Коллектор является одним из важнейших узлов электродвигателя постоянного тока. От его исправности напрямую зависит работоспособность всего двигателя. С течением времени коллектор подвергается естественному износу, что приводит к ухудшению его характеристик и в конечном итоге к отказу двигателя.
В этой статье мы подробно рассмотрим устройство коллектора, причины его износа и типичные неисправности. А также дадим рекомендации по ремонту и профилактическому обслуживанию коллектора для продления срока службы электродвигателя.
Устройство коллектора
Коллекторный узел является важной частью коллекторного двигателя. Он представляет собой цилиндрическую конструкцию, состоящую из отдельных медных пластин, разделенных изоляционным материалом (слюдой или текстолитом). Каждая пластина электрически изолирована от вала двигателя и соединена с обмоткой ротора. При вращении ротора происходит поочередное подключение обмоток к щеткам, прижимающимся к пластинам коллектора. Таким образом осуществляется электропитание обмотки и вращение ротора.
Основное назначение коллектора - коммутация, т.е. переключение обмоток якоря (ротора). Благодаря коллектору обмотки ротора периодически включаются и выключаются из цепи электропитания в нужной последовательности, обеспечивая вращение ротора электродвигателя.
Коллекторный узел является наиболее нагруженным элементом двигателя. Он испытывает значительные механические и тепловые нагрузки, а также воздействие электрической дуги между щетками и коллектором. Поэтому коллектор чаще всего выходит из строя и требует замены или ремонта.
- Изолированные друг от друга медные пластины (ламели)
- Слюда или текстолит в качестве изолятора между пластинами
- Щетки, прижимаемые к поверхности пластин и передающие на них электропитание от обмоток статора
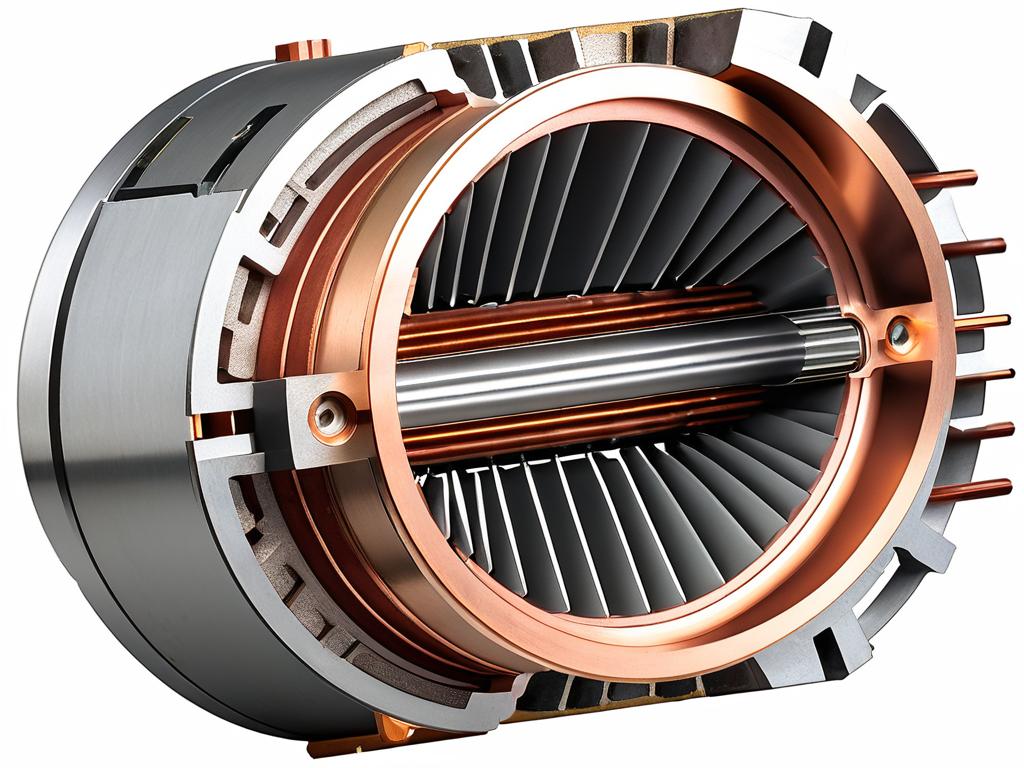
Причины износа коллектора
Коллекторный узел в процессе работы подвергается интенсивному износу. Это связано с его конструкцией и условиями эксплуатации. Рассмотрим основные причины, вызывающие преждевременный износ коллектора двигателя.
