Поверхностная закалка стали - один из важнейших этапов обработки металлических изделий. От качества закалки зависят прочность, износостойкость и срок службы деталей. В статье мы рассмотрим основные виды, методы и тонкости профессиональной поверхностной закалки стали. Узнайте, как добиться идеальной твердости поверхности при сохранении пластичности сердцевины, избежать растрескивания и деформации. Получите ценные советы от опытных технологов.
Поверхностная закалка стали: общие сведения
Поверхностная закалка стали представляет собой процесс упрочнения только поверхностного слоя детали при сохранении прочности и вязкости сердцевины. В отличие от объемной закалки, при которой прогревается вся деталь, поверхностная закалка позволяет существенно сэкономить время и энергозатраты за счет локального термического воздействия.
Основные цели поверхностной закалки:
- Повышение износостойкости рабочих поверхностей деталей
- Улучшение устойчивости к усталостным нагрузкам
- Повышение коррозионной стойкости
Поверхностную закалку широко используют при производстве:
- Деталей машин, подвергающихся абразивному изнашиванию: зубчатые колеса, червяки, валы
- Режущего инструмента: фрезы, сверла, ножи
- Штампов и пресс-форм
- Подшипников качения и скольжения
Физико-химической основой закалки стали является быстрое охлаждение нагретого до определенной температуры металла с целью "заморозить" в нем созданную структуру. При нагреве до температуры Ac3 происходит превращение феррито-цементитной смеси в аустенит. При последующем быстром охлаждении аустенит превращается в мартенсит - твердый пересыщенный твердый раствор углерода в α-железе.
Основные критерии качества поверхностной закалки:
- Глубина закаленного слоя (0,2-2 мм)
- Твердость поверхности (50-65 HRC)
- Отсутствие трещин и деформаций
- Минимальные остаточные напряжения
Типичными дефектами при закалке являются трещины, коробление деталей и непровары. Чтобы их избежать, нужно тщательно подбирать режимы нагрева и охлаждения, а также проводить предварительную термообработку.
Наиболее часто поверхностной закалке подвергают следующие марки сталей:
- 40Х, 40ХН - конструкционные легированные стали
- 50ХФА, 50ХГФА - шарикоподшипниковые стали
- Р18, Р6М5 - инструментальные стали
- Х12МФ, Х12ВМФ - штамповые стали
- 95Х18, 110Г13Л - нержавеющие стали
Поверхностная закалка стали: индукционный метод
Одним из наиболее распространенных методов поверхностной закалки стали является индукционный нагрев токами высокой частоты. Его сущность заключается в использовании явления электромагнитной индукции.
Когда через индуктор, представляющий собой медную катушку, пропускают переменный ток высокой частоты, вокруг него возникает переменное магнитное поле. При помещении стальной заготовки в это поле в ней наводятся вихревые токи, под действием которых происходит быстрый нагрев поверхностного слоя.
Достоинствами индукционной закалки являются:
- Высокая производительность процесса
- Хорошая воспроизводимость результатов
- Возможность автоматизации
К недостаткам можно отнести ограничения по толщине и геометрии заготовок.
Индукционная закалка широко используется для упрочнения таких деталей, как зубчатые колеса, шлицы валов, резьбовые поверхности.
Оптимальные режимы закалки подбираются экспериментально для каждой марки стали. Например, для стали 40Х рекомендуются следующие параметры:
- Температура нагрева: 850-950°C
- Частота тока: 440 кГц
- Время выдержки: 2-5 сек
- Скорость охлаждения: не менее 500°C/с
Для заготовки вала диаметром 50 мм из стали 40ХН при индукционной закалке можно получить твердость поверхности 56-58 HRC на глубину 1,2-1,4 мм.
