На производствах и в строительной сфере неразрушающий контроль является одним из самых популярных способов диагностики материалов. С помощью этого метода строители оценивают качество сварных соединений, проверяют плотность на отдельных участках конструкций, выявляя глубинные дефекты и изъяны. Диагностические магнитные дефектоскопы позволяют обнаруживать как поверхностные, так и подповерхностные разрушения с высокой степенью точности.
Устройство прибора
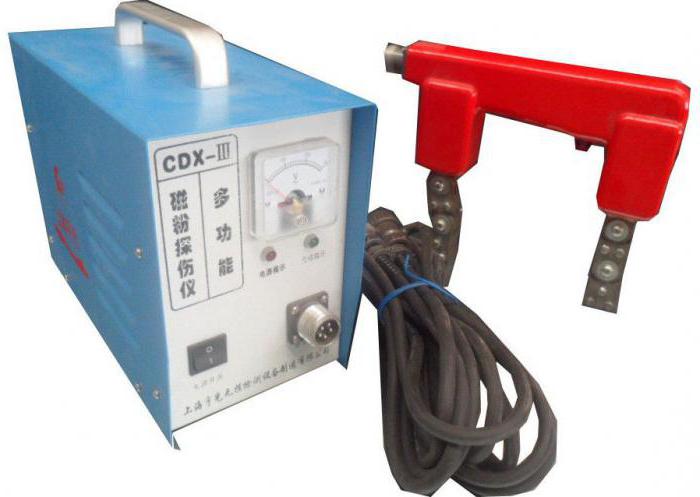
Основу сегмента магнитных толщиномеров и дефектоскопов представляют ручные аппараты, обеспеченные намагничиваемыми рабочими органами – как правило, в виде клещей. Внешне это небольшие приборы, начинку которых составляет электромагнит, регулирующий полюса волнового воздействия. Средний класс позволяет работать с магнитной проницаемостью, коэффициент которой выше 40. Корпус обеспечивается эргономичной рукояткой, благодаря которой устройство можно использовать в труднодоступных местах. Для подачи электротока приборы также обеспечиваются кабелем, подсоединяемым или к генераторной станции (если работы выполняются на улице), или к бытовой электросети на 220 В. Более сложное оборудование неразрушающего контроля имеет стационарную базу, подключенную к компьютеру. Такие средства диагностики чаще применяются для проверки качества выпускаемых деталей на производствах. Они выполняют контроль качества, фиксируя мельчайшие отклонения от нормативных показателей.
Феррозондовые дефектоскопы
Разновидность магнитных приборов, ориентированных на выявление дефектов на глубине до 10 мм. В частности, их используют для фиксации нарушений сплошности структуры конструкций и деталей. Это могут быть закаты, раковины, трещины и волосовины. Применяют феррозондовый метод и для оценки качества сварных швов. После завершения рабочего сеанса магнитные дефектоскопы такого типа могут определять и уровень размагниченности детали в рамках комплексной диагностики. В плане применения к деталям разных форм и размеров устройства практически не имеют ограничений. Но, опять же, следует не забывать о максимальной глубине анализа структуры.
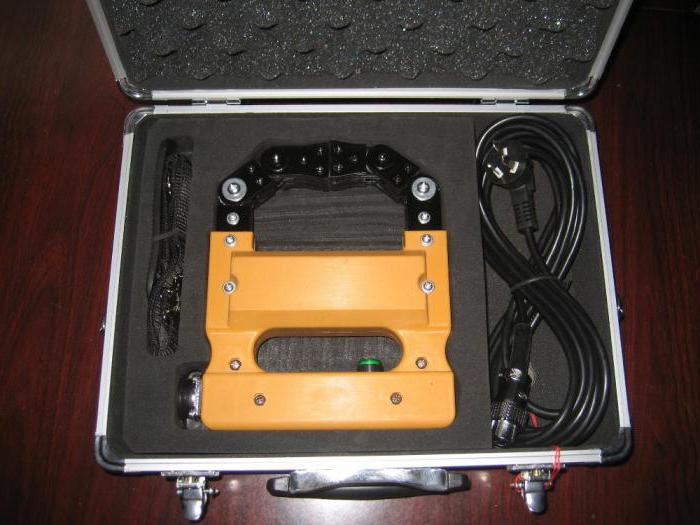
Магнитографические и вихретоковые дефектоскопы
С помощью магнитографических аппаратов оператор может обнаруживать недостатки изделий на глубине от 1 до 18 мм. И вновь целевыми признаками отклонений в структуре выступают нарушения сплошности и дефекты сварных соединений. К особенностям вихретоковой техники контроля можно отнести анализ взаимодействия электромагнитного поля с волнами, образуемыми вихревыми токами, которые подаются на предмет контроля. Чаще всего вихретоковый дефектоскоп применяется для обследования изделий, выполненных из электропроводящих материалов. Приборы такого типа показывают высокоточный результат при анализе деталей с активными электрофизическими свойствами, но важно учитывать, что они работают на небольшой глубине – не более 2 мм. Что касается характера дефектов, то вихретоковой метод позволяет выявлять несплошности и трещины.
