Подшипниковые узлы играют важнейшую роль в работе любого вращающегося оборудования. Они обеспечивают плавное и бесшумное вращение валов, роторов и других деталей машин и механизмов. От надежности и долговечности подшипниковых узлов напрямую зависит безаварийная работа всего оборудования.
В этой статье мы подробно рассмотрим устройство и принцип действия различных типов подшипниковых узлов, особенности их конструкции и монтажа, а также способы обеспечения длительного срока службы.
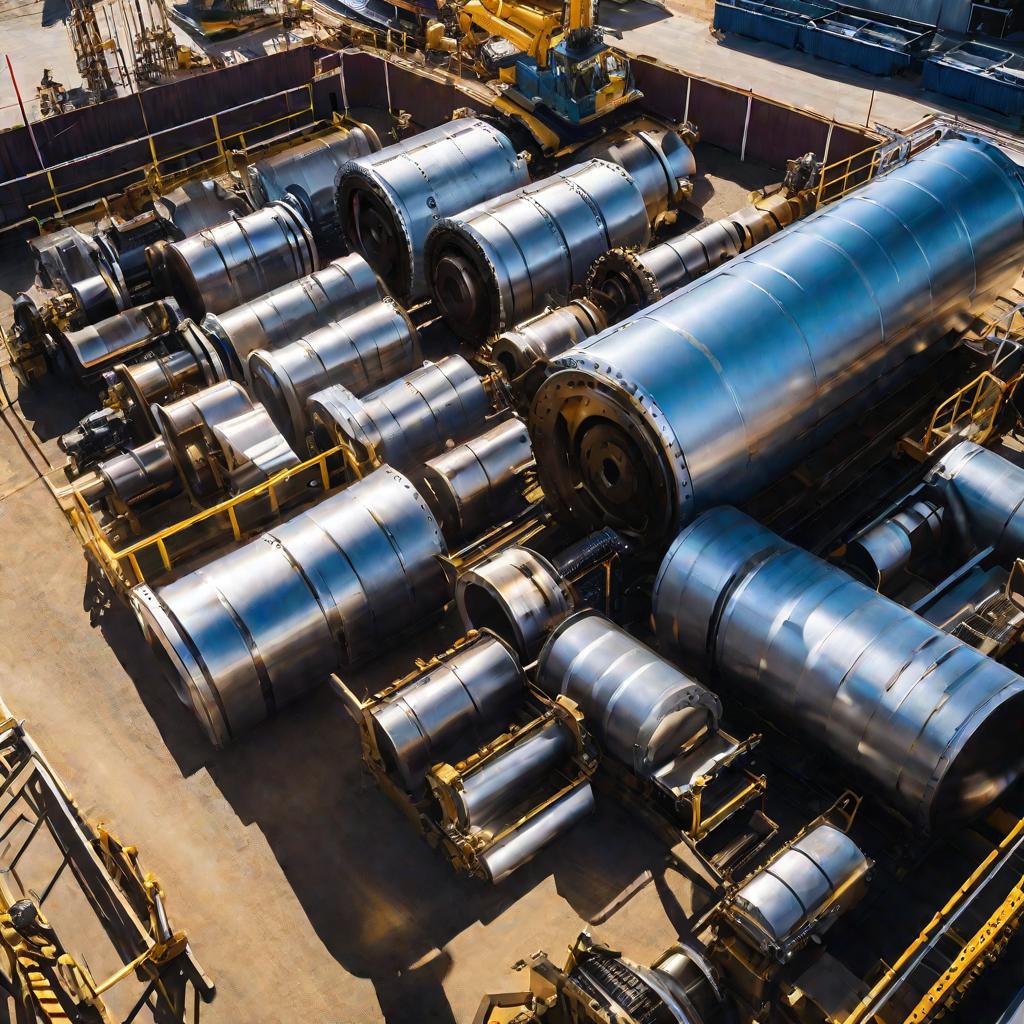
Назначение и классификация
Подшипниковые узлы предназначены для обеспечения вращательного или поступательного движения между частями машин и механизмов с минимальным трением. Они воспринимают радиальные и осевые нагрузки, возникающие при работе оборудования.
