Центровочные отверстия играют важную, но часто недооцененную роль в обработке деталей. Их правильный выбор позволяет значительно повысить точность обработки, снизить процент брака и ресурсозатраты. Однако на практике конструкторы и технологи не всегда уделяют должное внимание проектированию центровочных отверстий. В этой статье мы подробно разберем, какие бывают центровочные отверстия, как правильно их выбирать исходя из задач обработки и особенностей детали, и как их грамотный выбор влияет на экономическую эффективность производства.
1. Назначение центровочных отверстий
Центровочные отверстия предназначены для базирования и закрепления заготовок при их механической обработке. Они позволяют точно и надежно устанавливать деталь относительно инструмента, обеспечивая высокую точность обработки.
Центровочные отверстия наиболее часто применяются при токарной и шлифовальной обработке валов, втулок, дисков и других тел вращения. Заготовку устанавливают между центрами станка, один из которых располагается в шпинделе, а другой - в задней бабке. Конические рабочие поверхности центров входят в соответствующие конические отверстия заготовки, обеспечивая надежную фиксацию и высокую точность вращения.
Качество обработанной поверхности напрямую зависит от точности базирования заготовки, то есть от точности изготовления и расположения центровочных отверстий. Поэтому выбор параметров центровочных отверстий является важной технологической задачей.
2. Типы центровочных отверстий
Согласно ГОСТ 14034-74, существует несколько стандартных типов центровочных отверстий:
- Тип А - отверстие с конусом 60° без цилиндрической части;
- Тип В - отверстие с конусом 60° и цилиндрической частью;
- Тип С - отверстие с конусом 75° без цилиндрической части;
- Тип R - отверстие с дугообразным профилем;
- Тип F - отверстие с конусом 60° или 75° и резьбой.
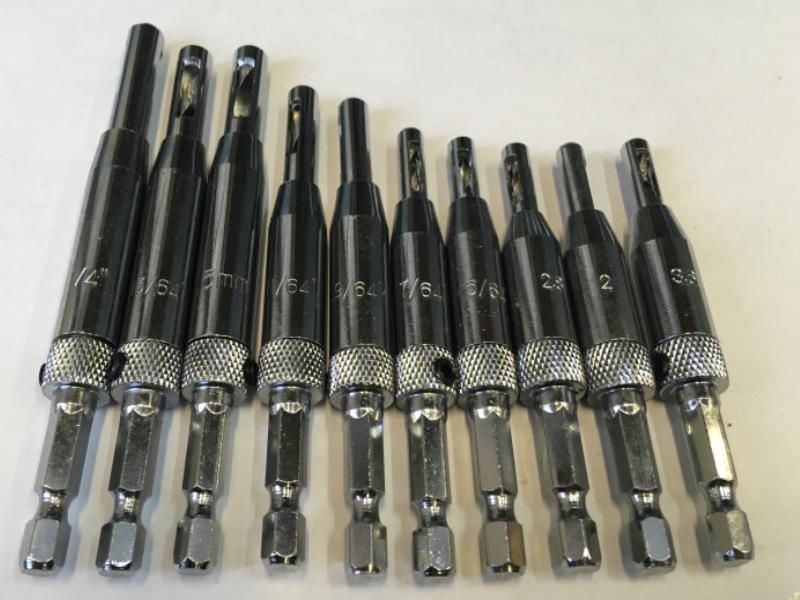
Конструктивные особенности разных типов центровочных отверстий определяют области их применения:
- Тип А используется в простых случаях, когда нет повышенных требований к сохранности отверстий;
- Тип В обеспечивает лучшую защиту центрирующего конуса и применяется при необходимости многократного использования;
- Тип R обеспечивает повышенную точность центрирования за счет дугообразного профиля;
- Тип F используется в сложных конструкциях, где требуется дополнительное крепление.
Правильный выбор типа центровочного отверстия позволяет оптимизировать конструкцию и технологию обработки детали.
3. Основные размеры и допуски
Стандарт ГОСТ 14034-74 регламентирует диаметры центровочных отверстий в зависимости от их типа. Например, для отверстий типа В диаметры составляют:
1 мм | 2 мм | 2,5 мм | 3 мм | 4 мм |
5 мм | 6,3 мм | 8 мм | 10 мм | 12 мм |
16 мм | 20 мм | 25 мм | 32 мм | 40 мм |
Конкретный диаметр выбирают исходя из диаметра обрабатываемой детали. Для отверстий типа F диаметр зависит от параметров резьбы.
ГОСТ допускает определенные отклонения на размер и угол конуса центровочного отверстия. Например, для угла 60° допуск составляет минус 30'. Шероховатость центрирующей поверхности регламентирована в пределах Ra 2,5 мкм.
Точное соблюдение допусков имеет принципиальное значение для обеспечения базирования с высокой точностью.
4. Технология обработки центровочных отверстий
Обработку центровочных отверстий производят на токарных или специальных центровальных станках с использованием комбинированных центровочных сверл.
Режимы резания при центровании:
- скорость резания v = 12-25 м/мин;
- подача S = 0,02-0,06 мм/об;
- охлаждение - эмульсия.
