Жаростойкость и жаропрочность являются очень важными характеристиками. Некоторые изделия машиностроения работают в очень сложных условиях при повышенных температурах. Обычные конструкционные стали при нагреве скачкообразно меняют свои механические и физические свойства, начинают активно окисляться и образовывать окалину, что совершенно неприемлемо и создает угрозу выхода из строя всего узла, а возможно, и серьезной аварии. Для работы при повышенных температурах инженеры-материаловеды при помощи металлургов создали ряд специальных сталей и сплавов. В данной статье дается их краткая характеристика.
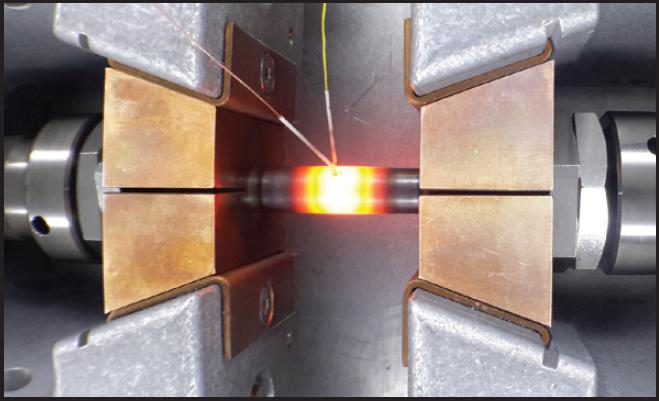
Жаропрочные стали
Многие люди отождествляют понятие жаростойкости с таким понятием, как жаропрочность. Этого делать ни в коем случае нельзя. Жаропрочность еще называют красноломкостью. И под этим понятием подразумевают способность металла (либо сплава) сохранять высокие механические свойства при работе в условиях повышенных температур. То есть такой металл, даже будучи нагретым до красного свечения (оно характерно для температур выше 550 °С), не поползет и сохранит достаточную жесткость.
Говоря простым языком, жаропрочность – это способность материала сохранять работоспособность при нагреве до высоких температур. Обычные конструкционные стали даже при незначительном нагреве становятся пластичными, что исключает возможность их применения для изготовления изделий, работающих при высоких температурах.
Разные марки металлов и сплавов обладают различной жаропрочностью. Этот показатель зависит от химического состава материала. Испытания на жаропрочность могут проводиться на протяжении длительного времени. Но чаще всего образцы, нагретые в печи до определенной температуры, испытывают на растяжение в течение короткого отрезка времени.
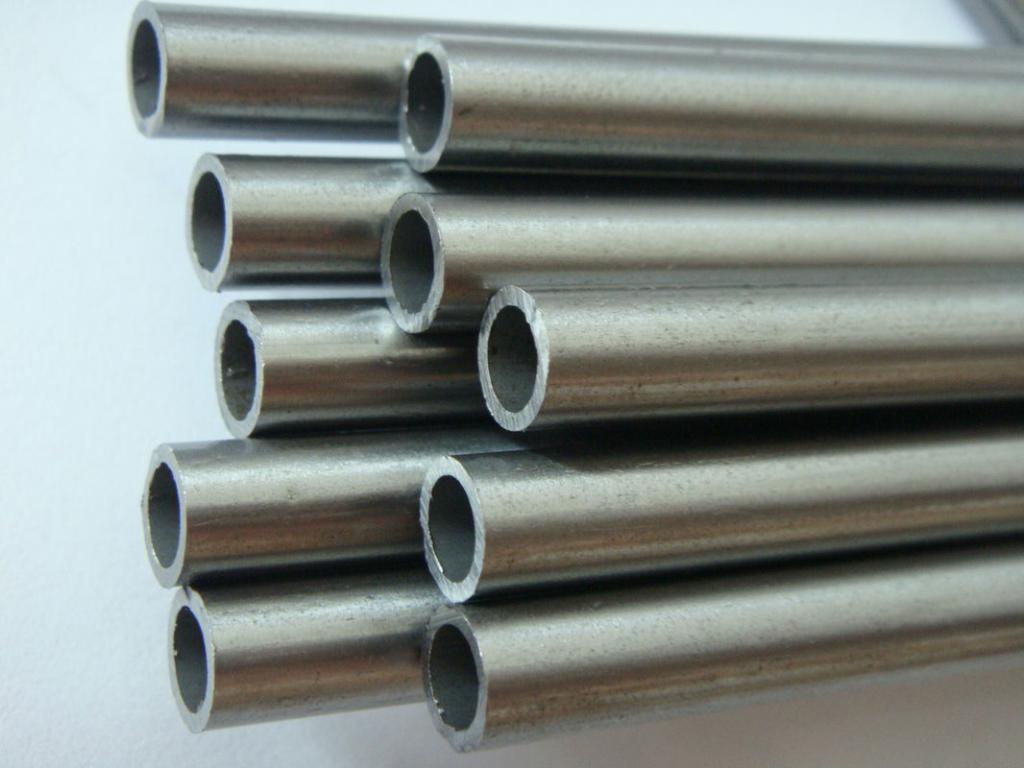
Жаростойкие стали
Жаростойкость, в отличие от жаропрочности, – это способность материалов противостоять развитию коррозионных процессов при работе в условиях высоких температур. Обычные стали, если их подвергнуть нагреву (за исключением термической обработки в защитной атмосфере или в вакууме), начинают окисляться. Кроме того, при длительном нагреве углерод на поверхности изделия начинает выгорать. В результате поверхность обедняется углеродом, что приводит к резкому изменению механических свойств (прежде всего, твердости) на поверхности. Износостойкость падает. Получает развитие такое негативное явление, как задиры. Данная группа сталей может работать при температурах около 550 °С.
