Технологический процесс изменения размеров и форм деталей, как правило, не обходится без такого вида механической обработки, как зенкерование. В переводе с немецкого, слово означает "проходить", "углублять". Если говорить точнее, то это процесс, во время которого увеличивают диаметр отверстий. Его можно сравнить с рассверливанием. Зенкерование – это механическая операция, во время которой производится растачивание отверстий, с целью повышения качества их поверхности и точности.
Получение отверстий
Для того чтобы досконально разобраться в том, что такое зенкерование, необходимо иметь представление, как делают отверстия в деталях. Допустим, в заготовке необходимо просверлить отверстие пятого класса точности диаметром 12 мм.
Для этого понадобится сверлильный станок и 3 рабочих инструмента: сверло, зенкер и развертка. Каждый из них предназначен для обработки проходов, ведь сверление зенкерование, развертывание – это операции очень похожие между собой. В первую очередь в заготовке проделывают отверстие при помощи сверла, однако диаметр его будет значительно меньше необходимого, допустим в половину – 6 мм.
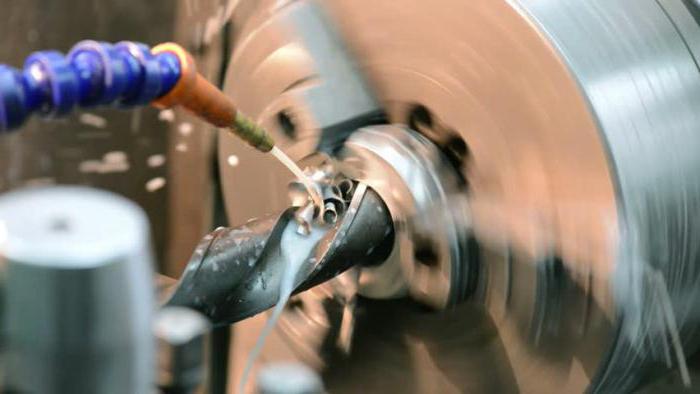
Это будет черновая обработка. Далее его рассверливают зенкером до необходимого диаметра 12 мм (получистовая операция). Кроме того, зенкерование обеспечит 7 класс точности.
Для того чтобы отверстие было 5 класса, необходимо использовать развертку. Она обеспечит необходимые предельные размеры и припуск – чистовая и завершительная обработка отверстия. Зенкерование и развертывание, как правило, выполняют на один и тот же диаметр, различаются лишь предельные размеры, и, поскольку развертка обеспечивает более низкий класс точности, припуск на развертывание выбирают с высокой точностью.
Зенкерование и зенкование
Очень часто данные понятия путают между собой из-за того, что они очень похожи в названиях. Однако, если зенкерование – это процесс, во время которого зенкер растачивает отверстие на всю глубину, то зенкованием называют обработку верхней его части.
Это необходимо для образования углублений под потайные головки элементов крепления (болты, заклепки, винты). Зенковка – инструмент для зенкования, отличается от зенкера формой рабочей части.
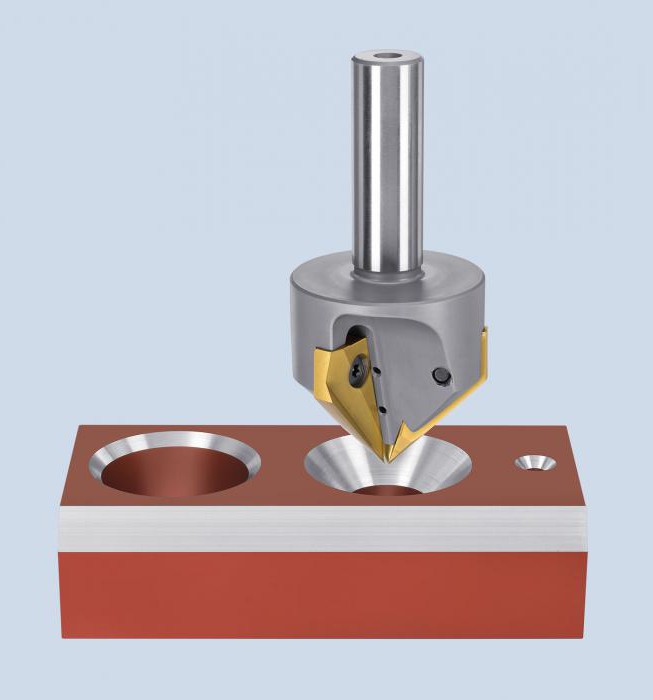
Материал и виды зенкеров
Как и любой другой режущий инструмент, зенкер классифицируется по типу конструкции, по форме и виду обработки, а также по материалу, из которого его изготавливают.
Поскольку данный инструмент обладает высокой жесткостью, как правило, его делают из быстрорежущей стали, однако нередко можно встретить зенкера из конструкционного легированного (40Х) и углеродистого (Ст45) сплава.
Зенкерование - это сглаживание и очищение поверхности, поэтому сам инструмент имеет большое количество режущих кромок. Зенкеры могут быть хвостовыми сборными с вставными ножами, хвостовыми цельными, насадными сборными и насадными цельными.