Механический износ
Постоянное трение щеток о поверхность коллектора приводит к механическому износу его пластин. Со временем это вызывает неравномерность поверхности, появление канавок, задиров. Усиливается искрение на коллекторе, растет переходное сопротивление в местах контакта щеток с ламелями. В итоге снижается КПД и мощность двигателя.
Электрическая эрозия
Прохождение электрического тока через контакт щетка-коллектор сопровождается искрением. Это приводит к электрической эрозии – разрушению поверхности ламелей под действием электрических разрядов. Со временем на коллекторе образуются кратеры, язвы, канавки. Эрозия усиливается при повышенных токах, напряжениях, нагреве коллектора.
Термическое воздействие
Нагрев коллектора и ламелей при работе двигателя также способствует ускоренному износу. При температуре свыше 80°C происходит интенсивное окисление меди, разрушается поверхность коллектора. Кроме того, перегрев ведет к повреждению изоляции между пластинами, появлению токов утечки и искрению.
Загрязнение и увлажнение
Попадание в зону коллектора абразивной пыли, стружки и других загрязнений способствует ускоренному механическому износу ламелей при трении о щетки. Увлажнение коллектора вызывает утечки тока между соседними пластинами, искрение, эрозию поверхности.
Неправильная регулировка щеточного узла
Несоблюдение оптимального давления щеток на коллектор, неправильный выбор материала щеток, отклонение оси щеткодержателя от нормы также ведут к преждевременному износу коллектора и снижению ресурса двигателя.
Таким образом, основными причинами износа коллектора двигателя являются механическое трение, электрическая эрозия из-за искрения, термическое и химическое воздействие. Эти факторы усиливаются при неправильной эксплуатации и техническом обслуживании электродвигателя.
Типичные неисправности коллектора
В процессе эксплуатации коллектор двигателя подвергается интенсивному износу. Это приводит к типичным неисправностям:
- Потертости и задиры на поверхности ламелей. Приводят к увеличению переходного сопротивления и искрению в местах контакта щеток с коллектором.
- Канавки и борозды на ламелях. Образуются из-за механического трения и электрической эрозии, вызывают неравномерность магнитного поля и вибрации при вращении ротора.
- Пригорание и оплавление пластин. Происходит при сильных токах и нагреве коллектора, приводит к росту переходных сопротивлений в местах контакта с щетками.
Перечисленные дефекты коллектора двигателя вызывают дополнительное искрение, снижение мощности и КПД электродвигателя, вибрации и шум. Это требует проведения ремонта или замены коллекторного узла.
Другие типичные неисправности:
- Повреждение изоляции между ламелями, замыкание соседних пластин.
- Ослабление посадки коллектора на валу, биение при вращении.
- Искрение и подгорание изоляционных прокладок между пластинами.
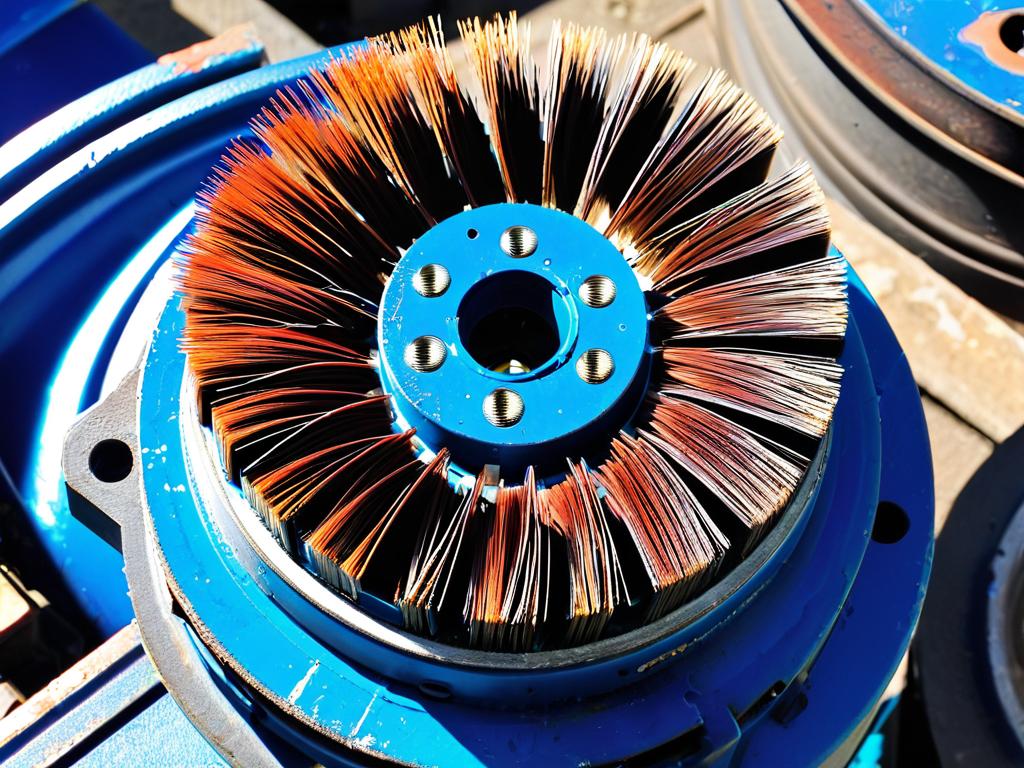
Ремонт коллектора
При значительном износе коллектора двигателя требуется его ремонт или замена. Рассмотрим основные способы восстановления работоспособности коллекторного узла.