Магнитно-порошковые дефектоскопы
Такие устройства тоже ориентируются преимущественно на поверхностные дефекты, которые можно фиксировать на глубине до 1,5-2 мм. При этом допускается возможность исследований на предмет выявления широкого спектра дефектов – от параметров сварного шва до обнаружения признаков расслоения и микротрещин. Принцип работы такого оборудования неразрушающего контроля основывается на активности частиц порошка. Под действием электротока они направляются в сторону неоднородности магнитных колебаний. Это позволяет фиксировать недостатки поверхности целевого объекта исследования.

Наибольшая точность определения дефектных зон таким методом будет присутствовать в случае, если плоскость дефектного участка формирует 90-градусный угол с направлением магнитного потока. По мере отклонения от этого угла сокращается и чувствительность прибора. В процессе работы с такими приборами используется и дополнительный инструментарий, позволяющий фиксировать параметры дефектов. Например, магнитный дефектоскоп «Магест 01» в базовой комплектации обеспечивается двукратной лупой и ультрафиолетовым фонарем. То есть непосредственное определение изъяна на поверхности выполняется оператором путем визуальной проверки.
Подготовка к работе
Подготовительные мероприятия можно разделить на две группы. В первую войдет непосредственно подготовка рабочей поверхности, а во вторую – настройка прибора. Что касается первой части, то деталь должна быть очищена от ржавчины, различного рода смазок, масляных пятен, грязи и пыли. Качественный результат можно получить только на чистой и сухой поверхности. Далее выполняется настройка дефектоскопа, в которой ключевым этапом будет калибровка с проверкой по эталонам. Последние представляют собой образцы материалов с дефектами, по которым можно оценивать корректность результатов анализа прибора. Также в зависимости от модели можно фиксировать диапазон рабочей глубины и чувствительность. Эти показатели зависят от задач по выявлению дефектов, характеристик обследуемого материала и возможностей самого аппарата. Современные высокотехнологичные дефектоскопы позволяют выполнять и автоматическую настройку по заданным параметрам.
Намагничивание детали
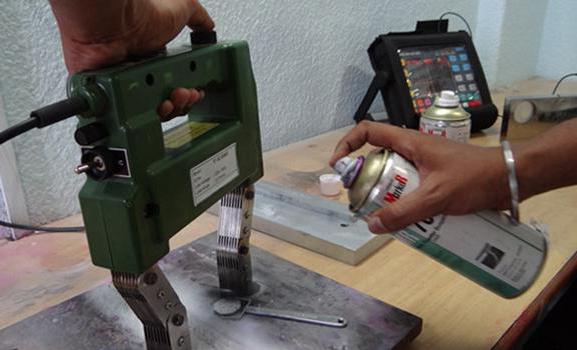
Первая стадия рабочих операций, в ходе которой выполняется намагничивание обследуемого объекта. Изначально важно правильно определить направление потока и тип намагничивания с параметрами чувствительности. К примеру, порошковый метод позволяет выполнять полюсное, циркулярное и комбинированное воздействие на деталь. В частности, циркулярное намагничивание осуществляется посредством пропускания электротока прямо по изделию, по основному проводнику, по обмотке или по отдельному участку элемента с подключением электрических контакторов. В режиме полюсного воздействия магнитные дефектоскопы обеспечивают намагничивание с применением катушек, в среде соленоида, посредством переносного электромагнита или с помощью постоянных магнитов. Соответственно, комбинированный метод позволяет сочетать два способа, подключая дополнительное оснащение в процессе намагничивания заготовки.