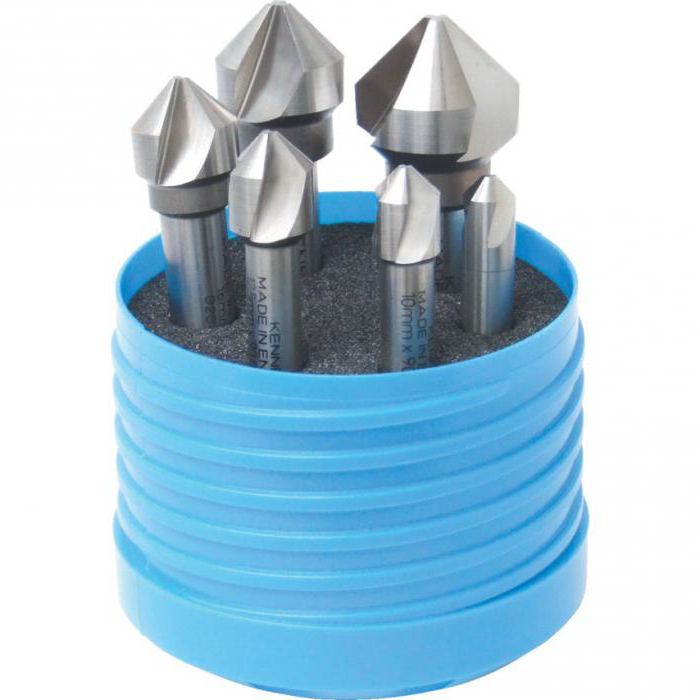
Если рассматривать с точки зрения экономичности, то, конечно же, сборные инструменты имеют более высокую стоимость, но и срок их эксплуатации гораздо больше, поскольку вышедшие из строя кромки можно заменить.
Длина и диаметр
Поскольку сверление, зенкерование - процессы довольно похожие, то сверло (в особенности это касается спиральных сверл) и зенкер имеют практически одинаковое строение. Каждый из инструментов имеет режущую часть, которая непосредственно делает отверстие в детали.
Различие состоит в том, что у зенкера нет поперечной режущей кромки, но имеется от трех до шести зубьев. Его рабочая часть состоит из калибрующей и режущей составляющих. Длина второй зависит от глубины зенкерования. Калибрующая часть – это продольные ленточки вдоль режущей кромки. Их ширина зависит от диаметра зенкера (0,8-2,5 мм), а высота – 0,2-0,9 мм.
Зенкерование – это механическая операция, похожая на рассверливание. Если же её целью является растачивание отверстия для последующего развертывания, то диаметр зенкера выбирают меньше, с учетом припуска на последнюю чистовую операцию. К тому же, поскольку требуемая точность этого инструмента ниже, чем для развертки, абсолютные значения отклонений могут быть гораздо больше.
В другом случае зенкерование отверстий – это и есть последняя чистовая обработка, требуемая для детали с допуском по 11, 12 квалитету. Тогда инструмент выбирают с учетом разбивки и запаса на изнашивание, а его диаметр должен соответствовать диаметру отверстия.
Проектирование и расчет
Для того чтобы диаметр необходимого отверстия был максимально точным, выполняют проектирование зенкера. Таким образом можно найти максимальный и минимальный диаметр необходимого инструмента, определить материал его режущей части и выполнить расчет режимов резания.
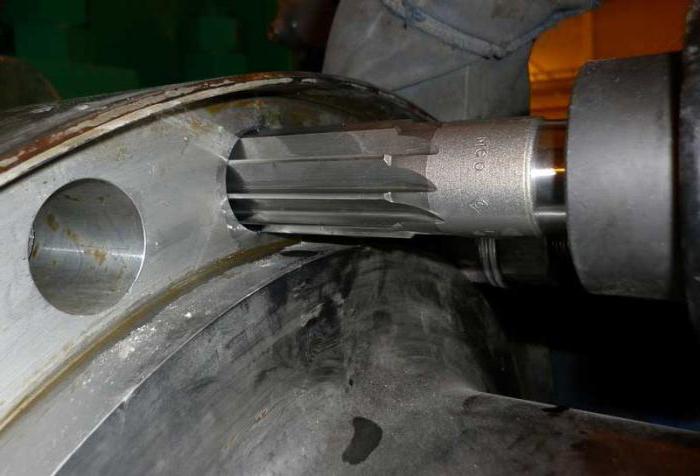
Важный показатель, который влияет на максимальные и минимальные значения – это требуемый квалитет. Например, необходимо выполнить чистовое зенкерование отверстия на диаметр 85 мм с квалитетом Н11. Исходя из таблиц полей допусков отверстий при номинальных размерах от 1 до 500 мм, для 11 квалитета (для диаметров от 80 мм до 120 мм) поле допуска составляет: верхнее значение – «+220», а нижнее –«0», то есть 85 +220мм. Максимальный диаметр рассверливаемого отверстия не может превышать 85,22 мм, а минимальный – 85 мм.
При этом допуск на размер — это разница между Dmax и Dmin, то есть он будет составлять 0,22 мм. Если же говорить о браке, то для отверстия неисправимым будет считаться диаметр выше значения 85,22 мм, а исправимым – меньше 85 мм.