По конструкции подшипники подразделяют на две основные группы:
- Скольжения (например, вкладыши)
- Качения (шариковые, роликовые)
По способу размещения подшипников относительно вала выделяют:
- Радиальные
- Упорные
- Радиально-упорные
По типу крепления к корпусу различают подшипники:
- Фланцевые
- Посадочные
- Плавающие
Устройство и принцип работы
Подшипниковый узел состоит из двух колец – наружного и внутреннего. Между ними располагаются тела качения (шарики или ролики), которые свободно перекатываются при вращении колец.
Благодаря этому вращение вала или оси происходит практически без трения. Нагрузка распределяется по большому количеству точек контакта между телами качения и кольцами.
В подшипниках скольжения в качестве тел качения используются сегменты вкладышей из антифрикционных материалов. Они плотно прилегают к поверхностям вращающихся и неподвижных колец.
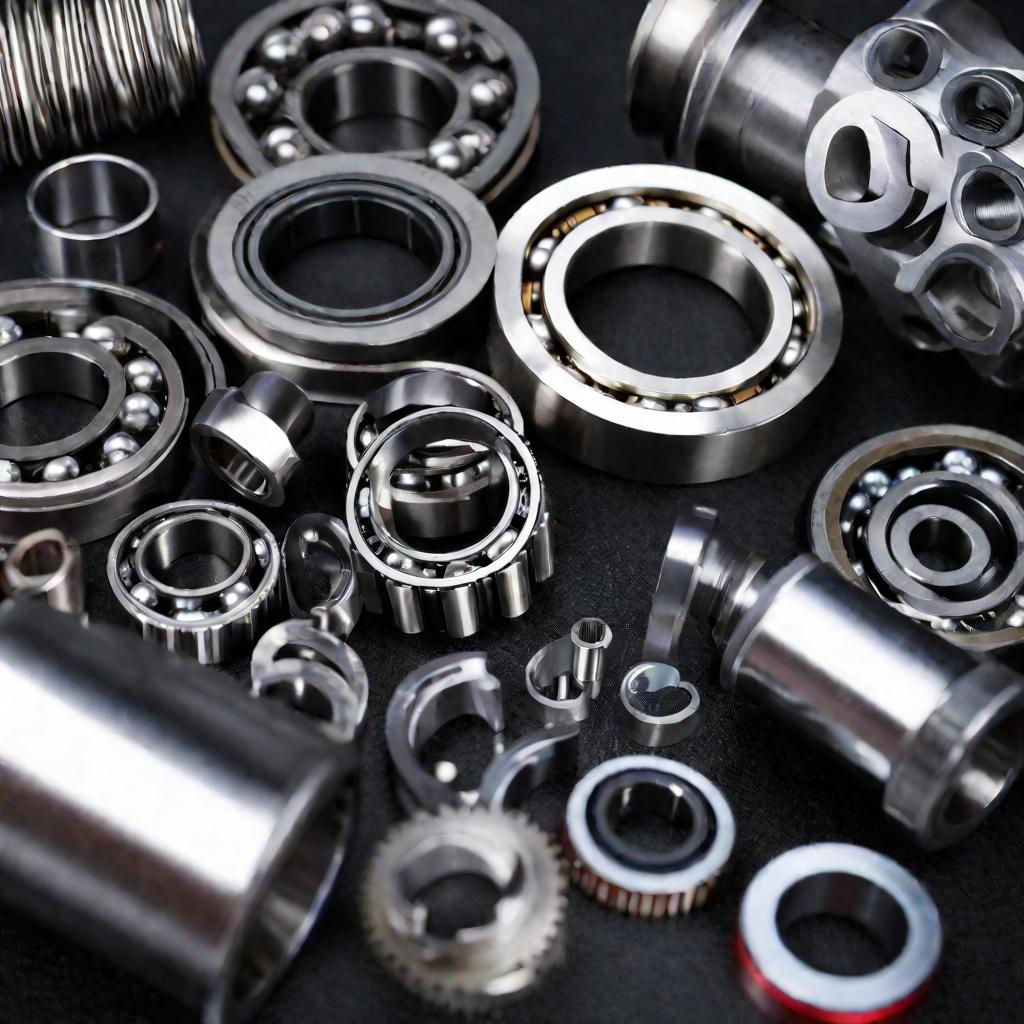
Конструкция и материалы
Конструкция подшипниковых узлов определяется условиями их работы. Для высокоскоростных валов применяют шариковые подшипники, обладающие меньшим трением. При больших нагрузках используют роликовые, способные воспринимать значительные осевые усилия.