Шлифовка и точение коллектора
Наиболее распространенный ремонт коллектора заключается в механической обработке его поверхности. Существует несколько способов: шлифовка наждачной бумагой, точение на специальном станке, протягивание абразивного бруска между ламелями. Такая обработка позволяет восстановить ровную гладкую поверхность коллектора и устранить дефекты (задиры, канавки, пригары).
Пропитка коллектора
Для восстановления изоляции между пластинами и уменьшения переходных сопротивлений применяется пропитка коллектора специальными составами. Наиболее распространены пропитки на основе эпоксидных или перхлорвиниловых смол.
Установка компенсационных прокладок
Если толщина ламелей после обточки становится меньше допустимой, устанавливаются специальные компенсационные прокладки между пластинами. Это позволяет восстановить необходимый размер коллектора без замены всего узла.
Перечисленные способы позволяют отремонтировать коллектор двигателя и значительно продлить срок его службы. Но со временем все равно потребуется полная замена изношенного коллекторного узла на новый.
Профилактика и правильная эксплуатация
Для предотвращения преждевременного износа коллектора двигателя и продления срока службы необходимо регулярно проводить профилактические мероприятия:
- Периодическая очистка коллектора от загрязнений. Удаление пыли, грязи и масляных отложений позволит избежать ускоренного механического износа.
- Проверка состояния изоляции между ламелями коллектора. При нарушении изоляции необходимо устранить токи утечки и восстановить изоляцию с помощью специальных лаков.
- Контроль нагрева коллектора с помощью пирометра. При превышении 80°C следует выявить и устранить причину перегрева.
- Проверка состояния подшипников вала коллектора. Изношенные подшипники вызывают вибрацию вала, что приводит к ударам щеток и быстрому разрушению коллектора.
Также важны правильные условия эксплуатации и режимы работы двигателя:
- Исключение длительных или частых пусков при больших токах, вызывающих перегрев коллектора.
- Недопущение работы с превышением номинальной мощности и оборотов вала двигателя.
- Обеспечение чистоты и отсутствия влаги в месте установки двигателя, защита от пыли и стружки.
- Выбор оптимального давления щеток на коллектор и материала щеток.
Замена щеток
Щетки являются элементом коллекторного узла, непосредственно контактирующим с вращающимся коллектором. Со временем щетки изнашиваются и требуют замены. Рассмотрим основные моменты, касающиеся замены щеток коллекторного электродвигателя.
Причины замены щеток
Основными причинами, вызывающими необходимость замены щеток, являются:
- Износ щеток. Постоянное трение о вращающийся коллектор приводит к истиранию материала щеток.
- Замасливание или загрязнение щеток. Ухудшается контакт со щеткодержателем или коллектором, возрастает переходное сопротивление.
- Повреждение пигталиевых пружин щеток. Нарушается усилие прижима щеток к коллектору.
Периодичность замены
Для коллекторных двигателей периодичность замены щеток составляет в среднем 1500-2500 часов работы. На практике щетки часто меняют по мере выработки, ориентируясь на визуальное состояние.
Особенности замены щеток
Главными особенностями при замене щеток коллектора двигателя являются:
- Контроль давления щеток для обеспечения стабильного контакта с коллектором без чрезмерного нажатия.
- Выбор материала щеток (электрографит, электрокорунд, медно-графитовая смесь) в зависимости от мощности двигателя.
- Соблюдение полярности установки щеток в зависимости от направления вращения коллектора двигателя.
- Проверка состояния и замена изношенных щеткодержателей.