Нанесение магнитного индикатора

На предварительно подготовленную и намагниченную поверхность наносится индикаторный материал. Он позволяет выявлять недостатки детали под воздействием электромагнитного поля. Уже говорилось, что в этом качестве могут использоваться порошки, но некоторые модели работают также с суспензиями. В обоих случаях перед работой важно учитывать оптимальные условия для применения аппарата. К примеру, дефектоскоп магнитный «МД-6» рекомендуется использовать при температурном режиме от -40 до 50 °С и при влажности воздуха до 98%. Если условия соответствуют требованиям к эксплуатации, то можно начинать нанесение индикатора. Порошок наносят по всей зоне – так, чтобы предусматривался и небольшой охват непредназначенных для исследования зон. Это позволит получить более точную картину дефекта. Суспензия наносится струей при помощи шланга или аэрозоля. Также существуют методы погружения детали в емкость с магнитной индикаторной смесью. Далее можно переходить непосредственно к дефектовке изделия.
Осмотр детали
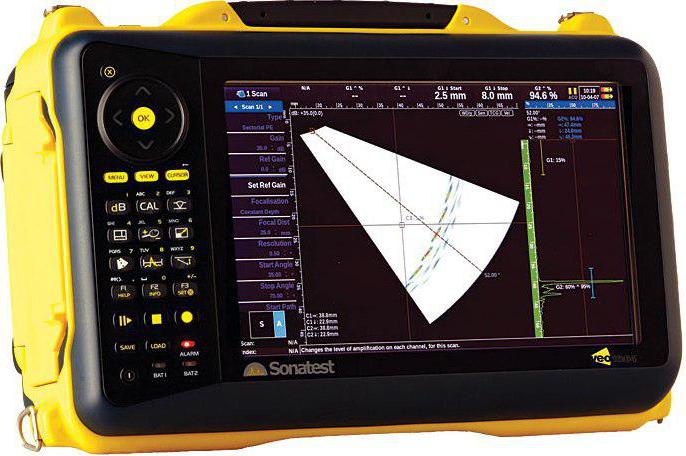
Оператор должен дождаться момента, когда завершится активность индикатора, будь то частицы порошка или суспензия. Изделие проверяется визуальным способом с вышеупомянутыми приспособлениями в виде оптических устройств. При этом увеличительная способность данных приборов не должна превышать х10. Также в зависимости от требований к обследованию оператор может сделать снимки уже для более точного компьютерного анализа. Многофункциональные магнитные дефектоскопы-станции имеют в базовом оснащении аппаратуру для расшифровки реплик с порошковыми отложениями. Полученные в ходе разбраковки рисунки в дальнейшем сверяются с нормативными образцами, что позволяет вынести заключение о качестве изделия и его допустимости к целевому применению.
Заключение
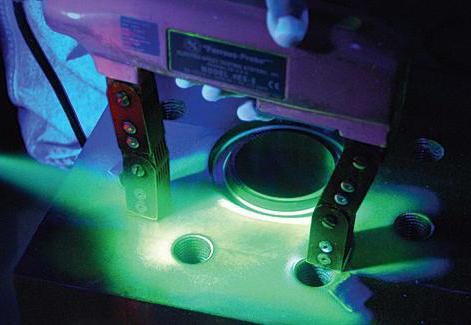
Магнитные приборы для дефектоскопии широко используются в разных областях. Но у них также есть и недостатки, ограничивающие применение. В зависимости от условий эксплуатации к ним можно отнести и требования к температурному режиму, а в некоторых случаях и недостаточную точность. В качестве универсального средства контроля специалисты рекомендуют применять многоканальный магнитный дефектоскоп, который также способен поддерживать функцию ультразвукового анализа. Количество каналов может достигать 32-х. Это значит, что аппарат сможет поддерживать оптимальные параметры дефектоскопии применительно к такому же количеству разноплановых задач. В сущности, под каналами понимается количество режимов работы, ориентированных на определенные характеристики целевого материала и условия окружающей среды. Такие модели стоят недешево, но зато обеспечивают корректность результатов при выявлении дефектов поверхности и внутренней структуры разного рода.