Сталь ХВ5, также известная как "алмазная сталь", отличается уникальным сочетанием твердости, прочности и износостойкости. Эти качества делают ее незаменимой для производства режущих инструментов, от сверл по металлу до кухонных ножей. Давайте разберемся в истории создания этой легендарной стали.
История создания и производства стали ХВ5
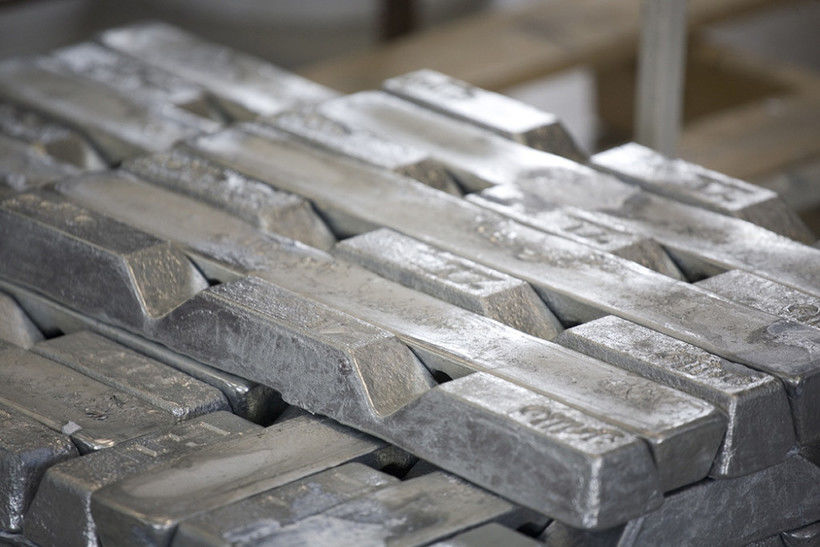
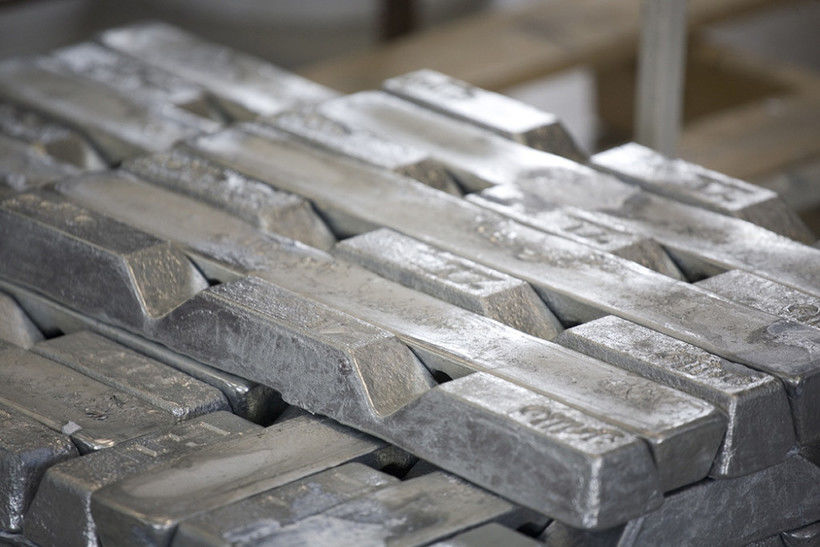
История стали ХВ5 уходит корнями в древнюю Японию. Изделия из особой стали под названием "тамахагане" (что означает "драгоценная сталь") использовались еще в Средние века для изготовления мечей самураев.
Согласно легендам, мечи из "тамахагане" обладали такой остротой, что могли разрезать падающий лист бумаги пополам.
Технология производства этой стали держалась в строгом секрете и передавалась из поколения в поколение оружейников. Выплавка "тамахагане" была очень трудоемким процессом:
- Использовались специальные одноразовые печи, которые после плавки разрушались;
- Для выплавки требовалось до нескольких десятков человек;
- Процесс длился около 3 дней при температуре 1200-1500°C.
Со временем технология производства этой стали проникла и в Европу. Первые упоминания о стали, аналогичной современной ХВ5, появились в России в 18 веке. Однако европейские металлурги так и не смогли полностью повторить уникальные свойства "тамахагане".
В наши дни производство стали ХВ5 в основном локализовано в Японии, Китае и России. Современная технология включает в себя обогащение и очистку руды, выплавку стали в индукционных или дуговых печах, раскисление, легирование, разливку в слитки и последующую прокатку или ковку заготовок.
Химический состав и структура
Ключевыми элементами, определяющими характеристики стали ХВ5, являются:
- Углерод (1,3-1,45%)
- Хром (0,9-1,2%)
- Вольфрам (4-5%)
Высокое содержание углерода обеспечивает твердость и износостойкость стали. Хром повышает прочность и коррозионную стойкость. А вольфрам делает сталь ХВ5 быстрорежущей и жаропрочной.