Признаки неисправности коллектора
Во время эксплуатации коллекторного электродвигателя важно своевременно определять признаки неисправностей коллектора. Это позволит предотвратить выход из строя двигателя и провести необходимый ремонт.
Основные признаки неисправного коллектора:
- Повышенное искрение на коллекторе при вращении ротора.
- Появление характерного запаха гари из двигателя.
- Наличие копоти на поверхности коллектора.
- Повышенный шум и вибрация при работе двигателя.
- Снижение мощности и частоты вращения ротора двигателя.
Внешние проверки коллектора:
- Проверка целостности изоляции между ламелями коллектора.
- Контроль биения коллектора - отклонение от соосности с валом более 0,01 мм указывает на неисправность.
- Проверка состояния рабочей поверхности коллектора - наличие значительных задиров, подгара, эрозии свидетельствует о необходимости ремонта.
Обточка коллектора
Коллектор двигателя является одним из самых важных узлов, от которого напрямую зависит работоспособность мотора. Со временем графитовые контактные кольца коллектора изнашиваются под воздействием щеток. Это приводит к повышенному искрению в зоне контакта щетка-коллектор, ухудшению коммутации и как следствие - к снижению мощности и перегреву двигателя. Поэтому периодическая профилактическая обточка коллектора является обязательной процедурой для поддержания коллекторного электродвигателя в работоспособном состоянии.
Признаками необходимости обточки коллектора являются: сильное искрение в зоне контакта щеток с коллектором, появление канавок и неровностей на поверхности коллекторных колец, заметное потемнение изоляционных промежутков между контактными кольцами. Все эти признаки свидетельствуют об интенсивном износе коллектора и необходимости его восстановления методом обточки.
Процесс обточки коллектора довольно трудоемкий, но при соблюдении технологии и использовании правильного инструмента не вызывает особых затруднений. Для этой цели используют специальные коллекторные токарно-винторезные станки или обычные токарные станки с приспособлениями для крепления ротора. В качестве режущего инструмента применяют алмазные резцы или надфили. Глубина резания должна быть минимальной, в пределах десятых долей миллиметра за один проход.
Первоначально производится черновая обточка всей поверхности коллектора до получения равномерной и гладкой поверхности без видимых дефектов. Затем выполняется чистовая обточка с минимальным снятием материала для окончательного восстановления идеально ровной зеркальной поверхности. После обточки необходимо тщательно зачистить пазы между коллекторными пластинами и продуть сжатым воздухом для удаления металлической пыли. Коллектор должен быть чистым, сухим и без следов масел.
Правильно выполненная обточка коллектора позволяет значительно продлить срок службы коллекторного электродвигателя. Эта процедура должна входить в перечень обязательных профилактических работ при техническом обслуживании машин и механизмов с коллекторными моторами.
Правила безопасности при работе с коллектором
Работа с коллектором электродвигателя требует строгого соблюдения правил техники безопасности, так как связана с опасностью поражения электрическим током. Прежде чем приступать к любым работам с коллектором, необходимо полностью обесточить двигатель, отсоединив его от сети и убедившись в отсутствии напряжения. Работать следует в диэлектрических перчатках, используя изолированный инструмент.
При шлифовке и зачистке коллектора обязательно надевать защитные очки - летящие частицы медной пыли и абразива могут повредить глаза. Также рекомендуется работать в респираторе или маске, чтобы не вдыхать вредную коллекторную пыль. Стружку и пыль после обработки коллектора следует тщательно убрать с помощью пылесоса.
При установке нового коллектора нужно быть предельно аккуратным и строго соблюдать моменты затяжки крепежных болтов, чтобы не деформировать коллектор и не нарушить балансировку ротора. Новый коллектор перед установкой должен быть тщательно очищен от консервирующей смазки.
Особо осторожно следует обращаться с щетками, не допуская их падения и ударов. Щетки из хрупкого электрографита легко ломаются. Перед установкой новых щеток необходимо зачистить контактные поверхности держателей надфилем для обеспечения надежного электрического контакта. Щетки должны свободно двигаться в держателях и прижиматься к коллектору с оптимальным усилием.
Восстановление изоляции между коллекторными пластинами производится с помощью специальных изоляционных лаков. При этом важно не допустить попадания лака на рабочую поверхность коллектора, иначе это приведет к нарушению контакта щеток с коллектором. Работы по нанесению и сушке изоляционного лака следует проводить в хорошо проветриваемом помещении с использованием средств защиты органов дыхания.
Таким образом, соблюдение всех правил техники безопасности является обязательным условием для безопасного проведения любых работ с коллектором электродвигателя и сохранения здоровья обслуживающего персонала.