Для агрессивных сред часто применяют подшипники со специальными защитными покрытиями. Для работы в условиях недостаточной смазки подходят подшипники с увеличенным зазором.
Материал колец и тел качения также подбирается в зависимости от условий эксплуатации. Наиболее распространены подшипниковые стали, но для особо ответственных узлов используются керамика, композиты, драгметаллы.
Монтаж подшипниковых узлов
Правильный монтаж подшипников имеет большое значение для обеспечения их долговечности и надежной работы узла.
Перед установкой подшипники тщательно очищают от консервирующей смазки и проверяют на отсутствие дефектов. Посадочные поверхности также должны быть чистыми.
Подшипники устанавливают с натягом, обеспечивающим плотную посадку без перекосов. Используют специальные инструменты и оправки, не допускающие повреждения колец.
После монтажа проводят контроль биения вала и зазоров в подшипнике. Превышение допустимых значений может привести к преждевременному выходу узла из строя.
Обеспечение долговечности
Срок службы подшипников во многом зависит от правильной смазки и регламентного обслуживания. Рекомендуется использовать высококачественные смазочные материалы в строгом соответствии с инструкцией.
Необходимо регулярно контролировать температуру подшипников, вибрацию, уровень шума. Повышение этих параметров может сигнализировать о неисправностях.
Своевременная замена изношенных подшипников, профилактический осмотр и ремонт узлов позволяют максимально продлить срок службы оборудования.
Таким образом, от качества и правильной эксплуатации подшипниковых узлов напрямую зависит надежность и долговечность всего оборудования. Их регулярное обслуживание является обязательным условием безаварийной работы любых механизмов.
Типы подшипниковых узлов
Существует большое разнообразие типов и конструкций подшипниковых узлов, предназначенных для различных условий эксплуатации.
Одним из распространенных является двухопорный подшипниковый узел. В нем устанавливаются два подшипника по краям вала, что позволяет воспринимать как радиальные, так и осевые нагрузки.
Для крепления подшипников к корпусу оборудования часто используется корпусной подшипниковый узел. Он имеет приварной или отлитый к корпусу фланец, в котором размещается подшипник.
Выбор подшипников для конкретных условий
При выборе подшипников для конкретного механизма необходимо учитывать множество факторов:
- Тип и величина нагрузок;
- Частота и скорость вращения;
- Температурный режим;
- Наличие ударов и вибраций.
Кроме того, важно рассчитать требуемый ресурс подшипников в заданных условиях эксплуатации. Эти расчеты позволяют обеспечить надежную работу оборудования в течение всего срока службы.
Правильный подбор подшипников по типоразмеру, конструктивному исполнению и материалу колец является важной инженерной задачей.
Проектирование подшипниковых узлов
При проектировании подшипниковых узлов важно правильно определить их конструкцию и параметры в соответствии с условиями работы механизма.
Необходимо выполнить прочностные расчеты деталей узла, определить допустимые нагрузки, подобрать материалы с учетом надежности и долговечности.
При разработке конструкции нужно предусмотреть решения по смазке подшипников, защите от пыли и влаги, отводу тепла, удобству монтажа и обслуживания.
Оптимизация подшипниковых узлов
При модернизации оборудования подшипниковые узлы часто подвергаются оптимизации для повышения надежности и снижения затрат.
Возможные направления оптимизации:
- Замена серийных подшипников на более долговечные;
- Использование уплотнений увеличенного ресурса;
- Установка датчиков контроля температуры и вибрации;
- Внедрение более эффективных систем смазки.
Такая модернизация позволяет существенно снизить затраты на ремонт и простои оборудования.