Помимо основных легирующих элементов, в стали ХВ5 могут присутствовать незначительные примеси никеля, меди, серы и фосфора. Их содержание строго регламентируется и не должно превышать нескольких десятых долей процента.
После закалки в стали ХВ5 формируется мелкозернистая структура, что обеспечивает высокую твердость по всему объему изделия. Ближайшими аналогами по химсоставу и структуре являются нержавеющие инструментальные стали 1.4528 (X105CrCoMo18-20) и N690.
Физико-механические свойства
Благодаря оптимальному сочетанию легирующих элементов, сталь ХВ5 демонстрирует исключительные физико-механические характеристики.
Твердость закаленной стали ХВ5 по различным шкалам составляет:
- По Роквеллу - 64-67 HRC
- По Виккерсу - 800-850 HV
- По Бринеллю - 6500-7000 МПа
Такие показатели твердости сталь хв5 характеристики отзывы твердость позволяют применять сталь ХВ5 для обработки закаленных и высокопрочных сталей, чугуна, стекла, камня и других твердых материалов.
Кроме высокой твердости, сталь ХВ5 обладает отличными прочностными характеристиками:
Предел прочности при растяжении | 1900-2100 МПа |
Предел прочности при изгибе | 2500-2900 МПа |
Однако повышенная хрупкость ограничивает использование стали ХВ5 в условиях ударных нагрузок. Поэтому изделия из нее требуют аккуратного обращения во избежание сколов и трещин.
Технология производства изделий из стали ХВ5
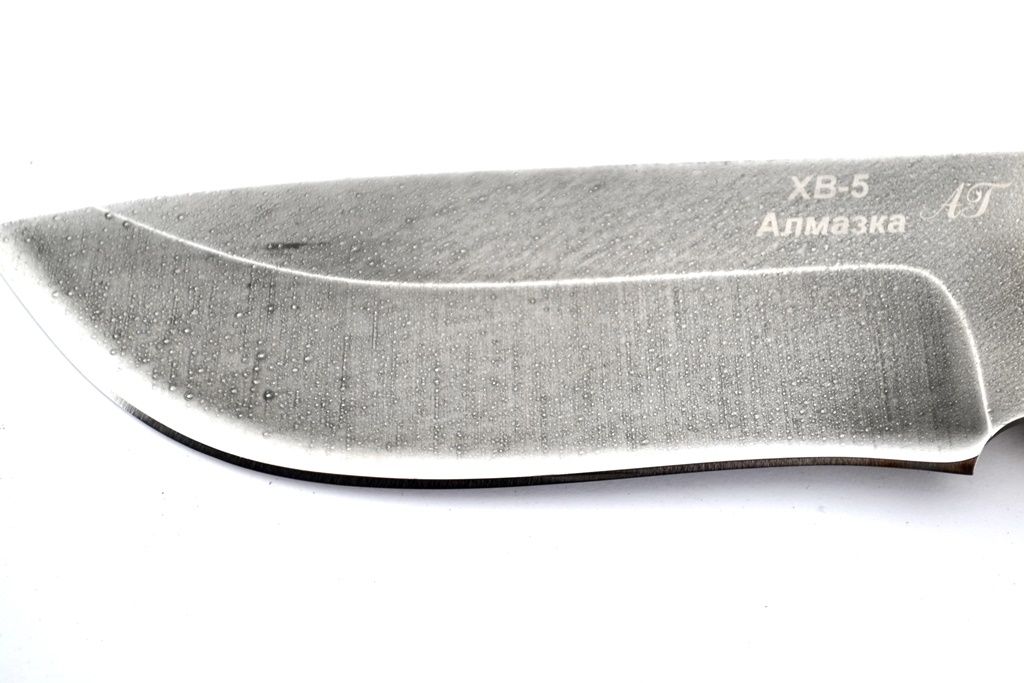
Для изготовления режущего инструмента из стали ХВ5 используются следующие основные технологические операции:
- Получение заготовок. В качестве исходных заготовок применяются прокатанные или кованые стержни, пластины, полосы из стали ХВ5. Размеры заготовок подбираются с учетом габаритов и конфигурации готовых изделий.
- Термическая обработка. Закалка стали ХВ5 производится при 1050-1080°C с последующим низкотемпературным отпуском при 150-300°C. Это позволяет получить высокую твердость по всему сечению изделия.
- Механическая обработка. После закалки изделия из стали ХВ5 подвергаются точению, фрезерованию, шлифовке для придания необходимой геометрической формы, размеров и качества поверхности.
- Термохимическая обработка. Дополнительно применяют азотирование или цементацию поверхности для повышения износостойкости и коррозионной стойкости инструмента.
- Нанесение покрытий. В ряде случаев на рабочие поверхности инструмента наносят износостойкие покрытия (нитрид титана, карбид вольфрама и т.д.) методами PVD или CVD для увеличения стойкости.
При изготовлении инструмента из стали ХВ5 важное значение имеет соблюдение оптимальных режимов всех технологических операций, поскольку материал достаточно чувствителен к перегреву и переохлаждению.