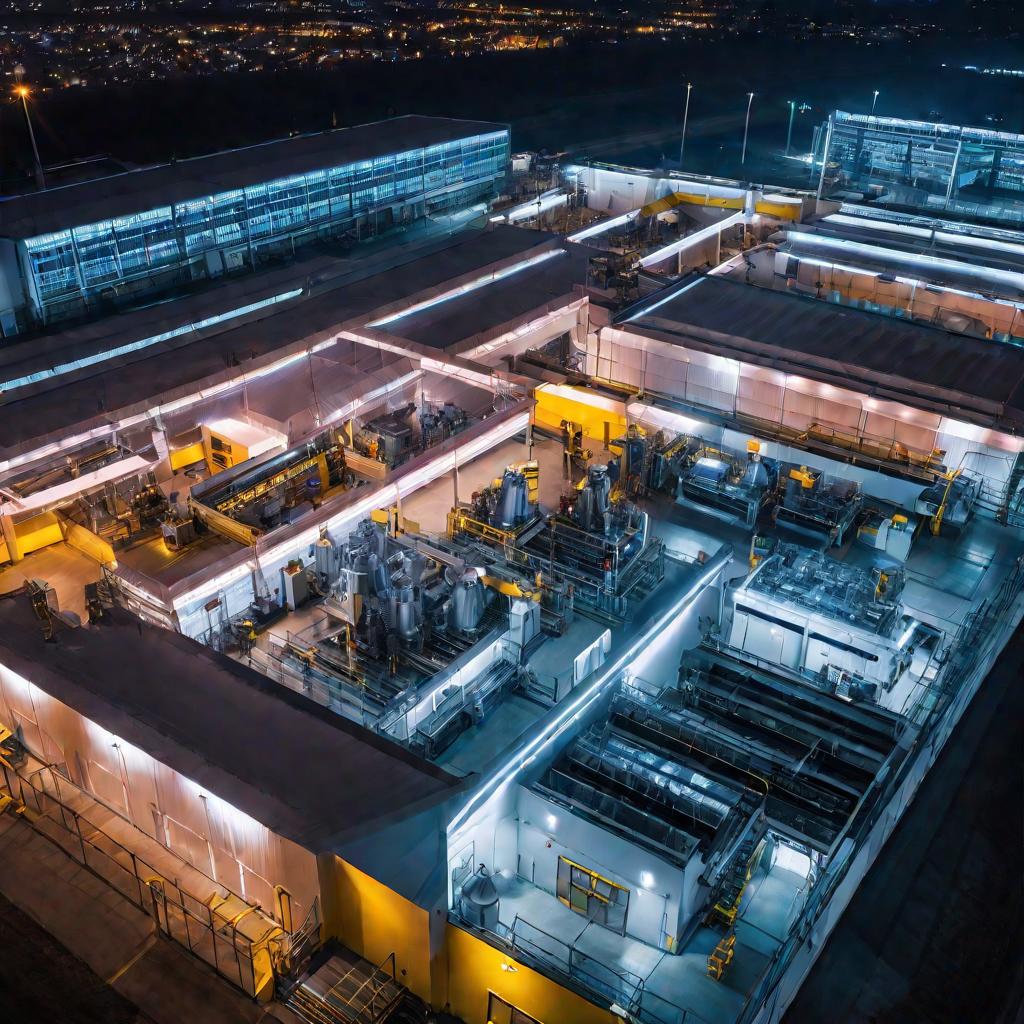
Лазерная закалка стали
Лазерная закалка основана на локальном нагреве поверхности заготовки сфокусированным лазерным лучом и последующем быстром охлаждении.
Преимущества лазерной закалки:
- Высокая концентрация энергии, позволяющая быстро нагревать малые участки
- Глубина закалки до 1-2 мм
- Возможность обработки труднодоступных участков
К недостаткам относят высокую стоимость оборудования и необходимость тщательной подготовки поверхности.
Лазерную закалку применяют для упрочнения режущего инструмента, лопаток турбин, элементов протезов.
Чтобы получить высокую твердость и износостойкость, режимы лазерной закалки подбирают для каждой марки стали индивидуально. К примеру, для быстрорежущей стали Р6М5 оптимальная плотность мощности составляет 104 Вт/см2, а скорость сканирования - 0,2 м/с.
Таким образом, лазерная закалка - эффективный метод упрочнения, позволяющий получать высокую твердость поверхности при минимальном термическом воздействии на деталь.
Электролитическая закалка стали
Электролитическая закалка основана на нагреве стальной детали при пропускании через нее электрического тока в электролите. В качестве электролита чаще всего используют водные растворы карбоната натрия, хлористого натрия или едкого натра.
При пропускании тока на поверхности детали образуется парогазовая оболочка, которая разогревается до высокой температуры и нагревает поверхностный слой. Закалка происходит либо в том же электролите, либо в другой охлаждающей среде.
Преимущества электролитической закалки:
- Возможность автоматизации процесса
- Экологичность
- Низкая стоимость
К недостаткам относят нестабильность процесса и возможность образования трещин.
Электролитическую закалку используют для небольших партий деталей из углеродистых и низколегированных сталей.