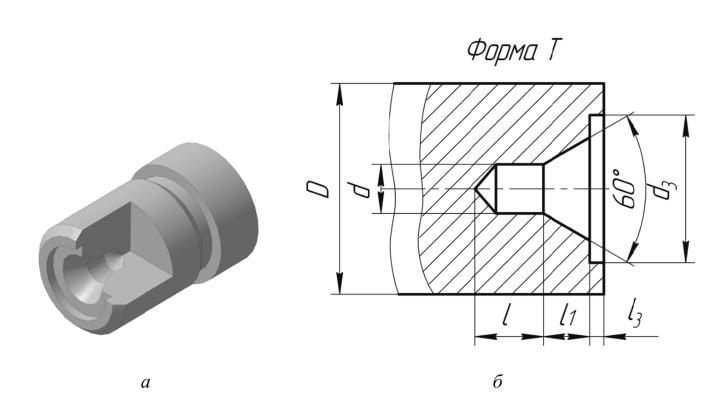
При центровании возможны такие дефекты, как несоосность отверстий, отклонение от заданного угла конуса, превышение шероховатости. Их можно предотвратить использованием высокоточных станков и режущего инструмента, тщательной настройкой оборудования.
Контроль качества центровочных отверстий осуществляют специальными калибрами-пробками, которые имитируют размеры и форму центров станка.
Соблюдение оптимального техпроцесса обработки крайне важно для получения требуемых параметров центровочных отверстий.
5. Центровочные отверстия в конструкции деталей
Конструктивное исполнение центровочных отверстий должно обеспечивать удобство базирования заготовки и сохранность отверстий в процессе эксплуатации изделия.
На пустотелых деталях центровочные поверхности часто выполняются в виде конических фасок с углом 60°, располагаемых в торцах отверстий. Такие фаски должны иметь достаточную длину для размещения центров (см. ГОСТ 14034-74
).
При наличии пазов, шлицев и других прерывистых поверхностей на торце, центровую фаску следует выполнять на максимально возможном расстоянии от них, чтобы исключить повреждение.
Если центровочные отверстия конструктивно недопустимы, это должно быть указано на чертеже. Например: "Центровые отверстия не допускаются".
Грамотный учет особенностей центровочных отверстий на этапе конструирования позволяет оптимизировать технологичность детали.
Таким образом, в первой части статьи мы рассмотрели назначение центровочных отверстий, их основные типы, параметры и особенности изготовления. В следующей части перейдем к практическим рекомендациям по выбору центровочных отверстий.
6. Выбор центровочных отверстий по массе детали
При выборе центровочных отверстий одним из определяющих параметров является масса обрабатываемой детали. Чем больше масса, тем, как правило, требуется больший диаметр отверстия.
В приложении к ГОСТ 14034-74 приведены рекомендуемые данные для выбора диаметра центровых отверстий в зависимости от массы детали:
- До 50 кг - диаметр 2 мм;
- До 80 кг - диаметр 2,5 мм;
- До 100 кг - диаметр 3,15 мм;
- До 200 кг - диаметр 4 мм;
- До 500 кг - диаметр 5 мм;
- До 1500 кг - диаметр 8 мм;
- До 8000 кг - диаметр 16 мм;
- До 20000 кг - диаметр 20 мм.
Для тяжелых деталей свыше 20000 кг диаметр центровых отверстий может доходить до 25-40 мм.
При выборе диаметра необходимо учитывать не только массу, но и габариты, жесткость детали, особенности ее базирования. Например, для длинных валов требуются отверстия большего диаметра.
7. Технологичность конструкции с центровочными отверстиями
Наличие центровочных отверстий влияет на технологичность детали. С одной стороны, это дает большую гибкость в выборе методов обработки. С другой стороны, требует дополнительных операций и может увеличивать металлоемкость.
Чтобы повысить технологичность, рекомендуется:
- Минимизировать количество центровочных отверстий;
- Выбирать оптимальные размеры отверстий;
- Рационально размещать отверстия на детали.
После окончания обработки центровые отверстия можно ликвидировать отрезкой торцов или запрессовкой втулок. Однако это требует дополнительных операций.
8. Экономическая эффективность оптимальных решений
Грамотный подход к проектированию центровочных отверстий может дать значительный экономический эффект за счет:
- Снижения трудоемкости обработки;
- Сокращения времени на переналадки;
- Уменьшения брака;
- Экономии материала.
Например, правильный выбор типа и размера центровочных отверстий позволяет сократить время установки заготовки в 2-3 раза. Это дает экономию до 15% общего времени обработки партии деталей.
Оптимальное размещение центровочных отверстий уменьшает металлоемкость детали на 5-7%. А грамотная конструкция центровочных фасок экономит до 10% материала по сравнению с неправильными решениями.
Таким образом, комплексный подход к проектированию центровочных отверстий оказывает значительное влияние на экономическую эффективность производства деталей.
9. Рекомендации по выбору центровочных отверстий
Исходя из рассмотренных факторов, можно дать следующие общие рекомендации по выбору центровочных отверстий:
- Анализировать назначение детали и условия ее эксплуатации;
- Определить требования к точности обработки поверхностей;
- Выбрать тип отверстия, исходя из особенностей обработки и конструкции;
- Ориентировать размер отверстия по диаметру и длине детали;
- Проработать оптимальное конструктивное исполнение и размещение отверстий;
- Проанализировать технологичность принятых решений.
Главным критерием оптимальности должна быть экономическая эффективность с учетом требований надежности и качества деталей.