С целью увеличить жаростойкость стали, ее расплав легируют кремнием, алюминием и хромом. Иногда достаточно повысить жаростойкость поверхности детали. В таком случае прибегают к силицированию или алитированию (насыщению поверхностного слоя соответственно атомами кремния или алюминия) в порошковой среде.
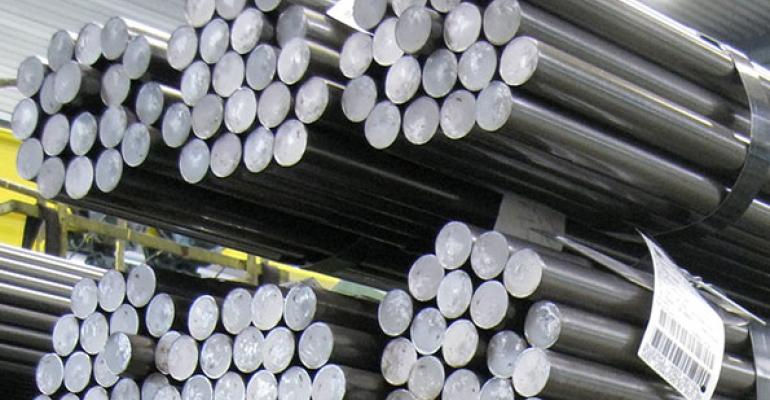
Материалы с высокой температурой плавления
При эксплуатации в условиях особенно высоких температур рассмотренные материалы не могут использоваться, так как при температуре в районе 2000 °С начинает протекать оплавление (выделяется жидкая фаза). Для этих целей используют тугоплавкие металлы: вольфрам, ниобий, ванадий, цирконий и так далее. Эти материалы довольно дорогие, но инженеры еще не нашли для них достойной альтернативы.
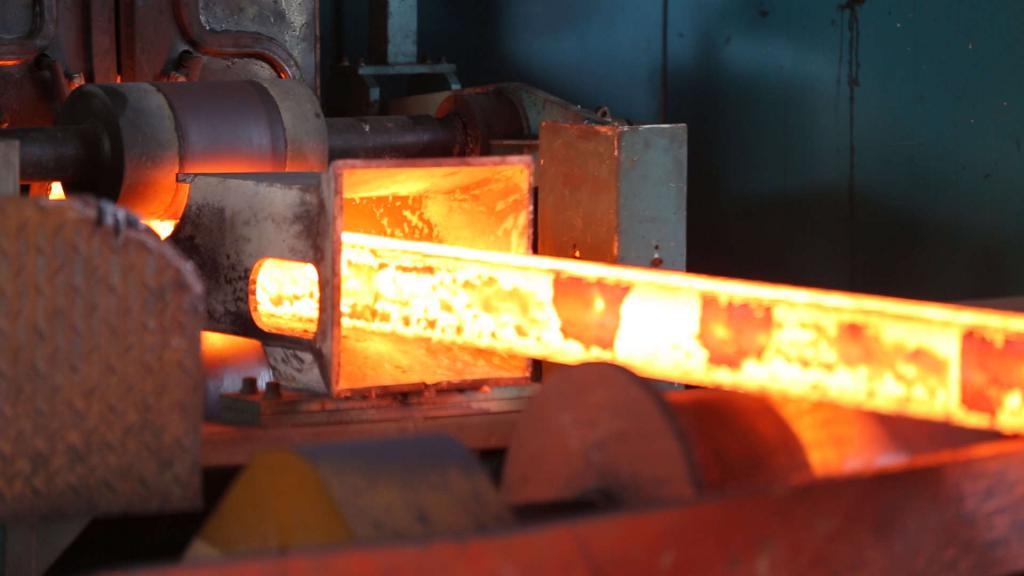
Характеристика сплавов на основе хрома и никеля
Сплавы, обладающие большой жаропрочностью, очень востребованы в энергетическом машиностроении (лопатки паровых турбин, части двигателей летательных аппаратов и так далее). Причем потребность в подобных материалах постоянно растет. Более того, производство требует от ученых получения все более и более совершенных материалов, способных сохранять свою работоспособность при очень высоких температурах. Поэтому постоянно ведутся работы по увеличению показателей жаропрочности. Никель, точнее легирование этим элементом стали, способствует этому.
Все жаростойкие стали легируются никелем (не менее 65 %). В обязательном порядке имеется и хром. Содержание этого элемента не должно быть менее 14 %. В противном случае поверхность металла будет интенсивно окисляться.
Стали, дополнительно легируются алюминием, ванадием и другими тугоплавкими элементами. Алюминий, например, даже при комнатной температуре покрывается тонкой окисной пленкой, которая препятствует проникновению коррозии вглубь металла. То есть не образуется окалина.