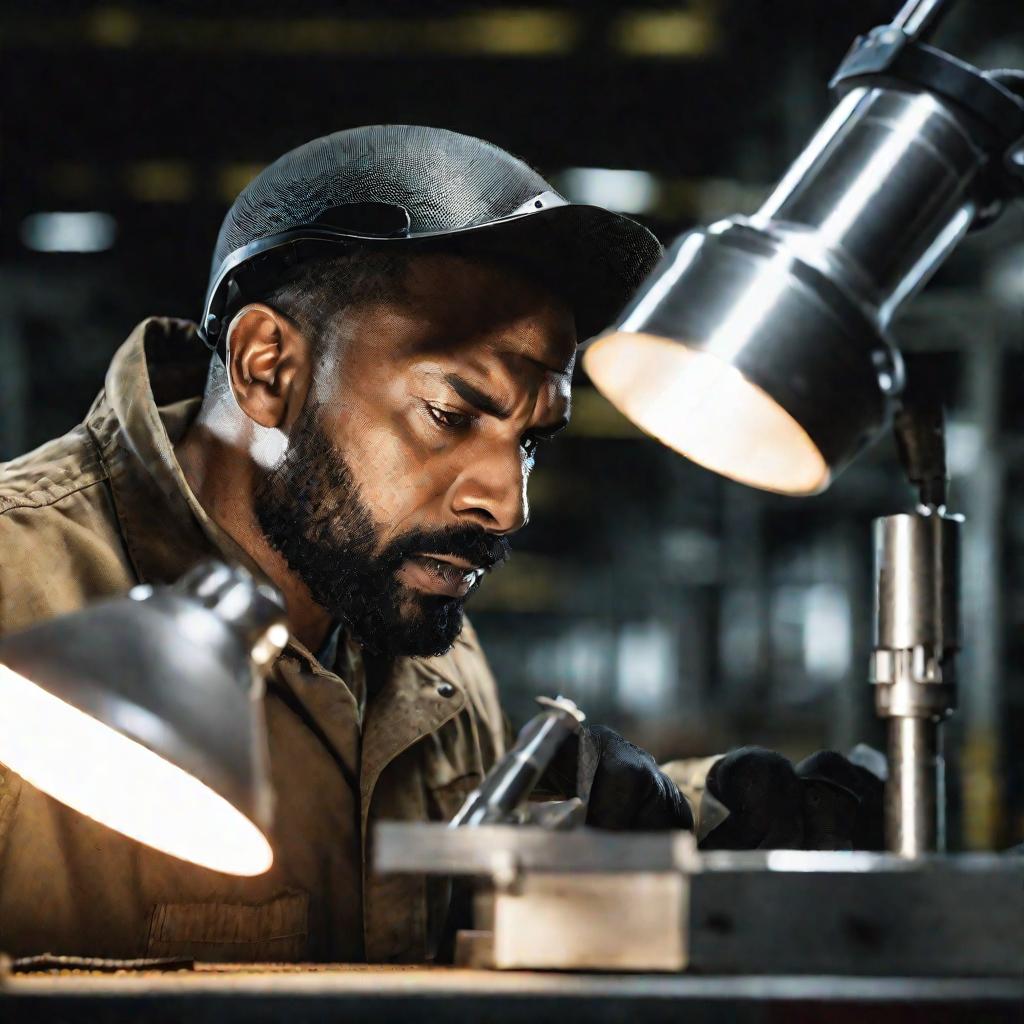
Закалка нагретым инструментом
Закалка нагретым инструментом заключается в кратковременном контакте нагретой металлической поверхности с закаливаемой деталью. Инструмент нагревают до температуры выше Ас3 обрабатываемой стали.
Преимущества этого метода:
- Простота осуществления
- Возможность локального упрочнения
- Отсутствие деформации детали
К недостаткам относят низкую производительность и нестабильность результатов.
Закалку нагретым инструментом применяют для упрочнения небольших поверхностей трения, например торцевых поверхностей зубчатых колес.
Выбор способа поверхностной закалки стали
При выборе оптимального способа поверхностной закалки нужно учитывать:
- Требуемую производительность процесса
- Тип и размеры детали
- Требования к качеству закаленной поверхности
- Стоимость необходимого оборудования
- Квалификацию персонала
Для массового производства мелких и средних деталей наиболее подходит индукционная или лазерная закалка. Для единичных крупногабаритных деталей - закалка нагретым инструментом. Электролитическая закалка применима для небольших партий простых деталей.
Комплексный подход к выбору способа упрочнения позволяет оптимизировать технологический процесс и получить максимальный экономический эффект.
Контроль качества поверхностной закалки
Чтобы оценить качество поверхностной закалки, проводят измерение микротвердости по глубине закаленного слоя на специальных приборах. Строят профиль твердости - график зависимости микротвердости от расстояния до поверхности.
Также контролируют:
- Глубину закаленного слоя
- Поверхностную твердость
- Наличие трещин и деформаций
Для выявления дефектов используют методы капиллярной и магнитопорошковой дефектоскопии, травление реактивами.
При необходимости проводят корректировку режимов нагрева и охлаждения.