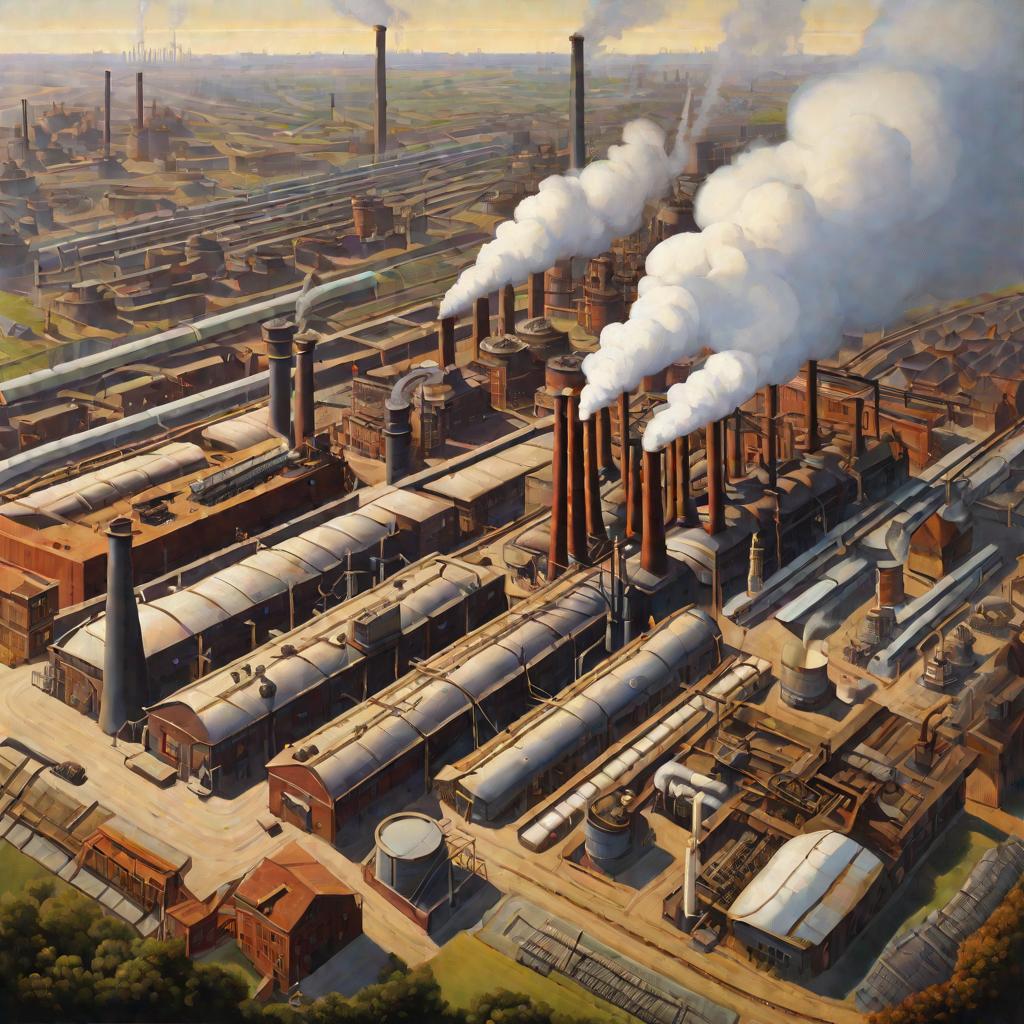
Указание допуска на чертеже
На чертеже допуск прямолинейности указывают с помощью знака в виде прямоугольника или прямой линии с отходящей от нее стрелкой. Рядом проставляют числовое значение допуска, например:
Также допуск может быть указан текстом в технических требованиях к чертежу.
Влияние прямолинейности на работу детали
Соблюдение заданного допуска прямолинейности крайне важно для обеспечения работоспособности детали:
- Обеспечивает плавность хода подвижных соединений
- Исключает вибрации и люфты
- Повышает точность позиционирования деталей
- Увеличивает срок службы и надежность изделий
Несоблюдение допуска прямолинейности, напротив, приводит к повышенному износу, шумам, неточности работы механизмов.
Пути повышения прямолинейности
Чтобы снизить отклонения от прямолинейности при обработке, можно использовать следующие методы:
- Применение высокоточного оборудования
- Тщательный контроль износа станка
- Использование качественной оснастки
- Контроль геометрии режущего инструмента
- Оптимизация режимов резания
Наибольший эффект дает применение высокоточных станков с ЧПУ, лазерной и электроэрозионной резкой. Эти методы позволяют получить прямолинейность порядка 1-5 мкм.
Контроль прямолинейности трубопроводов
Важный параметр при монтаже трубопроводов - допуск отклонения от прямолинейности. Он определяет степень соответствия оси реального трубопровода прямой линии.
Контроль прямолинейности труб выполняют с помощью геодезических измерений или лазерного сканирования. Допуск для магистральных трубопроводов обычно составляет 150-200 мм на 1 км трассы.
Прямолинейность образующей конуса
Важной характеристикой конических деталей является допуск прямолинейности образующей конуса. Этот параметр показывает степень отклонения образующей поверхности конуса от идеальной прямой.
Контроль прямолинейности образующей выполняют специальными измерительными приборами или оптическими системами. Допуск прямолинейности конической заготовки перед обработкой может достигать 0,5-1 мм на длине 300 мм.
Допуски плоскостности и прямолинейности
Допуски плоскостности и прямолинейности определяют предельные отклонения соответственно плоских и цилиндрических поверхностей деталей от идеальной геометрии.
Эти два вида допусков задаются и контролируются раздельно, поскольку характеризуют различные геометрические параметры деталей. Однако часто требования к допускам плоскостности и прямолинейности взаимосвязаны.